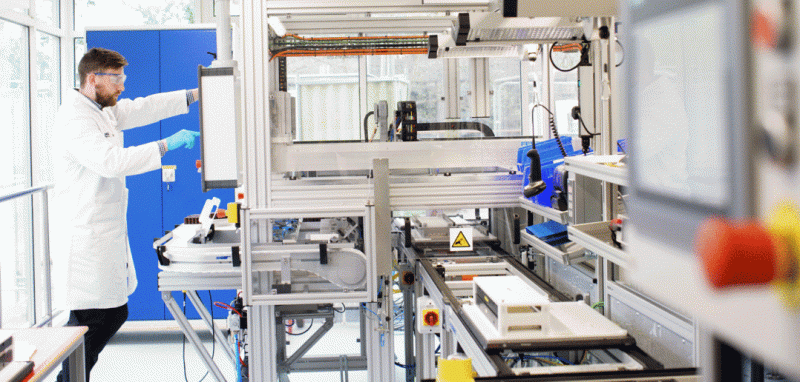
Siemens’s automation controls architecture, PLCs, networks and operator interfaces are playing a central role in a project aimed at increasing the UK’s knowledge and capability in support of design and production methods for modular battery systems.
The relatively small volumes required to manufacture battery packs for niche or new market hybrid and electric vehicles has meant that UK manufacturers have historically avoided this market. But as demand increases for more sustainable transportation solutions, and sales of electric vehicles surge, moves are being made to provide a flexible manufacturing solution for UK companies embarking on the production of batteries for vehicle electrification.
A project to demonstrate that the commercial production of scalable battery packs is both feasible and cost competitive has been underway since 2015 under the direction of WMG, at the University of Warwick, and funded by Innovate UK.
It has brought together a consortium of interested parties which over the past three years has developed a modular, scalable production facility that reconciles the aspects of production efficiency against configurability at an affordable cost. The project is also laying the foundations for an extendable approach to future data-led connectivity for data collection, work instructions and cloud analytic capability.
The pilot project focused on solutions for a range of sectors where a scalable, modular, pack-centered solution around cylindrical cells was appropriate. Looking initially at packs of 18650 cells, the project has now entered its second stage – AMPLiFII and is currently working with 21700 cells in order to suit the evolving needs of customers looking at the technology and production outcomes.
The production line incorporates a modular extendable control network supplied by Siemens. It has the ability to scale as required and also the connectivity capability to enable it to be progressively extended and integrated with wider production equipment, as well as with Siemens cloud-based platform, Mindsphere.
The work underway is taking place within WMG’s Energy Innovation Centre (EIC). It is looking at battery research and development from cell level through to full-scale model and pack pilot line production, in order to ultimately enhance UK capability in this important area.
Prof. Robert Harrison, professor of automation systems at WMG, University of Warwick, is in charge of the project. “This project will help to develop the next generation of traction batteries for electric and hybrid vehicles. The UK government recognizes that it is critical for the UK to embrace the opportunity created by the shift to electric vehicles,” he said.
“AMPLiFII allows us to demonstrate our ability to automate the cell-to-module packaging process and help pave the way to full production. With the help of our partners such as Siemens we are developing the new knowledge, skills, technology and facilities to support UK industry as it seeks to use new technologies and processes in vehicle battery systems.
“The system provides significant benefits to UK companies entering the battery manufacturing market and enabled a range of end users to have a cost-effective entry point.”
作者:RACHEL EVANS