作者:皮旭明、刘德福
本文从驱动电机外特性曲线、驱动电机与减速器(变速器)的连接方式等方面分析了故障产生的机理,并采集了纯电动汽车道路试验的载荷谱作为设计输入条件,对减速器及内部差速器进行了强度仿真分析,最后提出了典型故障模式的解决方法,提高其可靠性。
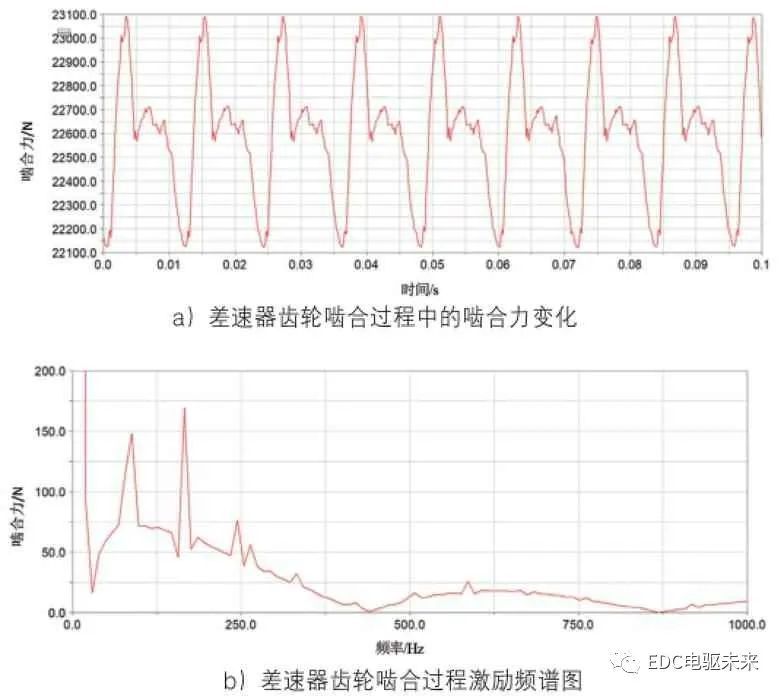
纯电动汽车经过近十年的高速发展,其传动系统的安全性、可靠性问题也值得我们深入研究。纯电动汽车传动系统包括与驱动电机连接的减速器和减速器内含转弯差速的差速器总成。差速器的输出半轴齿轮与驱动半轴相连,纯电动汽车在道路试验及售后使用时常出现差速器故障、驱动半轴断裂、动力中断和转弯异响等问题。
近年来,随着纯电动汽车的高速发展,其减速器可靠性的研究也取得了一些成果。这些研究均基于传统燃油车思维对电动汽车的可靠性进行研究,没有针对纯电动汽车传动系统的特点对其故障原因及可靠性进行分析。本文首先分析了纯电动汽车减速器的一些常见但特有的故障,然后通过理论计算及仿真分析技术,挖掘出纯电动汽车减速器故障的产生机理,提出了一套提高减速器可靠性的方法,并进行试验验证。
一、纯电动汽车减速器的常见故障
从纯电动汽车整车厂、减速器零部件厂收集了传动系统的常见故障问题:差速器行星齿轮断齿、行星齿轮轴断裂、差速器壳体断裂、驱动半轴断裂、减速器壳体以及悬置位置开裂和减速器内轴承出现散架。
二、纯电动汽车减速器失效机理分析
纯电动汽车减速器早期失效概率明显高于传统的燃油汽车,主要原因是驱动电机的外特性曲线与发动机差异较大。如图1所示的驱动电机的特性曲线可知,驱动电机的特点是低转速高转矩。电机低速起步转矩即可达到峰值转矩,在一定的转速区间内,电机的转矩是不变的。转速增加即可进入最大功率恒功率区,随后随转速的增加转矩开始下降。
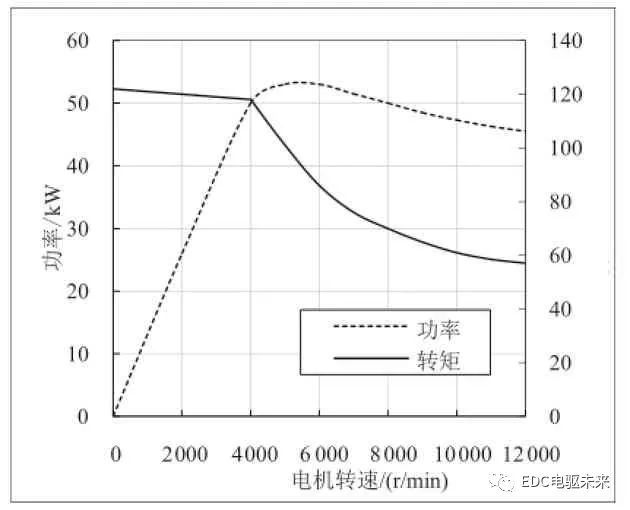
图1 某型号永磁同步电机的外特性曲线
