1 整车问题简介
研究对象为后驱车型,传动系统由发动机、变速箱、三段式传动轴和后桥组成。图1为3档全油门加速工况车内噪声时频分析色谱图。从图1中可以看出,在频率240.0 Hz处存在明显共振带,且有多个阶次在不同转速激起了该模态共振。图2为3档全油门加速工况车内噪声总声压级和阶次曲线。从图2中可以看出,在发动机转速大于1 800 r/min时,该共振带成为车内噪声的主要来源,发动机0.5倍数阶激励激起该模态共振产生多个轰鸣噪声,且幅值高达81 dB(A)。该车在1~6档和空档均不同程度的存在该模态共振引起的问题。
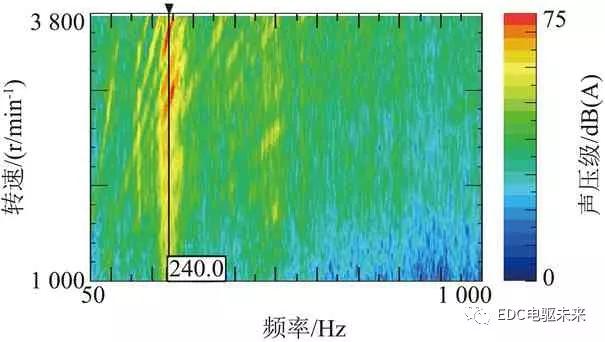
图1 车内噪声色谱图
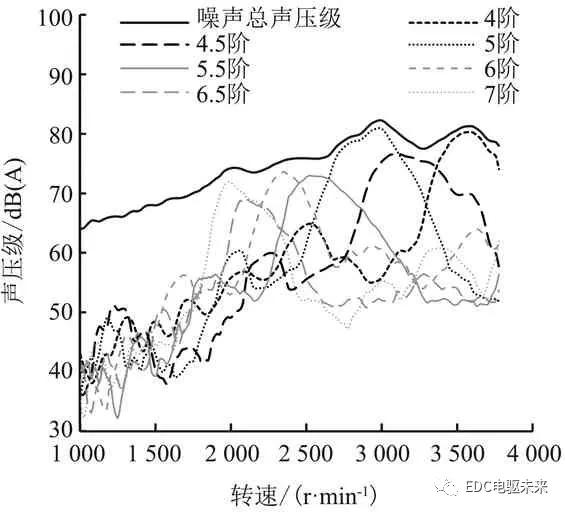
图2 车内噪声总声压级和阶次曲线
2 传动系统弯曲模态试验及影响因素分析
2.1 测点布置和激励位置
测试车型为某后驱车型,动力传动系统包括发动机、变速箱、三段式传动轴和后桥。由于与该车在频率240.0 Hz共振问题特征相吻合的底盘测点为后桥输入点壳体,因此本模态试验包含的零部件为三段式传动轴和后桥。三段传动轴各均匀分布3个测点。后桥左右轴管部分各均匀分布3个测点,测点布置在均匀分布的同时,还应考虑在后桥悬架连接点等后桥约束边界位置尽可能布置测点。后桥桥包部分布置3个测点,分别位于后桥输入点壳体、桥包后盖上和桥包后盖下各1个,形成1个能够更好表达点头模态的三角形。除此以外,在变速箱壳体布置1个点,用于辅助判断完整模态振型是否包含未测试的动力总成。后桥模态测试模型如图3所示。
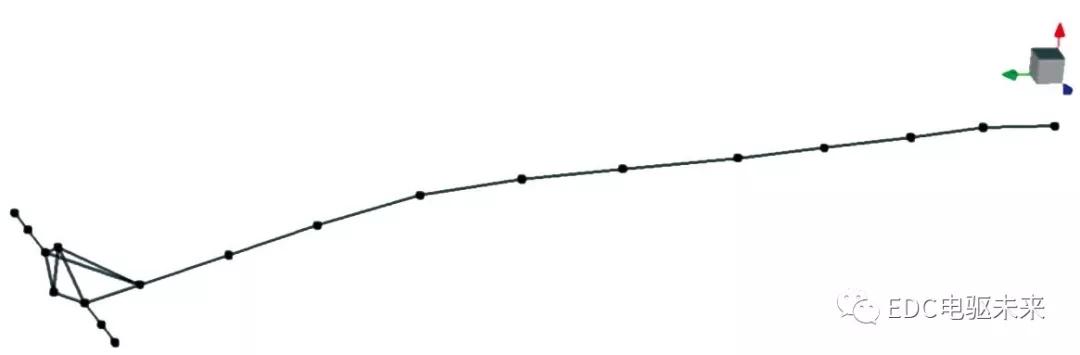
图3 后传动轴花键和后桥测点
