摘 要:提出一种线控制动系统的设计方案,通过试验验证该线控制动系统的制动压力控制及响应能力。该系统具备稳 态压力控制精度≤ ±200 kPa,最大目标压力响应速度≤ 180 ms,作为 AEB 主执行器,比 ESC 具备更高的控制精度和 更快的响应速度。
AEB 感知系统选用一种国内自主开发的 77G 毫米波雷达并进行测试验证,该雷达最多可同时追踪 64 个前向目标,并可对高度目标、行人 / 自行车目标进行有效识别。运用 Matlab/Simulink 及 Vector/CANoe 设计了 AEB 功 能软件模块,为提高紧急制动效果,提出以制动距离为控制目标的功能逻辑,通过实车试验对所设计的 AEB 系统进行 了验证。
关键词:线控制动;毫米波雷达;AEB;快速控制原型
1 AEB 系统方案
本项目确定了以下 AEB 系统架构:传感器选 用 77 G 毫米波雷达,主要用于目标检测,具备探测距离远、距离精度高、中远程自动切换的优势, 可追踪多达 64 个目标;制动执行机构为线控电子液 压制动系统(Electric Hydraulic Brake,EHB),并 集成 AEB 功能算法;量产方案中 ESC 作为 EHB 的 压力备份冗余以及车辆信息交互。系统架构原理如 图 1 所示。
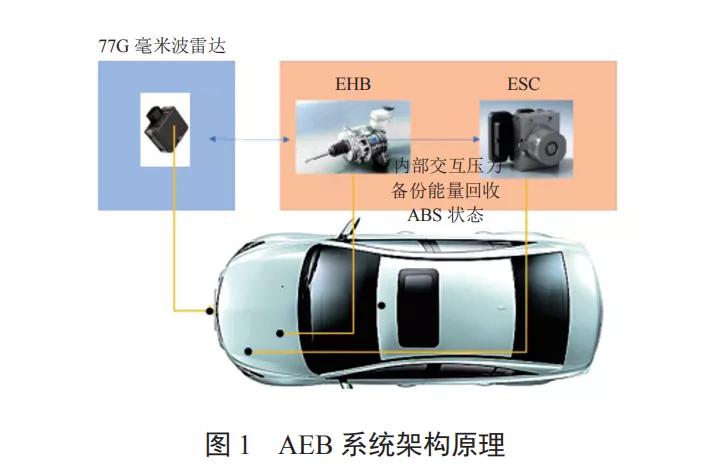
2 线控制动系统设计
2.1 线控制动系统方案原理
当前已具备成熟量产 EHB 能力的企业多数为外 资厂商。国内汽车零部件企业和高校进行了预研和 产品开发工作,国内如浙江亚太、万向集团、上海 拿森、同济同驭、清华大学、吉林大学、北航等都 开展了 EHB 产品的理论研究及产品试制开发工作。
