随着节能减排及环保要求的提升,汽车轻量化的需求高涨。研究表明,汽车每减轻10%的质量,相当于提高8%~10%的燃油效率。铝合金板材具有质量轻、强度高、抗腐蚀性能好的特点,广泛用于汽车轻量化制造。铝的密度是2.7g/cm3,是钢铁密度的1/3左右,以铝板厚度为钢板厚度的1.44倍为例,减重效果可达到50%,车身质量对燃油消耗量的影响如图1所示。铝合金板材性价比效果明显(见表1),铝合金板材在汽车覆盖件方面的应用正在逐步扩大,是汽车轻量化的有效手段。目前,在宝马、奥迪等一些高端车型中,铝质发动机盖、翼子板以及门外板等已被大量采用。在最近的车型中,捷豹XJ、奥迪A8等几乎实现了全铝车身,车身单位面积上的平均质量由传统的100kg/m2以上大幅减少至65kg/m2左右。
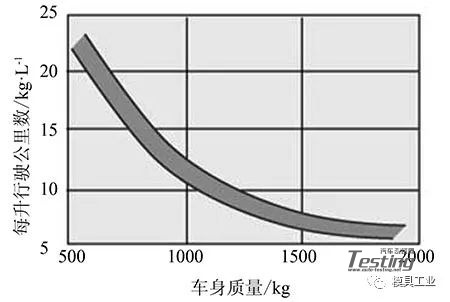
图1 车身质量对燃料效率的影响
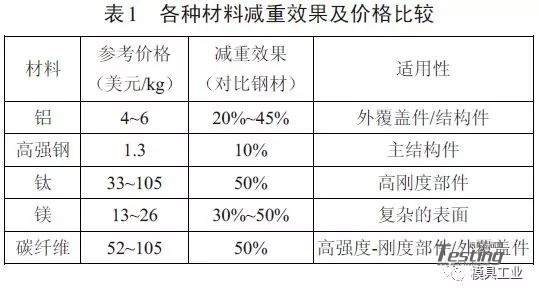
但铝合金板材在冲压性能方面存在一些弱点,在成形特性、成形工艺和生产条件要求等方面与传统的钢板冲压成形有较大差别。以下主要对铝合金板材的成形特性和冲压成形技术进行分析,并对铝合金板材在汽车覆盖件模具设计及量产应用的关键技术进行阐述。
汽车覆盖件用铝合金板材的种类与材料特性
纯铝材质偏软、强度低,为保持其优点,提高板材的成形性,得到较低的屈强比、较高的加工硬化速率、均匀的延伸率、加工硬化指数n和塑性应变比r值较高。通过Mg、Si等元素的加入,产生了各种系列的铝合金板,改善其力学性能和成形性。用在汽车覆盖件的铝合金主要为5000系(Al-Mg)和6000系(Al-Mg-Si)铝合金。
5000系铝合金板在强度、成形性、表面处理性和抗腐蚀性等方面具有普通碳钢板的优点,但有2个明显缺点:延迟屈服和吕德斯线(stretcher-strainmark)。板材成形时易出现桔皮效应,如图2所示,增加Mg含量可以一定程度上抑制吕德斯线的产生,但是随着Mg含量的增加,拉伸性能下降明显,加工硬化现象严重。因此在覆盖件中5000系铝合金板材多用于内板件,要求较高的外观件一般采用6000系铝合金板材成形。
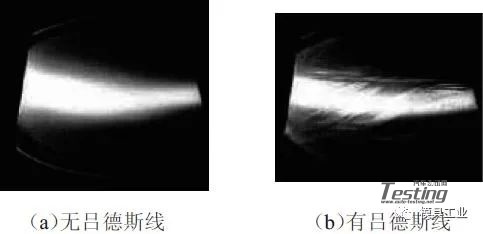
图2 5000系铝材成形后产生的吕德斯线
6000 系铝合金由于加入了Mg-Si 合金元素,强度和塑性良好结合,具有优良的综合性能。与钢板相比,6000系-T4态板材的屈服强度和抗拉强度相近,n值超过钢板。此外,6000系是烘烤强化合金,在冲压成形后,经油漆烘烤硬化(bakingharden,BH)后可达到强化目的,性能进一步提升。铝合金板材还可直接利用原有的生产线适当改造后进行加工。