模态激振器主要布置于后桥输入壳体和变速箱输出壳体位置。其中,后桥输入壳体处激振器需在X、Y和Z三个方向均有分力,以保证能激起后桥X向和Z向弯曲及点头等模态。变速箱输出壳体处激振器则主要保证Y向和Z向有足够激励,以便充分激励传动轴和动力总成弯曲模态。激振器布置如图4所示。
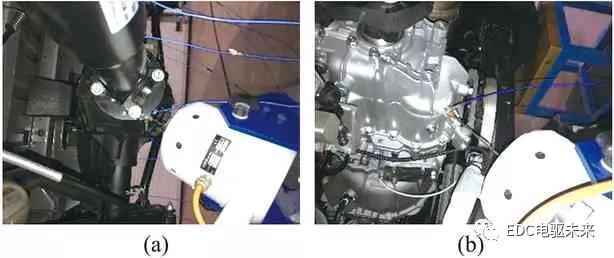
图4 后桥输入壳体和变速箱输出壳体激振器
2.2 传动系统弯曲模态试验影响因素分析
影响传动系统弯曲模态试验结果的因素较多,主要包括两个方面:模态试验与实车运行工况下系统状态存在差异,如轴系承受的扭矩、轴系间隙和变速箱档位等;模态试验参数影响,如激振力大小、方向和位置。
模态试验中,车辆状态应尽可能模拟实车运行状态。在传动系统弯曲模态试验前,将首先对传动系统间隙和档位等影响因素进行研究。
将变速器挂入固定档位(3档),先将车辆举起,在落地的过程中,在人力推动驱动轮的同时将车辆放至地面,以消除传动系统间隙。该方法的缺点是轴系承受的扭矩与实车状态不同,但操作方便安全,如需模拟实车扭矩可参考文献[1]中方法。图5所示为相同的激励情况下,消除传动系统间隙和不消除传动系统间隙时,传动系统测点传递函数总和曲线。从图5中可以看出,总体来说传递函数曲线峰值特征和大小差异不大,但部分峰值频率存在3.0~5.0 Hz的差异。峰值频率的差异主要是由于传动系统间隙带来的非线性和约束边界差异所致。由结果可知,如果不消除传动系统间隙将会对模态识别结果造成一定误差。
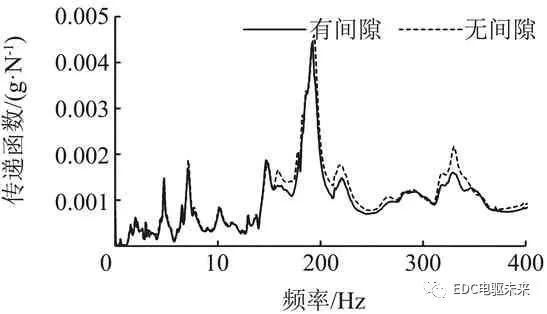
图5 有无传动系间隙时传动系统测点传递函数总和曲线