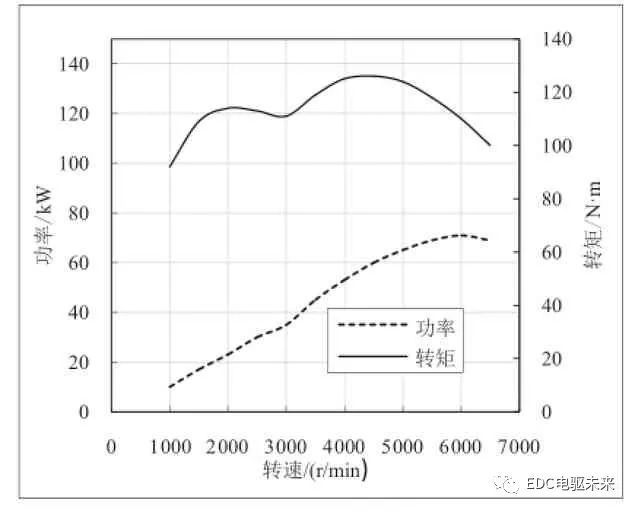
图2 某型号内燃机的外特性曲线
如图2所示的某型号内燃机的外特性曲线中,内燃机的最大转矩需要转速支持,最大功率也需要随转速增加至6 000 r/min时才能到达最大值。传统燃油车起动需要短暂的延迟来实现离合器从分离到接合,而驱动电机和减速器之间是刚性花键连接或一体轴没有离合器,因此纯电动汽车起步明显快于传统燃油车。
而急加速也是如此,传统燃油车动力仍然会有一定延迟,因为变速器需要降档(降档时间需要0.8~1.2 s),这时候动力就会慢一拍。而纯电动汽车减速器没有档位不需要换档,所以提速更快一些。再加上发动机与变速器之间连接有离合器、减振器和双质量飞轮等,对发动机转矩波动有过滤和缓冲,因此纯电动汽车对传动系统的要求更苛刻,这就是同功率同转矩纯电动汽车百公里加速时间比传统燃油车要短的原因,当然,汽车加速度还取决于驱动轮的最大打滑转矩。

汽车行驶方程式为:式中:Ttq为电机输出转矩;i0为主减速器传动比;ig为变速器传动比;ηT为传动效率;r为轮胎半径;G为整车质量;f为滚动阻力系数;α为整车行驶坡度;a'为加速行驶时的加速度;δ为汽车旋转质量换算系数(δ> 1)。
根据汽车行驶的附着条件与汽车的附着率计算公式可得作用在驱动轮上的地面法向反作用力为:
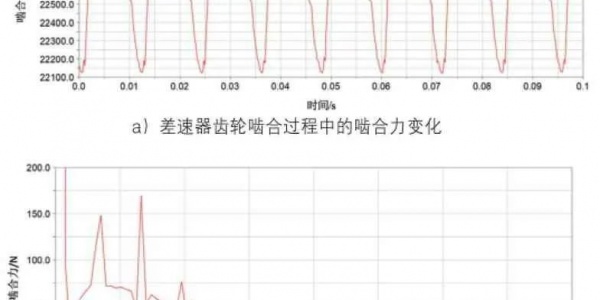
式中:b为汽车质心到后轴的距离;h g为汽车质心的高度;L为汽车轴距。
联立式(1)和式(2)可得:
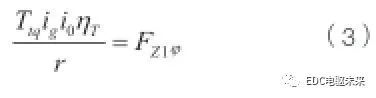
式中:φ为附着系数。
对于前驱轿车而言,当其在一定的坡度上加速行驶时,加速度a' 逐渐增大,作用在驱动轮上的地面法向反作用力F Z1逐渐减小。由于地面对驱动轮切向反作用力F t的极限值,即附着力Fφ与驱动轮法向反作用力FZ1成正比,当加速度a' 达到一个临界值时,则可得:

当驱动转矩继续增大时,F t>FX1 = Fφ= FZ1φ,驱动轮打滑,驱动转矩的这个临界值被称为打滑转矩。联立式(2)、式(3)和式(4)可得到打滑转矩为:
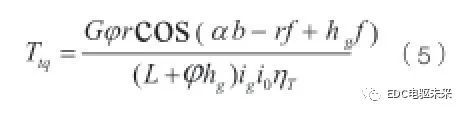
式中:Ttq为电机输出转矩。
对几款前驱纯电动汽车及一款同类型的传统燃油车的最大打滑转矩进行计算,最大驱动力等于前轮附着力FXbmax=Fφ=FZ φ=61.5% mgφ。滚动阻力系数f取0.008 3,附着系数φ取0.9,传动效率ηT取0.95。计算结果见表1。
根据表1可以看出,传统燃油车的1档最大输出转矩接近于轮胎最大打滑转矩,而2档最大输出转矩就远远低于轮胎最大打滑转矩,从驾车习惯来看,1档一般只用于起步和爬陡坡,使用频次并不高,而纯电动汽车可实现大转矩起步、加速超车,使用频次较高,尤其是共享网约车、出租车司机,追求动力性和时间的最大价值,较少考虑电耗、车辆的维护保养,因此对传动系统的要求更加苛刻。
三、纯电动汽车减速器的优化设计
1. 利用载荷谱加速故障过程
由于纯电动汽车减速器的设计载荷谱缺失,一般变速器企业采用《QC/ T 1022-2015 纯电动乘用车用减速器总成技术条件》作为设计载荷谱,但由于该载荷谱与实际载荷谱之间存在着较大差异,比如汽标中载荷谱最大转矩循环时间太长,而反拖发电转矩循环时间太短,未体现加减速冲击载荷等。
表1 不同厂家电动汽车轮胎打滑转矩对比
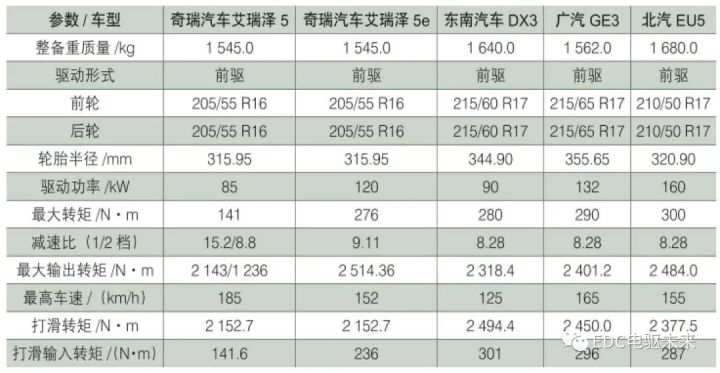
表2 纯电动汽车道路试验载荷谱
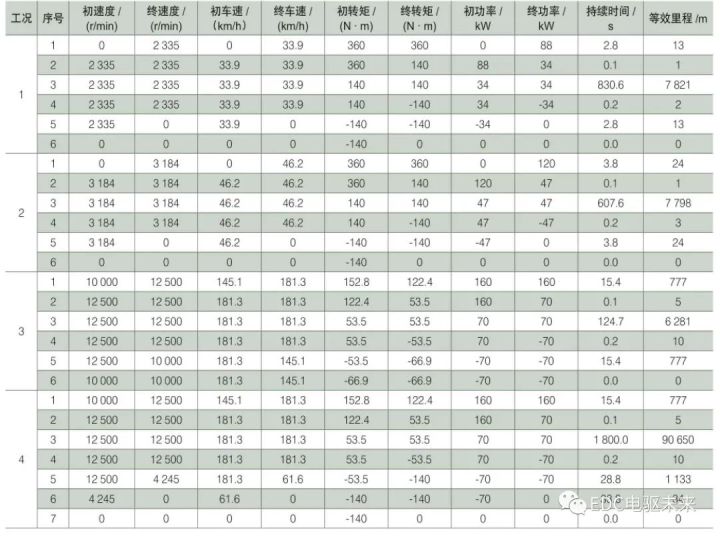
为了得到较为准确的纯电动汽车减速器的设计载荷谱,首先必须依据用户的使用情况以及各种路面情况进行实车道路载荷谱采集。常用的实车道路载荷谱采集方法为常规路面按比例采集法。对于用户实际使用条件下的标准载荷谱,按照我国的道路情况,多采用城市公路、城郊公路、一般公路、高等级公路以及坏路等路面,按照一定比例合成的综合道路载荷谱,从而实现获得与实际使用工况等效寿命载荷谱的目的。