设计开发了一种线控制动系统(属于 EHB 线 控制动分类),该样机开发英文简称为 WBS(Wire Brake System),原理如图 2 所示。
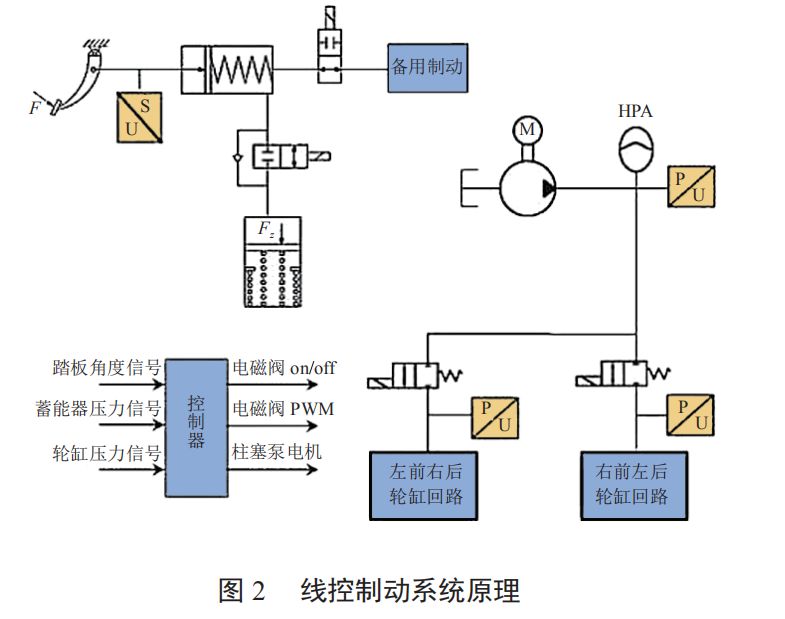
WBS 系统工作原理:常规制动工况下驾驶员 采取制动时,踩下制动踏板,控制器通过读取踏板 角度信号确认车辆制动需求,常开型制动主缸隔离 电磁阀上电关闭,模拟器常闭电磁阀上电打开,制 动主缸油液通过模拟器常闭电磁阀进入模拟器主 缸,并由制动主缸和模拟器主缸共同作用反馈合适 的制动脚感。
线控制动系统制动力源由电动柱塞泵 提供,并由高压蓄能器储压,以减少油泵工作次数 并提高系统压力响应速度。控制器通过判断踏板角 度传感器等信号,控制电磁阀开度及柱塞泵工作, 按照控制逻辑控制线控制动系统输出相应制动力, 此时制动踏板和制动力是完全解耦的。如果线控制 动系统发生故障,进入备用制动状态,控制器控制 制动主缸隔离电磁阀断电打开,模拟器常闭电磁 阀断电关闭,模拟器停止工作,此时制动油液通过 制动主缸和制动主缸隔离电磁阀直接进入备用制 动回路,提供车辆备用制动力。
对于 ADAS 系统 (AEB、ACC 等)所需的减速度或制动力请求, 可直接发送目标给 EHB 控制系统,由 EHB 控制器 进行减速响应 [6-7]。
2.2 线控制动系统台架及装车验证
对所设计的 WBS 线控制动系统进行了台架验 证,台架包括:轮缸、制动管路、线控制动模块、 踏板等,其中轮缸压力、踏板转角、踏板力可通过 传感器采集至示波器,线控制动模块相关制动压力 目标或反馈信号可通过 CAN 线与上位机通讯。
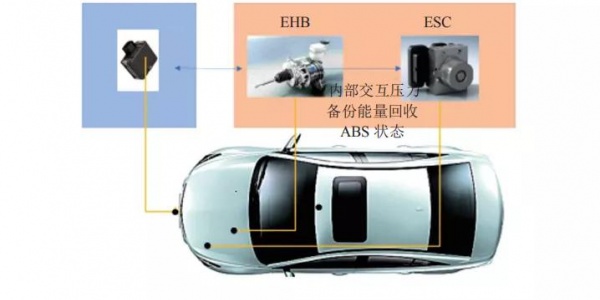
实车装车过程对原车制动踏板、制动主缸、真 空助力器进行了替换,通过 CAN 通讯方式采集线 控制动系统相关信息。