消除传动系统间隙,保持激励大小和方向不变,将变速器挂入不同档位,激励得到传动系统测点传递函数总和曲线,如图6所示。从图6中可以看出,不同档位传递函数曲线峰值频率存在差异,如190.0 Hz左右峰值频率差异可达4.0 Hz。部分峰值频率在不同档位甚至可能会消失,该现象应该是由于该模态在部分档位变得不敏感,或者敏感的激励位置发生了明显变化。因此,如果想要得到预期的模态频率只在实车部分档位出现问题后,确保模态试验时保持跟实车出现问题的档位相同。
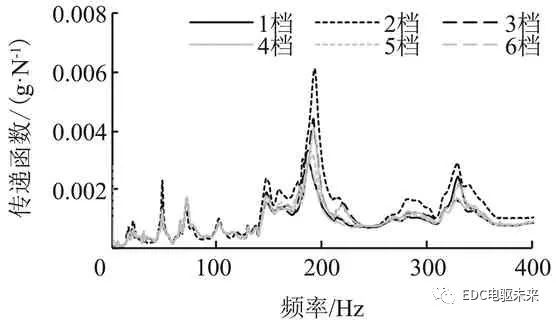
图6 不同档位时传动系统测点传递函数总和曲线
2.3 传动系统弯曲模态识别结果分析
将变速器挂入3档,消除传动系统间隙后,后桥输入壳体处激振器调至Y向,激励得到传动系统测点传递函数总和曲线,如图7所示。用最小二乘复频域法对模态频率和振型进行识别,传递函数曲线三个峰值对应的模态频率分别为24.5 Hz、161.0 Hz和240.0 Hz,模态振型分别如图8、图9和图10所示。该车型传动系统对后桥输入端Y向激励较为敏感的模态分别是传动轴总成的横向一阶弯曲、三阶弯曲和四阶弯曲模态。该激励方式未能识别出二阶弯曲模态,原因可能为二阶弯曲模态对于该激励方式不敏感,可尝试不同的激励位置,直至找到相应振型。但四阶弯曲模态频率240.0 Hz与所需要解决的车内噪声问题频率吻合较好,与二阶弯曲模态无关。因此,二阶弯曲模态未继续尝试不同的激励方式。
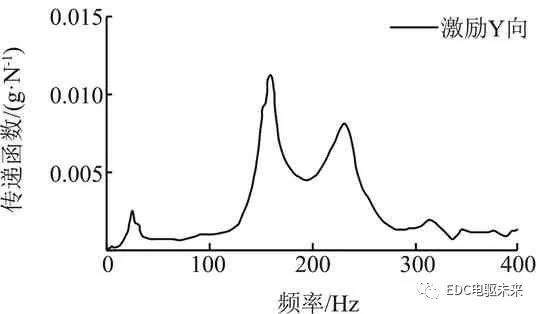
图7 激励Y向时传动系统测点传递函数总和曲线
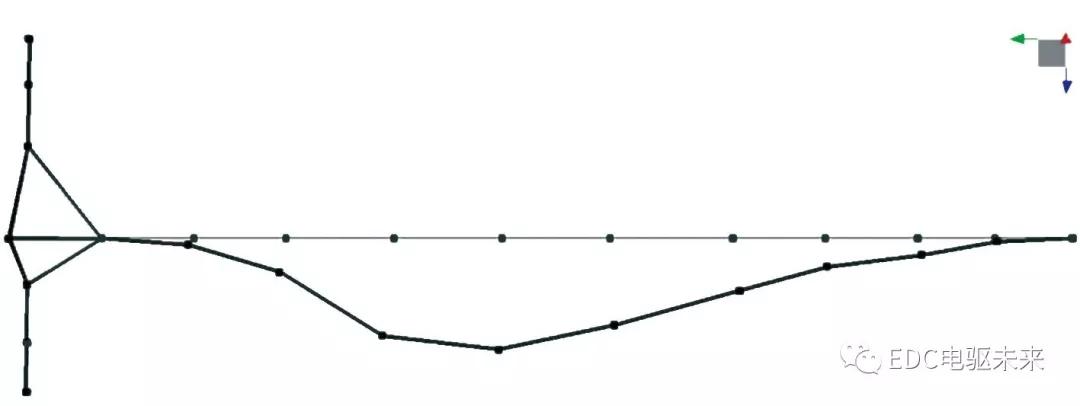
图8 24.5 Hz横向一阶弯曲模态振型
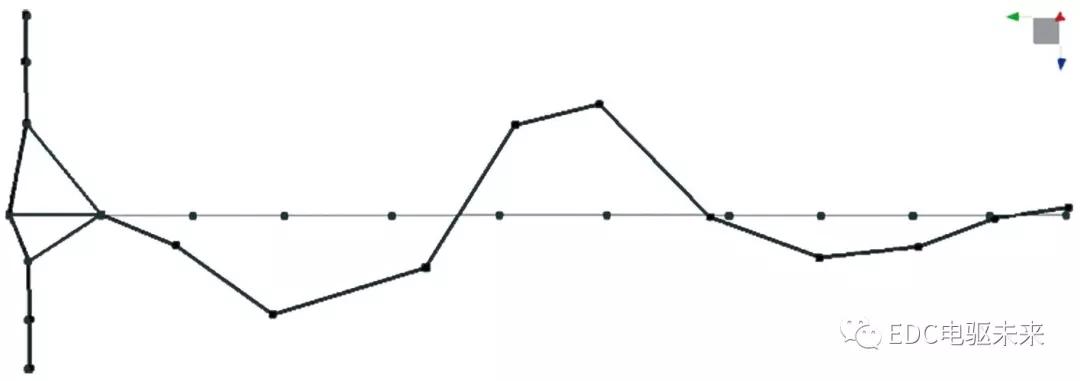
图9 161.0 Hz横向三阶弯曲模态振型
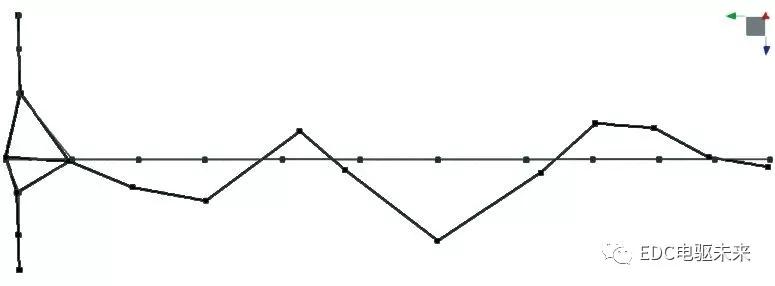
图10 240.0 Hz横向四阶弯曲模态振型
3 传动系弯曲模态优化