表2是通过某纯电动汽车整车道路试验采集的载荷谱,采集了20个工况,选取了4个工况。按照此工况进行完台架试验后,整车道路试验也能一次通过,并且售后故障率很低。
某型号减速器根据疲劳实验工况对轴承基本损伤率进行校核和台架试验,结果均一次性通过,但在整车道路试验时发现输入轴前轴承保持架都散架。而根据疲劳实验工况的CAE分析结果是输入轴前轴承的损伤率远比输入轴后轴承低。后来将输入工况改成表2载荷谱后,CAE分析结果和台架试验都未通过,并且连续三台台架试验样箱的输入轴前轴承保持架都散架。经与轴承厂家联合分析,造成保持架损坏的主要原因是变转矩时的冲击力过大,尤其是高速制动能量回收工况。而高速轴承为尼龙保持架,抗冲击能力差,后来改成钢保持架的轴承后,顺利通过了台架试验和整车道路试验。
2. 提高仿真分析能力,优化设计
利用MASTA软件对电驱动传动系统进行建模,将设计载荷谱输入后,可对壳体应力、齿轮、轴承寿命和NVH等进行仿真分析。
差速器的仿真分析需要联合多体动力学分析软件ADAMS、有限元分析软件Abaqus和有限元前处理软件HyperMesh等,差速器设计的总体技术思路如图3所示。
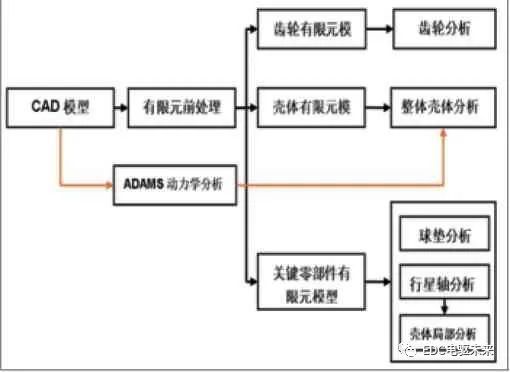
图3 差速器设计的技术思路
将差速器总成三维模型导入ADAMS中,设置材料属性、约束关系等参数,建立差速器运动仿真模型。
将输入载荷工况导入ADAMS运动仿真模型中,分析差速器齿轮啮合过程中的啮合力变化和差速器齿轮啮合激励频谱图,如图4所示。差速器齿轮啮合过程中的啮合力变化直接影响到齿轮接触应力和NVH性能,差速器总成失效和转弯异响与啮合力变化范围息息相关。
3. 齿轮制造工艺优化提升
对出现转弯异响、行星齿轮轴断裂和差速器壳体开裂等故障的减速器总成进行拆解分析,重点对差速器内直齿锥齿轮的相邻两齿跳动、齿圈轴向位移Δf AM、轴向最大间隙进行检测,检测数据见表3。