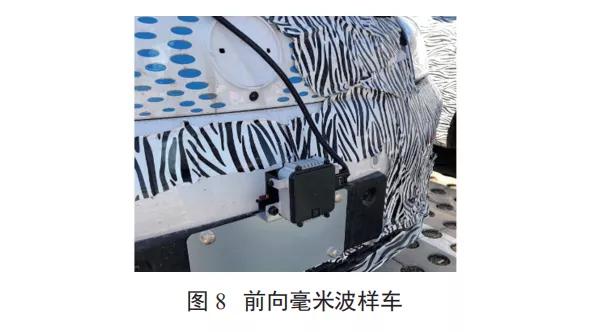
通过试验验证了该线控制动系统具备较高的 压力控制精度(稳态≤ 200 kPa),快速的压力响 应(0 ~ 8 000 kPa ≤ 180 ms),与 ESC 相比较在 响应时间、响应精度上均具备优势,可提高 AEB 系统能力。线控制动系统阶跃响应结果如图 6 所示。
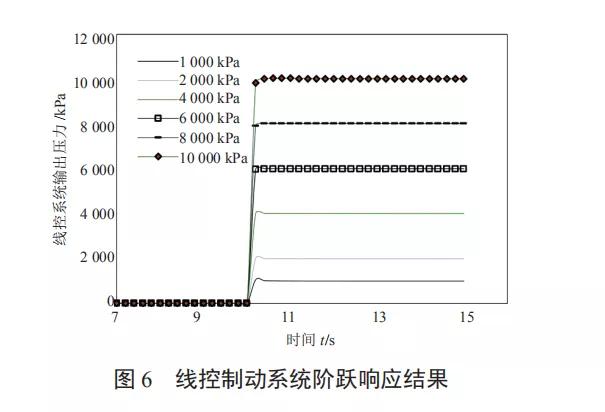
底盘会议相关推荐(点击图片可阅读会议详情)
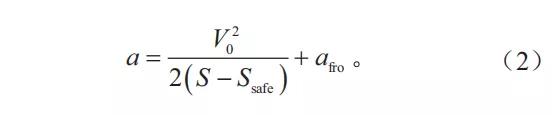
3 环境感知及控制系统设计
3.1 毫米波雷达测试及数据处理
对毫米波目标 CAN 数据进行解析,获取帧 ID、检测到的目标个数、目标的序号及其置信度、 横向位置、横向速度、纵向位置、纵向速度等数据。对解析出来的检测目标进行筛选,去除无效目标、 高度目标、筛选出本车道的候选目标。
雷达在扫描 期间偶尔会出现的非空信号目标,这种信号出现时 间极短,连续性差,偶尔出现的连续数据在数值上 跳动性较大,没有实际意义,对目标车辆和防撞预警也会产生影响,因此需要去除。前方具备通过性 的障碍物目标信息,比如高架桥、减速带、限高杆、 指示牌等,这些目标出现在毫米波视场范围内时可能 会造成车辆误动作。图7为毫米波雷达主要筛选算法。
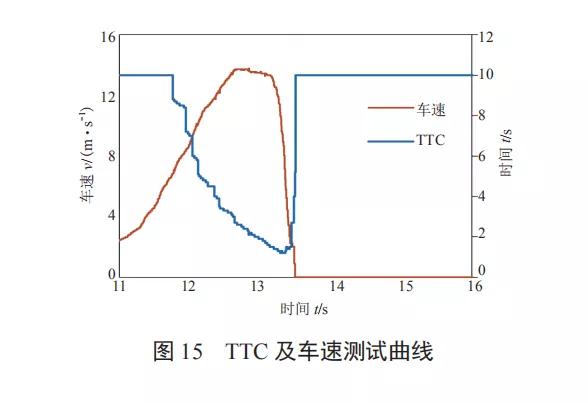
3.2 毫米波雷达实车输出测试
毫米波雷达目标筛选和处理后,完成毫米波雷 达装车并进行各路况测试,同时编写上位机程序用 以显示目标检测效果。
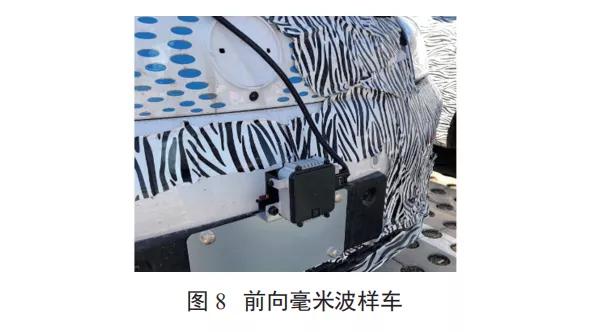