3.1 模态敏感度试验分析
由传动系模态试验结果可知,传动系统存在与车内噪声共振频率吻合,是以传动轴振动为主的240.0 Hz横向四阶弯曲模态。为了进一步确认是否为该模态共振引起车内噪声问题,在后桥输入端、第三段传动轴中间、第二段传动轴中间和第一段传动轴中间加7 kg质量块,对空档工况实车响应和传动系统模态进行测试。图11为传动轴不同位置加7 kg质量块后车内噪声总级曲线。表1为传动轴不同位置加7 kg质量块后传动系统四阶弯曲模态。从试验结果可以看出,传动轴加质量后,传动系统四阶弯曲模态频率均有下降,同时车内噪声亦均有下降。
由此结果可以判断,车内噪声问题的产生确实与传动系统四阶弯曲模态共振有关。第二段和第三段传动轴中间加7 kg质量块时,传动系统四阶弯曲模态频率下降最为明显,可达10.0 Hz,同时车内噪声幅值亦下降最明显,下降量级均可达到4~9 dB(A)。后桥输入法兰加7 kg质量块后,车内噪声改善量相对较少约2~6 dB(A)。第一段传动轴中间加7 kg质量块时,传动系统四阶弯曲模态频率下降最少,车内噪声只在部分转速有明显改善。综上所述,该四阶弯曲模态质量最敏感的位置位于第二段和第三段传动轴中间位置,而从工程可实施性方面考虑,后桥输入端加质量块可调整传动系统质量分布,以改善该车车内噪声问题。另外,该试验中,虽然未将传动系统模态与激振力频率避开,但是质量块的增加使得模态响应幅值降低,从而使得车内噪声有明显改善。这说明在解决此类频率相对较高的结构模态问题时,除了考虑模态分布外,还应重视模态响应幅值的降低。
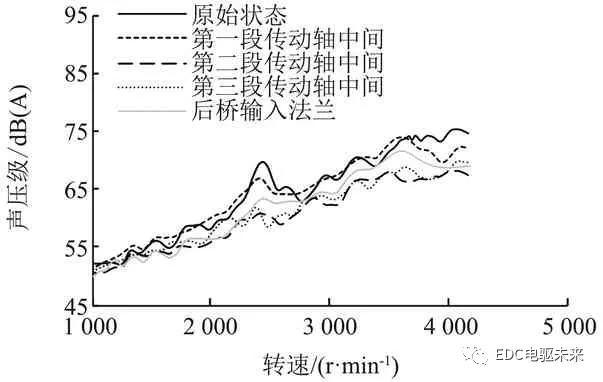
图11 传动轴不同位置加7 kg质量块车内噪声总声压级
表1 传动轴不同位置加7 kg质量块后传动系统四阶弯曲模态
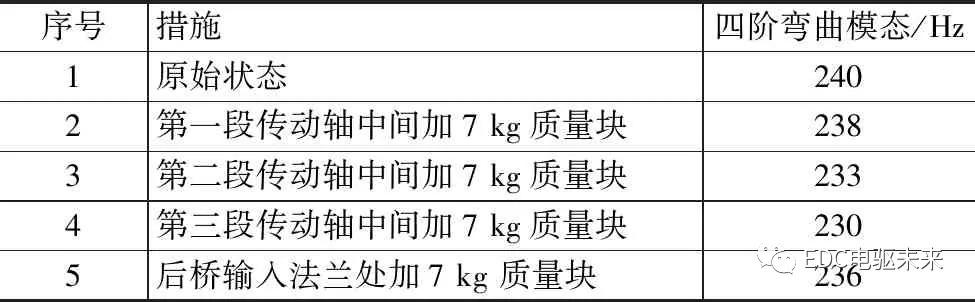