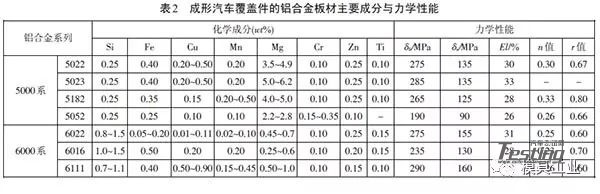
用于成形汽车覆盖件的铝合金板材主要成分和力学性能如表2所示。铝合金板材屈服强度δs和抗拉强度δb与低碳钢处于同等水平,但延展性不如低碳钢。铝材和钢材应力-应变曲线如图3所示,铝合金板材在最大应力后的拉伸(局部拉伸)明显比低碳钢差,这是成形性差异的主要原因。
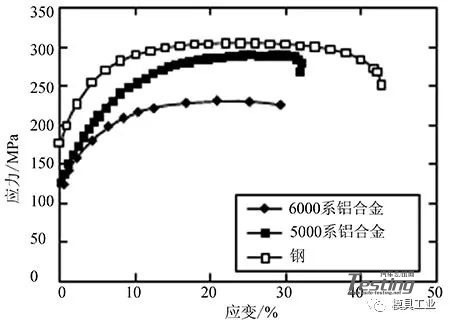
图3 铝合金与钢的应力-应变曲线
汽车覆盖件用铝板的成形性能分析
延展性与深拉深性
延展性是指材料在未开裂的前提下在线性方向上的长度变化。由表2可见,铝合金板与强度接近的钢板对比,软钢汽车板由于具有较高的n值 (0.20~0.28)、高的r值(1.3 以上),总延伸率大于40%,具有良好的延展性和深拉深性;而铝合金的r值通常在0.6~0.8,总延伸率只有25%左右,铝合金板材的深拉深性能比钢板低约30%,如表3所示。
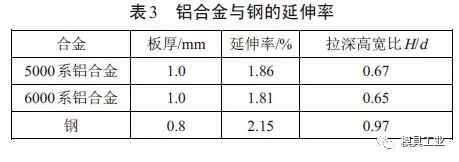
屈服强度与回弹
铝材的杨氏弹性模量E为钢板的1/3,故变形中弹性应变占比大,回弹比钢板要大3倍左右。铝板要尽量避免二次成形或整形,回弹的整改一般在拉深过程中实施。根据这一特点,在设计铝合金冲模时必须充分考虑。根据长度回弹计算公式及弯曲回弹公式:
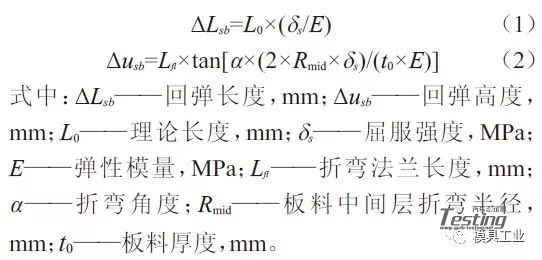
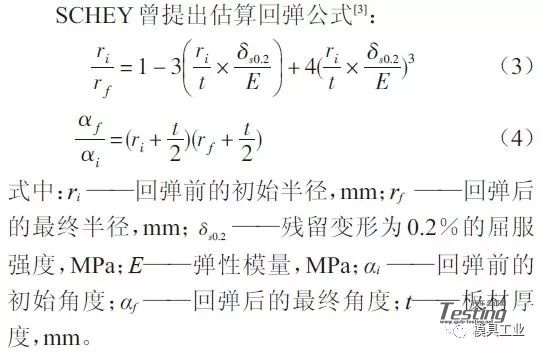
根据公式(3)、(4)可知,回弹大小与屈服强度、板料厚度有关,如果使δs0.2/E增加,或者使ri/t值增加,都会导致回弹量增大,而屈服强度δs0.2的影响在所有因子中是最大的。而在材质和厚度t均相同的情况下,弯曲半径增加,则回弹量也会增大。
弯曲及翻边性能分析
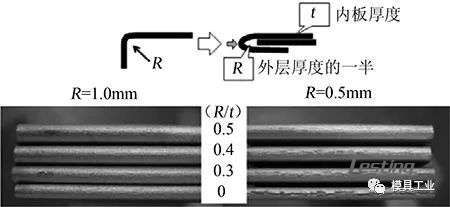
图4 90°弯曲试验对比
铝合金板材翻边、弯曲加工性能比钢板差,加工条件差异大会导致板材弯曲部位褶皱及开裂。以90°弯曲作为试验条件,得出结果如图4所示。当90°翻边弯曲半径R为1mm时,翻边后没有出现不良情况;但90°弯曲半径R为0.5mm时,当翻边圆角R与内板厚度t的比值在0.4以下时,表层开裂。试验表明弯曲半径对弯曲有明显影响。在产品设计时应将弯曲翻边圆角尽量放大。在不同翻边弯曲半径下,弯曲及翻边减薄率对比的情况如图5所示。