该雷达具备较好的目标识别能力,通过实际路 况测试,对具备高度信息的障碍物(如广告牌、减 速带)能识别并过滤,对成人目标可做到有效识别。在完成毫米波雷达输出信号准确度确认后, 在毫米波雷达输出 CAN 信息中增加一路 CAN ID 信息,其中涵盖危险目标的碰撞时间(Time to Collision,TTC)计算等相关信息,可作为 AEB 功 能算法输入。
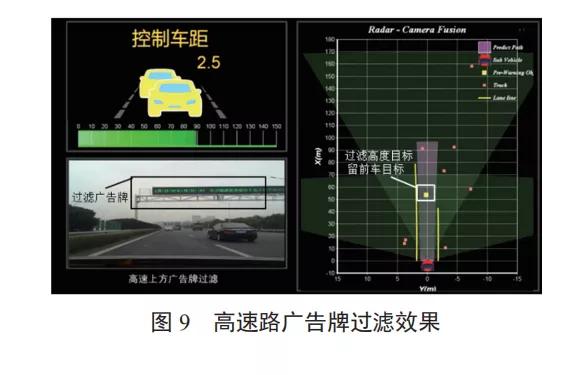
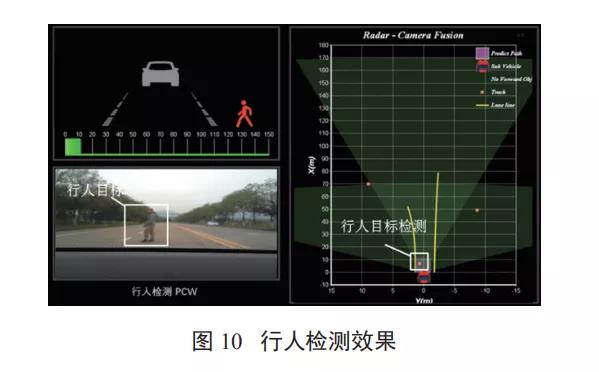
4 AEB 系统功能实车验证
4.1 AEB 系统控制策略设计
AEB主要功能逻辑如图11所示,主要包含:
(1) TTC 及制动压力算法;
(2)激活及抑制条件。首先判断是否满足 AEB 激活条件,如:车速>0, 挡位处于 D 挡,EPS 方向盘转角是否回位等,如 全部满足则输出 TTC 给 AEB 系统进行制动压力的 计算,如不满足则 AEB 功能被抑制或退出。设定 TTC 触发值,如果实际 TTC 值<触发值,则认为 AEB/FCW 功能被触发,由线控制动系统执行制动 压力计算值,完成紧急制动执行动作。
在紧急制动 执行过程中,如果满足 AEB 抑制条件,如:驾驶 员主动转向避险、加速踏板明显被踩踏等,都认为 驾驶员主动干预,AEB 功能将被抑制。
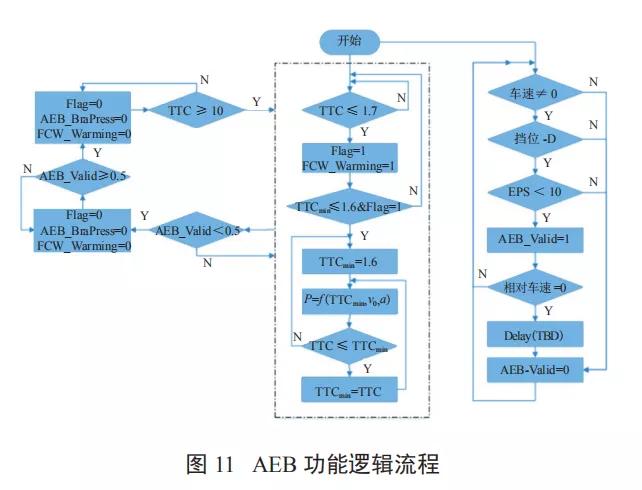
以 ESC 为执行器的 AEB 系统因其压力控制精 度较低、响应慢,TTC 触发多采用最大制动减速度 保证制动安全,但这会造成制动舒适性及驾驶员安 全感降低。
