CAE技术分析贯穿了汽车开发的全过程,小到螺栓预紧力分析,大到整车碰撞模拟和整车NVH(噪声、振动和声振粗糙度)分析,CAE分析都发挥了无可替代的优势和作用。CAE技术分析范围覆盖了结构、流体力学、多体动力学、被动安全、工艺、整机合整车性能等方方面面。新能源汽车研发中的CAE仿真技术应用既具有延续性也有其独特性。
今天小编就详细和大家讲讲CAE技术在新能源汽车研发中的应用
结构强度、刚度和模态分析及结构优化设计
汽车结构有限元分析的应用体现于:
一是在汽车设计中对所有的结构件、主要机械零部件的刚度、强度和稳定性进行分析;
二是在汽车的计算机辅助设计和优化设计中,用有限元法作为结构分析的工具;
三是在汽车结构分析中普遍采用有限元法来进行各构件的模态分析,同时在计算机屏幕上直观形象地再现各构件的振动模态,进一步计算出各构件的动态响应,较真实地描绘出动态过程,为结构的动态设计了提供方便。
噪声、振动与不平顺性(NVH)分析
有限元法除了广泛应用于汽车结构分析外,还可应用于车身内的声学设计,通过车身内声模态与整机模态的耦合,评价乘员感受的噪声,并进行噪声控制。
疲劳寿命与可靠性分析
汽车产品设计已进入有限寿命设计阶段,要求汽车在设计的使用期内整车和零部件完好,不产生疲劳破坏; 而达到使用期后,零部件尽可能多地达到损伤。以求产品轻量化,节约材料和节省能源。
碰撞与安全性分析
汽车模拟碰撞分析的目的就是为了提高汽车被动安全性能。对于汽车被动安全性能的要求,一是在碰撞时,车身结构、驾驶系统、座位等能吸收较高能量,缓和冲击; 二是发生事故时,确保车内乘员生存空间、安全气囊、座椅安全带等对乘员的保护功能,以保证乘员安全并在碰撞后容易进行车外救助和脱险。
气动或流场分析
随着计算机技术的飞速发展, 应用计算流体力学(CFD)方法来预测汽车车身外部流场已成为可能。CFD 在汽车领域中的绝大部分应用都集中于进行汽车外流场的数值模拟。在内燃机的设计和开发中,CFD 已经被作为一种重要而有效的工具加以利用。
汽车的可操纵性分析
车辆的可操纵性分析是指利用整车多体动力学模型,在驾驶人员采用不同驾驶方法的情况下,对车辆的侧倾稳定性进行仿真研究,还可以预测车辆在各种极限条件下的性能。
整车性能的分析评价与预测
从整体的角度对汽车的各种性能进行分析和预测,包括汽车的空气动力学特性、声学特性、振动特性、操纵稳定性、乘坐舒适性、碰撞安全性等。
电池组仿真分析
新能源汽车及其他设备所使用的电池主要分为化学电池、物理电池以及生物电池三大类,由于技术限制现阶段物理电池和生物电池并不能广泛使用,所以目前新能源汽车主要用的是铅酸蓄电池、镍氢电池及锂离子电池等。就像内燃机车对发动机有各种要求,新能源汽车对电池组也有着苛刻的性能要求,包括安全性、稳定性、成本、充放电效率、比功率、比能量等,这些直接关系到新能源车在电动驱动上的表现。
电池组热管理:根据温度场分布设计散热系统
电池的机械性能分析:碰撞,碾压,针刺对电池的影响
电池的电性能分析:过充/过放,大电流,充/放,外部短路对电池的影响
噪声、振动和声振粗糙度分析:流动噪声,结构振动
结构的耐久性分析
电动机仿真分析
主要为以下几个方面:
电磁设计优化:计算转矩曲线,优化电磁参数
热分析:设计散热系统,防止热损耗
振动分析:降低电机噪声
系统集成:优化电动机及控制器
结构耐久性分析