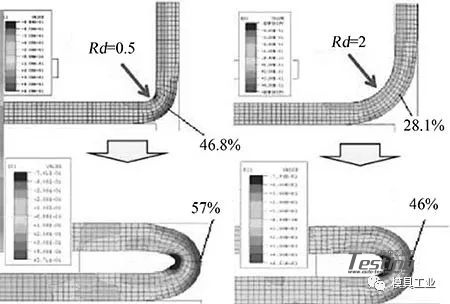
图5 弯曲及翻边减薄率对比
时效硬化
铝合金热处理后可得到过饱和的铝基固溶体,这种过饱和铝基固溶体在室温或加热到某一温度时,其强度和硬度随时间的延长而增大,但塑性降低,这一过程称时效。时效过程中使铝合金的强度、硬度增大的现象称之为时效强化或时效硬化。
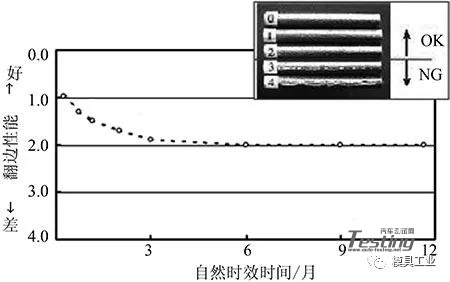
图6 汽车铝合金板时效周期推移
5000系列的材料时效变化很小,可认为无时效硬化现象,但6000系列材料进行热处理后,有时效硬化,时效硬化周期如图6所示。以6000系列的铝材为例,新置材料的屈服强度为130MPa,存放3个月后的屈服强度为150MPa,存放6个月后的屈服强度为165MPa,如果存放时间超过6个月,6000系铝材将发生过硬导致成形困难。
汽车覆盖件用铝合金板材冲压品质控制方法
铝材薄板成形时常见品质问题与控制方法
(1)开裂:铝板延伸率比钢板小,故允许变形量比钢板小,极易开裂,建议设置成形圆角和脱模角度时要比钢板成形适当放宽。
(2)起皱:铝板塑性较差,在冲压成形时容易起皱,对于深拉深件,在侧壁尽可能增加吸皱凸包,有利于解决起皱问题。
(3)板料时效:5000系材料由于无后序热处理工艺,时效性比6000系材料好,但一般建议时效控制在9个月内。
(4)表面划伤:由于铝板材质软,对模具零件表面的粗糙度要求高,模具成形零件表面时建议实施镀铬处理,表面检查时尽量避免使用硬油石打磨,可采用胶木软油石代替打磨模具成形零件表面以减少划伤。铝板成形模镀铬比钢板成形模要求更高,平面镀铬厚度控制在7~15μm,R部位保证在20μm以上。
铝材薄板的成形回弹精度控制
回弹是冲压成形零件的重要问题之一,尤其对于铝合金板冲压成形,对回弹的控制除了现有模拟分析手段外,采用调试与设计的充分联动,通过设计指导模具调试是改善成形回弹、提升零件精度的重要手段。
(1)铝合金板回弹比钢板要大3倍左右,建议主要在拉深工序上控制回弹,尽量避免整形等二次成形。
(2)调试与设计充分联动,铝材模具调试周期比一般钢板模具周期长,出现回弹较大的情况时,通过设计回弹补偿实施模具型面的再加工、研配,以达到改善目的。
(3)铝板模具的型面着色率达到90%以上,调试冲次数增加到一般钢板模具的3倍左右,以充分达到稳定成形的状态。
减少铝材薄板切屑控制表面缺陷
