摘要:文章主要介绍低密度聚丙烯(PP)材料开发的思路、原理、材料性能测试、零件注塑和零件性能评价。为内饰塑料件轻量化提供一种低成本、低风险的可行方案。
在汽车轻量化和节能的压力下,各OEM纷纷采用碳纤维复合材料、轻质铝合金、高强度钢、薄壁化设计等措施进行减重。虽然这些技术可以实现大幅度的减重,但这些措施轻则更改模具,重则更改生产工艺,投入成本太高、验证周期长、风险较高,在国内OEM推广存在困难。
目前中低端汽车门板内饰板、侧围饰板、立柱饰板材料大多采用PP类材料,全车内饰用量约50kg。开发低密度的PP类材料可以无需更改模具和注塑设备,调整注塑工艺即可得到尺寸和性能满足要求的零件,实现轻量化。集团种子基金支持主要用于PP、POE、添加剂和填料等材料购买、加工费和测试费。
1 材料开发
1.1 材料开发思路
目前中低端汽车门板内饰板、侧围饰板、立柱饰板、座椅饰板、副仪表板材料大多采PP+EPDM-T20,整车内饰用量约50kg。PP+EPDM-T20是以PP(聚丙烯)为基材添加约10%的EPDM(三元乙丙橡胶)作为增韧相,添加20%的滑石粉改善材料的强度、刚度和尺寸稳定性。PP密度0.92g/cm3,EPDM密度0.87 g/cm3,滑石粉密度2.7-2.8g/cm3。在保持材料性质不变同时降低滑石粉的使用量可以降低材料的密度,实现轻量化。
1.2 材料开发原理
主体基材聚丙烯是主链为亚甲基和次甲基交替、侧链为甲基的线性聚合物,其分子极性小,易结晶,低密度和化学惰性等性能。纯的聚丙烯由于存在机械强度较低、耐热性差、收缩变形大等缺陷,不能满足车内饰塑料件要求(见表1)。随着结晶度的提高,PP材料的拉伸强度、弯曲模量、硬度都有明显提高。
EPDM是乙烯-丙烯-非共轭二烯烃共聚的三元橡胶通常作为增韧材料使用,但由于碎胶困难,后期与粒状PP混合不均匀,流动性较差,造成整体性能下降,同时由于EPDM气味较大,作为增韧材料使用量逐渐减少。POE是采用茂金属催化剂的乙烯和辛烯实现原位聚合的热塑性弹性体,在POE分子链中辛烯的柔软链卷曲结构和结晶的乙烯链作为物理交联点,使它既有优异的韧性又有良好的加工性;POE分子量分布窄,具有较好的流动性,与聚烯烃相容性好,相对于常用EPDM增韧效果更好。
为改善纯聚丙烯材料的缺陷,通常采用价格便宜的无机硅酸盐滑石粉进行填充改性。试验证明,随着滑石粉量的增加,材料弯曲模量显著提高,收缩率降低,热变形温度提高(见图1)。
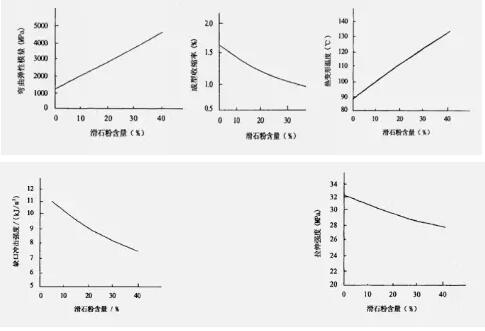
图1 滑石粉对聚丙烯材料性能影响
但随着滑石粉含量的增加,材料的冲击强度和拉伸强度逐渐下降。主要原因是随着滑石粉含量增加,滑石粉微粒相互团聚,与聚丙烯基材结合力下降,出现了不同程度的相分离,增强效果减弱。
表1 材料基本配方
成分
|
比例
|
高结晶聚丙烯PP
|
71%
|
增韧材料POE
|
18.4%
|
亚纳米滑石粉
|
10%
|
热稳定剂
|
0.3%
|
光稳定剂
|
0.2%
|
耐刮痕剂
|
0.1%
|
因此选用高结晶PP基材,选用增韧效果更好的POE提高增韧效果,特殊偶联剂改善滑石粉表面性质,提高滑石粉和PP基材的结合力。通过以上措施可以在保持材料的力学、热学性能的基础上降低滑石粉的含量,从而降低材料密度实现轻量化。基本配方见表1。
来源:代玉堂,杨汐 汽车实用技术杂志社
评论 0
同类信息
汽车用高分子材料测试哪些?