在新能源汽车牵引电动机的研发中,设计者要重点考虑电动机的电磁问题。首先根据最初的三维图纸及装配体的相关工程设计指标,在电子设计软件中定义电动机的主要设计参数,包括永磁材料、绕组分布图、绕组匝数等,此外还要计算出电动机的电气特性。然后将这些输出的模型和设计数据输入到电磁仿真软件中,模拟电动机的三维电磁场,计算出电动机的转矩曲线。
电动机的转矩曲线可以反映出:在电动模式驱动车辆时转矩如何随时间上升;在停车制动模式时电气阻力矩如何随时间变化。电动机电磁性能分析时,还需要引入车辆的质量以确定各种情况下的加速时间及制动时间。基于这些输出结果,设计者可以改变某些设计参数如永磁体的尺寸来调整设计,通过参数优化设计,在电动机的性能与电动机的尺寸、重量、成本之间做出最优匹配,优选设计方案。
电磁仿真输出的转矩可进一步输入到结构力学软件中,用于分析电气传动系统中其它部件包括驱动轴、齿轮等的应力、载荷、变形及振动。以电动机为主的驱动系统是新能源汽车的主要噪声源,为了进行噪声优化,驱动系统的振动分析也非常重要。此外,流体动力学可用于研究电动机的热管理问题,以确定电动机周围的热分布,优化热损耗问题。
在进行电动机仿真分析的时候,要同时兼顾电磁和机械分析的多物理场,还要考虑两者之间的耦合,在不同载荷情况的性能计算和不同设计方案比较时,要协调多个工具的动作,在不同工具之间交换数据。这要求仿真工具具有多物理场联合仿真的能力,能够在一个统一的环境中实现针对机电系统不同部件、不同学科之间的耦合仿真。
电力电子器件仿真分析
在对新能源汽车电力电子器件进行热分析的时候,工程师需要先通过电子电路仿真软件建立电力电子器件系统仿真分析模型,通常包括控制算法器件模型、电动机器件模型、各器件模型的电力特性(如通断电压、电流波形等),以及器件模型之间的控制算法逻辑。通过电子电路仿真分析软件确定出车辆在加速、巡航和制动等过程中任意给定时刻、整个系统内电流的变化情况。
控制逻辑优化:在不同驱动工况下,优化电气传动动力集成部件及系统
热管理:电磁损耗散热方式和路径设计
热应力分析:优化由热应力和电磁力产生的机械形变问题
利用电子热流分析工具,工程师可以指定电气传动系统中主要热源(电子控制器件和电机的载流部件)的几何尺寸,通过单独添加系统中关键点上的每个热源,同时还考虑空气流通量和传导热量的影响,以及参数化分析,可处理数据并生成等效热模型,用于热分析。利用这些热模型可确定电力电子器件整体温度分布以及温升性能参数,例如:从电池获得多少电能才能保证温度不超过影响某电子器件性能的限定值。
根据温度分布,工程师可以利用有限元软件的热-结构耦合分析功能,确定由此产生的热应力。电子设计分析工具还可用于计算电动机各部分上的电磁力,从而确定形变量和机械应力分布。由此,工程师可以通过修改结构,消除应力集中和过度变形,或者反之,减少那些由于过度设计而额外使用多余材料的区域。
电磁兼容仿真分析
与传统汽车研发不同,在新能源汽车设计中需要重点考虑大量机电器件的电磁兼容性(EMC),避免出现电磁干扰。主要存在两类电磁干扰问题:通过载流结构传导的电磁场引起的能量反射波对其它相连部件形成潜在威胁;通过空气辐射的电磁场影响其它电子系统。这两类电磁干扰问题都必须被充分考虑,工程师必须对车辆关键器件进行电磁兼容分析。
在样机制造之前进行电磁兼容分析
减少电磁兼容的测试
电机、母排、控制器等部件的电磁兼容分析
为了精确分析器件的电磁兼容性能,工程师首先要建立电路模型。供应商提供的数据手册中有器件性能曲线和数据,从中提取出需要的参数来生成器件的半导体电路模型。为了进行传导干扰分析,工程师需要将功率变换器的设计版图从CAD软件直接导入到寄生参数提取软件中,从而计算导电通路的频变电阻、部分电感和电容,并生成等效电路模型以备系统仿真使用。系统仿真的结果可用于检验辐射水平,工程师通过计算空间任意点上的电磁场强度以判断是否符合国内外相关标准。如果辐射超标,电磁干扰和电磁兼容可溯源到器件设计版图上的问题源。