所设计的以线控制动为执行器的 AEB 系统采 用制动安全距离为控制目标,可根据实际工况实时 调节制动减速度,可明显改善制动效果及舒适性。设 TTC 触发时,两车相对速度为 V0,两车相 对距离为 S0,相对安全距离目标为 Ssafe,前车减速 度为 afro(目标信息可由毫米波雷达提供),本车减 速度为 a,根据动力学公式:

本车减速度控制目标:
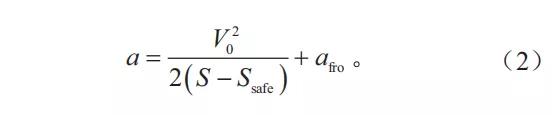
进一步考虑整车模型、道路、制动系统模型等, 得到轮缸制动压力 P 与本车制动减速度目标 a 的解 析关系:

式中:dw 为轮缸直径;BF 为制动效能因数;n 为单 轮轮缸数量;r 为制动有效半径。根据所匹配的实际车型参数,换算关系为 P a = × 70.628 8 P a = × 70.628 8 。
Vector 公司的 CANoe 具有强大的 CAN 总线设 计及仿真功能,借助 CANoe_Simulink 软件接口, 可使Simulink控制模型与整车CAN网络实时通讯, 搭建快速控制原型,验证算法的实时性和可靠性, 联合模型如图 12 所示。
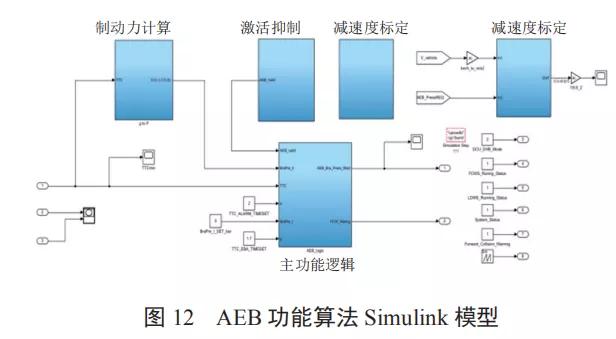
4.2 AEB 系统功能测试
在封闭场地对 AEB 样车进行功能测试验证, 试验设备构成如图 13 所示。在 10 ~ 40 km/h 本车车速范围内,对前静止目标进行AEB功能随机测试, 相关试验数据通过数据记录仪进行记录和分析。
如图 14 所示,AEB 功能执行过程中,为控制 制动距离,由 TTC 直接计算得到的制动力计算值可 能会产生波动或减小,通过 AEB 功能算法保证制 动力不减,并根据危险程度降低做实时制动力值更 新,AEB 制动结束时刻之后,适当延时制动力输出, 维持制动效果。
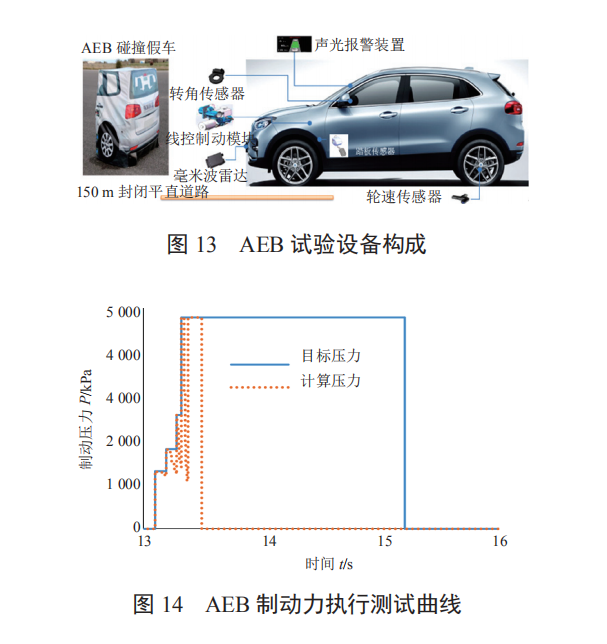