作为整车生产的基础,汽车材料的质量是整车生产成功与否的先决条件。随着各种新车型日益完善的功能和人们对乘车感受的不断追求,要求汽车生产企业必须在源头上对
2021-02-0669984
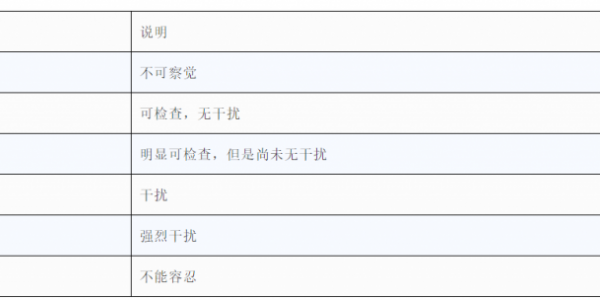
- 汽车气味评价方法
2020-03-14
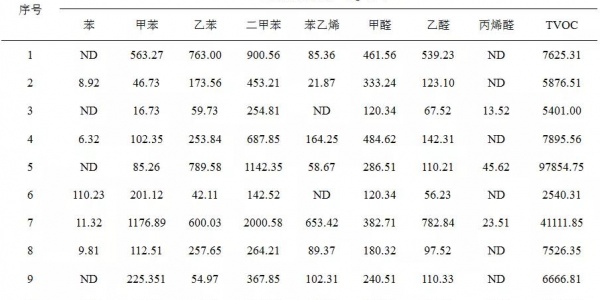
- 儿童座椅挥发性有机物现状分析及建议
2020-03-14
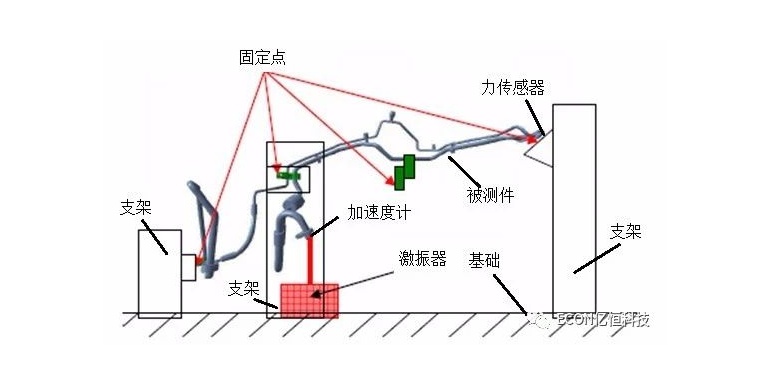
- 汽车空调管路动刚度与耐振性试验系统
2019-07-20
汽车管路的性能测试介绍
我们先来大致捋一下车辆各大系统的管路:1.进气系统管道:空压机进气管、中冷器管等2.燃油系统管道:供回油管、碳罐油管3.转向系统管道 :高压油管、吸油管、回