由此,对设计做出参数更改,并获得一系列仿真结果,直到传导辐射和辐射电磁发射等级都在可接受的限值之内。这样就能在样机制造之前保证新能源汽车部件间的电磁兼容性符合要求,避免出现电磁干扰问题,也取代了成本较高的电磁兼容测试。
多物理场的系统集成仿真分析
在新能源汽车研发设计中,除了要解决电池组、电动机、电力电子等部件的问题之外,系统集成也是一个完整可靠的电气传动系统中至关重要的部分,必须考虑每个部件独有的特征、属性、强度和其它复杂因素等,以确保整个电气传动系统在宽负载范围内及各种行驶条件下都能获得最高的整体效率。
由于子系统和部件协同工作,紧密耦合,它们的开发也不能完全独立地进行,而且每个子系统性能的改变都必须与其它所有子系统相匹配。同时整个系统涉及机械、流体动力学、热学、电气和电磁等领域的研究,因此为了成功地仿真如此复杂的电气传动系统,仿真方案必须建立在一个可实现多物理场、无缝集成的设计平台上,来平衡复杂的、相互依赖的、或相互矛盾的机械、电气、电磁、流体和热管理等多种设计需求。
电池组热分析
电池组热分析通常重点考虑电池包风道的不同布置,对电池包散热系统的影响。同侧风道方案是指电池模组顺序排列配置在电池箱体内,外部进入的冷却气流从电池包一侧进入,通过内部风道进入电池模组之间的缝隙,最后在与进风道同侧位置的出风道处将气体排出。异侧风道方案是指电池模组顺序排列配置在电池箱体内,外部进入的冷却气流从电池包一侧,通过内部风道进入电池模组之间的缝隙,最后在与进风道相反方向位置的出风道处将气体排出。
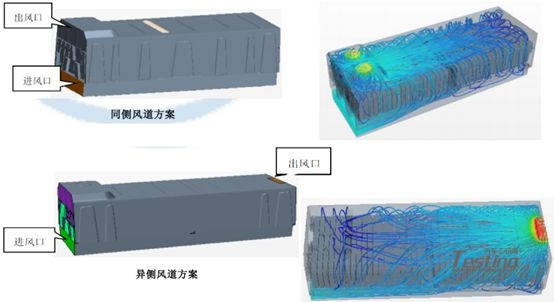
同侧进出风道方案,空气从进气管进入到电池组底部,到达右方后回流至左侧,这种回流现象将导致热循环,不利于电池上下部散热。相对于同侧进出风道方案,异侧进出风道方案气流从左侧进口进入到电池组底部,直接到达右方,能够减小电池热循环程度,有利于降低电池上部的最高温度;异侧进出风道底部流场流速分布更加均匀。
结合1D FloMaster和3D FloEFD可以对电动汽车电池组热管理复杂系统开展设计分析。在部件级层次,FloEFD用于研究分析热管理系统详细的流动和换热行为,确保电池组工作性能可靠。识别任何不可接受的设计,如不合理的流动布置或极端的温度梯度。在系统层次,结合Flowmaster模拟整个电池冷却系统,分析部件的相互影响,确保正确的系统性能。在早期CAD设计过程中同步使用FloEFD仿真,相比传统CFD工具,模拟时间可以大大减少。进一步结合使用Flowmaster,系统工程师可以在有限的开发时间内获得最佳设计效率。
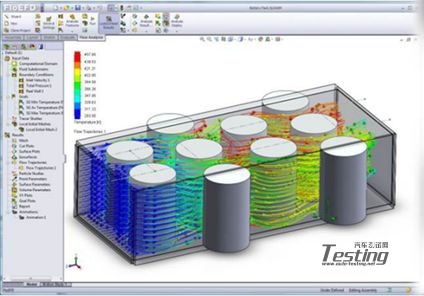
IGBT模组热分析
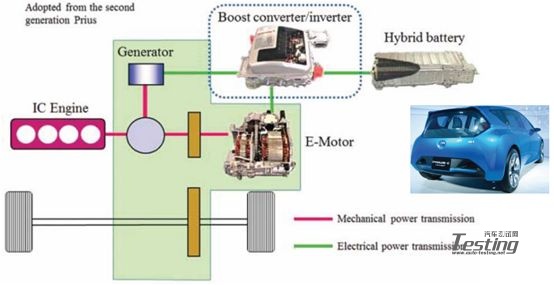
IGBT可以在上百安培的电流下运行并扮演极高开关速率的电子开关的角色。因此它也会产生大量的热量。利用FloEFD和T3Ster热测试仪进行功率模块的热特性优化。FloEFD用于设计前的热分析与评估。T3Ster使工程师可以了解散热路径的内部信息,结构函数清晰的给出了每一部分的热阻,并且在耐久性测试之前和之后都可以进行测试来比较散热的特性。
来源:海基科技