铝合金板由于质量较轻、材质较软,在切边工序及翻边工序易产生碎屑落到零件表面导致压伤,造成表面质量缺陷。针对切屑一方面可通过工艺改善减少碎屑的产生;另一方面可通过辅助工装实现碎屑的及时清理。
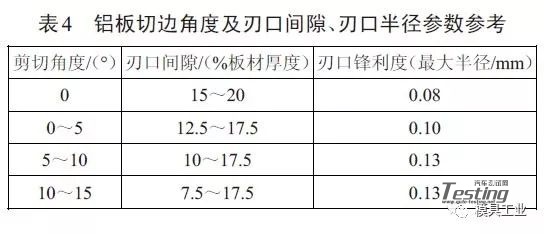
(1)在工艺上,修边冲孔角度尽可能小,如果需在斜面上进行修边剪切时,表4所示的铝板切边角度及刃口间隙、刃口半径参数可供参考。图7展示了一种减少碎屑产生的切边刀口的改善方案,经试验碎屑发生率可降低70%,但刃口的耐用性有待进一步验证。
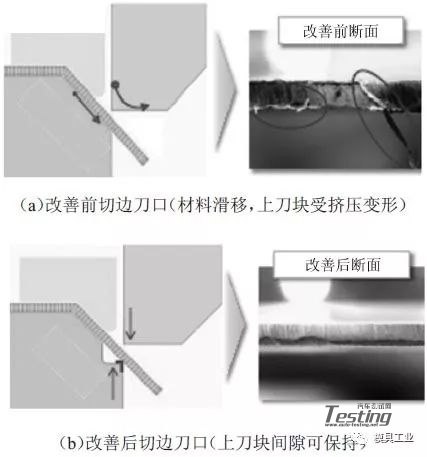
图7 改善切边刀口示意图
(2)在模具中增加吹屑装置或负压装置,可在成形间隙时间将残留在模具内的碎屑迅速排出。
铝合金板材模具设计要点及量产应用注意事项
虽然铝合金板材可在现有钢板冲压设备及生产线上实现冲压成形,但由于铝合金板材密度小,成形特性与钢板有较大差异,在铝合金板材的冲模设计及量产应用上需针对铝材的特性进行改进。
铝合金板材模具设计要点
由于拉深模的上模易吸件,修边、冲孔模的上模也易带起板件,而下模易发生堵料的现象,废料滑出也比钢板困难。在模具结构设计时需要注意以下几个方面:
(1)对于吸件的问题可在上模非成形部位加弹顶销,也可在不造成外观质量问题的前提下,在上模的凹R角区域、非外观面及避空区域增加或增大排气孔。
(2)采用带顶针结构的凸模。
(3)修边工艺优先考虑分工序二次修边,修边间隙建议为钢板修边模具修边间隙的1/2,修边刀块间的间隙控制在0.05mm以内。
(4)翻边工艺不能有型面干涉,翻边间隙建议为1~1.1(t板厚)。
(5)尽量增大废料滑出角度,滑出角度不小于30°。
铝合金板材冲压量产应用注意事项
(1)对于板件分张问题,由于铝合金板不具有磁性,一般采用气压分张技术为主,机械分张进行辅助,通常可达到15SPM以上,在自动化送料过程中采用真空吸盘吸附的形式进行板件搬送。机械辅助分张工装示意图如图8所示。

图8 机械辅助分张示意图
(2)铝合金板材的返修管理:由于铝合金板材易产生碎屑,零件表面外观小瑕疵较多,返修量较大,尤其是铝合金返修产生的铝粉积聚后遇火易爆炸。铝合金板材需要配建专用的铝材返修房进行返修工作,在返修的同时同步收集铝粉。
(3)铝合金零件的包边:汽车的4门和前后盖零件冲压成形后还需进行内外板的弯曲包边结合。由于存在时效硬化,如果零件放置时间过长则会导致弯曲包边时开裂,在零件冲压后需在时效硬化前完成弯曲包边工序。
来源:模具工业
作者:吴琼兴