2019-07-1713950
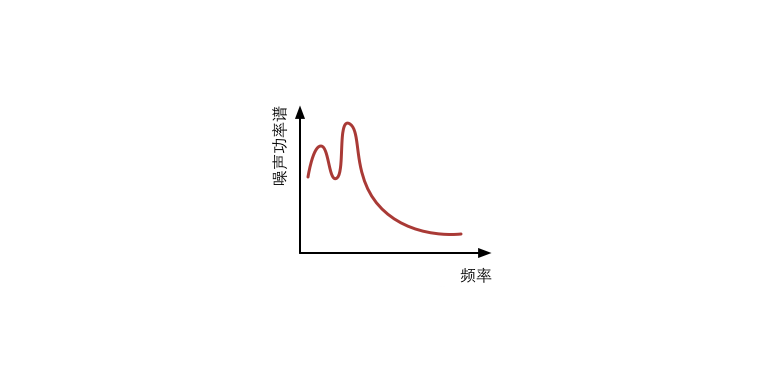
- 如何实现材料声特性的设计及数据管理
2019-07-10
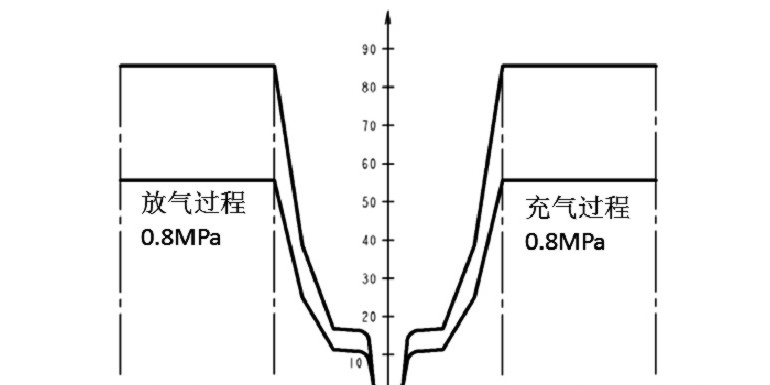
- 空气悬架高度阀对卡车驾驶室舒适性影响的 试验研究
2019-06-19
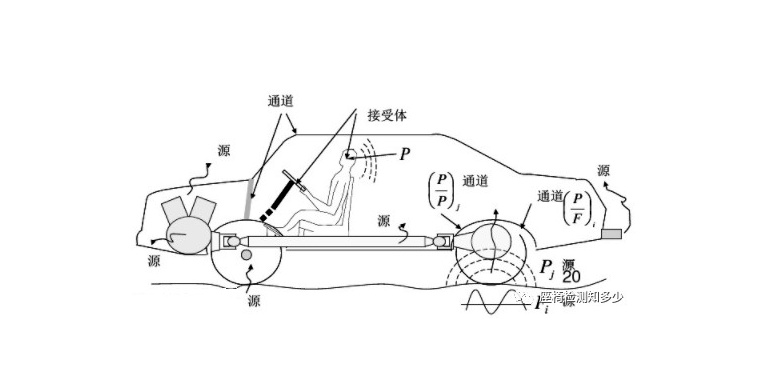
- 阻尼对汽车座椅减振特性的作用和影响
2019-06-17
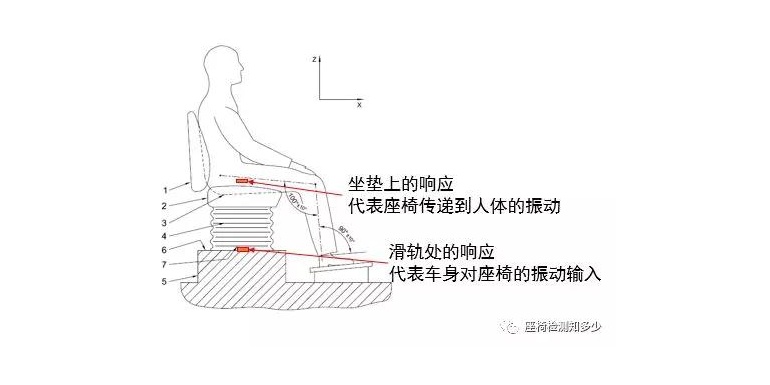
- 激励信号对人-椅系统传递特性的影响
2019-06-10
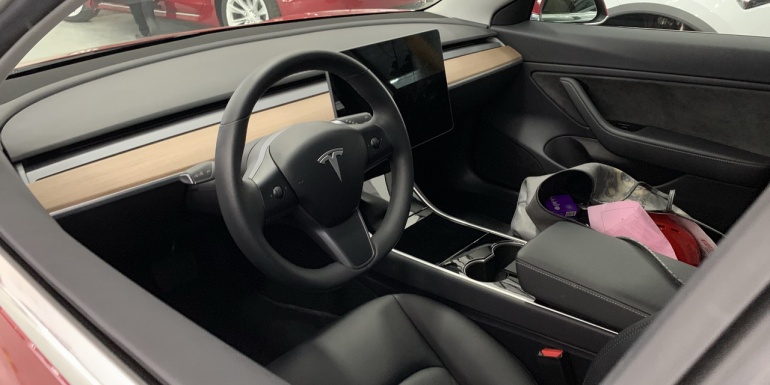
- Model 3 VOC测试
2019-06-10