表3中的1#、2#、3#差速器齿轮均为故障件。从检测数据可看出齿轮精度较低,造成齿轮精度低的主要原因是锥齿轮的加工工艺落后,先采用刨、铣齿机加工铜极,然后采用电火花加工出锻造模具,由于经过三轮传递,导致精度下降;而采用高速铣削加工中心,直接在模具钢上进行雕刻加工,加工出锻造模具,没有经过误差的传递,齿轮精度较高,对改进加工工艺后的4#、5#、6#差速器齿轮相邻两齿跳动、齿圈轴向位移Δf AM、轴向最大间隙进行检测,检测数据见表3,从检测数据可以看出锥齿轮精度能提高了1~2级,齿轮接触区也有明显改善,装车测试后转弯异响消除,重新进行整车耐久试验后,行星齿轮轴未出现断裂,差速器壳体也未出现开裂。
表3 差速器齿轮检测数据
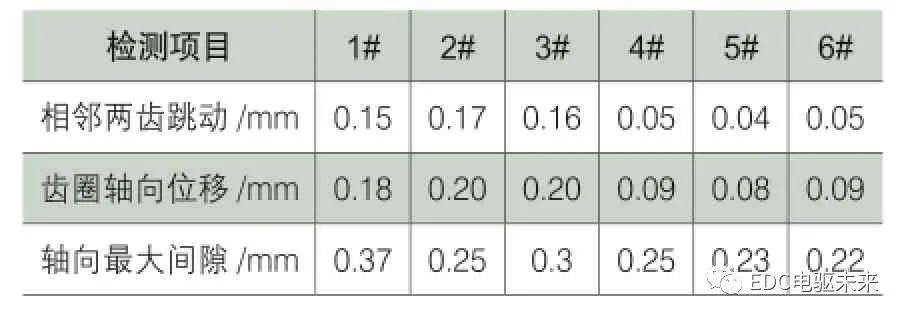
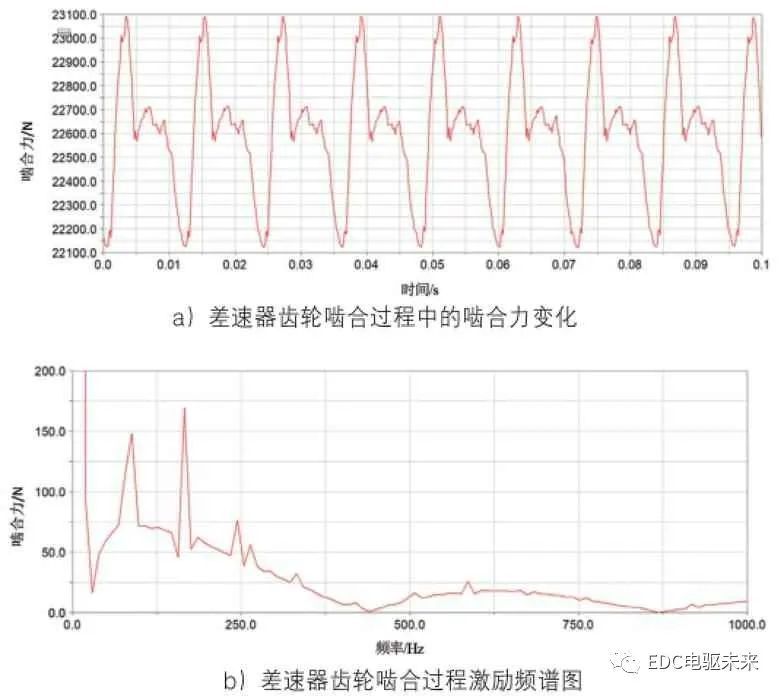
图4 差速器总成动力学仿真分析结果
4. 结论
通过对纯电动汽车在道路试验和售后故障模式的收集与分析,从传统燃油车和纯电动汽车动力外特性、连接方式、最大驱动转矩以及轮胎最大打滑转矩的差异性分析可以从机理解释这些故障现象产生的根本原因,并提出了如下提升纯电动汽车可靠性的解决方案:
(1)合理地采集实车路谱,经处理作为设计载荷谱是纯电动汽车减速器设计、仿真分析和台架试验等可靠性验证的前提,否则,以上结论对整车道路试验不具备参考价值,也规避了售后质量问题的发生。
(2)通过将合理载荷谱输入MASTA传动系统模型、ADAMS运动仿真模型中,可对减速器壳体、轴承和差速器等可靠性安全系数进行评估,可从设计层面大幅减低减速器壳体开裂、轴承散架等故障风险。
(3)通过系统优化设计可以优化差速器锥齿轮的接触应力分布,优化差速器锥齿轮制造工艺可以提高锥齿轮的精度,从而解决纯电动汽车转弯异响、差速器壳体开裂及行星齿轮轴断裂等故障。
来源:EDC电驱未来