如图 15 所示,试验结果基本体现了 AEB 预期 功能策略。制动力目标值与 TTC 值有函数关系, TTC 检测精度对制动力目标有较大影响,这会影响 实际制动精度及制动舒适性,从根源上应优化毫米 波雷达的滤波算法,并且在 AEB 策略输入端也做 好 TTC 真值的校验。
前文中式(3)计算了制动力和整车制动减速 度的关系,但实际测试中发现:仅稳态满足式(3)的结果,实际上由于线控制动系统响应时间、风阻、 载荷等因素的影响,呈现出图 16 所示的制动力与减 速度对应关系,这对AEB制动效果的影响至关重要, 需要据此进行标定。
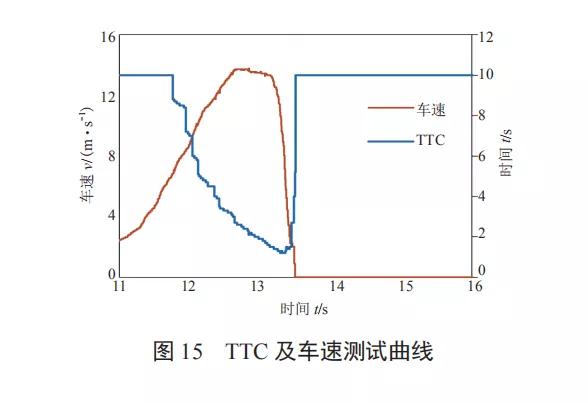
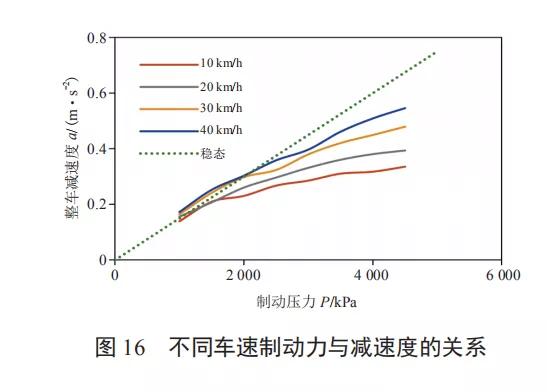
对本车车速 10 ~ 40 km/h 范围内的 AEB 功能 触发效果进行了测试统计,系统能根据不同本车车 速实时调整制动力值,实测制动距离误差在 ±0.5 m 内,制动距离稳定,达到设计目标,如图 17 所示。
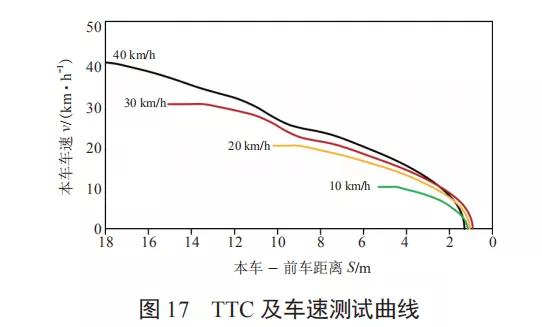
5 结论
设计了一种线控制动系统,台架及实车搭载试 验验证了该线控制动系统制动响应速度和精度的先 进性。所选用的毫米波雷达具备较好的目标距离识 别精度,可有效地输出 AEB 系统所需的危险目标 信息。
设计了 AEB 核心算法中的抑制 / 激活条件、 TTC 触发逻辑、制动力 - 减速度计算、载荷估计等 模块,通过快速控制原型进行实车验证,基本达到 开发目标,为后续量产开发打下了良好的基础。
文章来源:汽车工程学报
文章作者:刘宏伟 ,张 杰 ,朱恩利 ,黄雪梅 ,杨佳飞
来源:汽车工程学报