3.2 仿真分析及优化
由试验分析可知,后桥输入端适当增加质量,可改善该问题,但改善量不足,需从优化传动系统结构本身来解决该问题。因此针对该车型建立传动系统弯曲模态有限元模型,如图12所示。在与试验模态测试激励点相同位置施加单位激励,得到传动轴频响曲线,与试验得到的传递函数曲线对比如图13所示,仿真得到的模态频率和幅值均与试验基本一致,该模型可用于优化得到有效的改进措施。基于该模型,提出前中间支撑后移150 mm和前中间支撑后移150 mm,同时中间轴管径变大11 mm(由78 mm增加到89 mm)2种改进措施,分别称为方案1和方案2,其传递函数曲线对比如图14所示。这两种措施均可有效提升传动轴频率在240.0 Hz的四阶弯曲模态,可明显降低频率在240.0 Hz处的响应,并消除该频率处峰值特征。2种方案相比,方案2对传动系统四阶弯曲模态频率提升更多,幅值也下降更多。
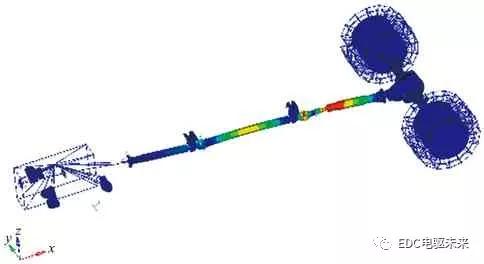
图12 传动系统有限元模型
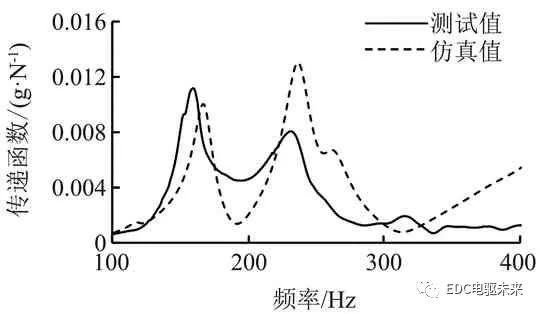
图13 传动系统测点传递函数测试和仿真曲线
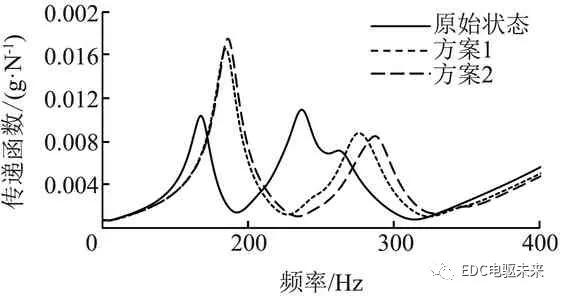
图14 优化方案传动系统测点传递函数曲线
3.3 优化方案效果验证
根据仿真分析结果,选择方案2,制作样件,并实车验证该优化方案效果,优化前后车内噪声总声压级曲线,如图15所示。车内噪声全转速段都有明显改善,240.0 Hz传动系统四阶弯曲模态共振引起的峰值处下降最为明显,最高可达7 dB(A),峰值特征基本消除,加速更为线性,品质感明显提升。由结果可知,优化传动轴支撑点的位置可有效提升传动系统弯曲模态频率,并降低其响应,有效解决由其引起的车内噪声问题。
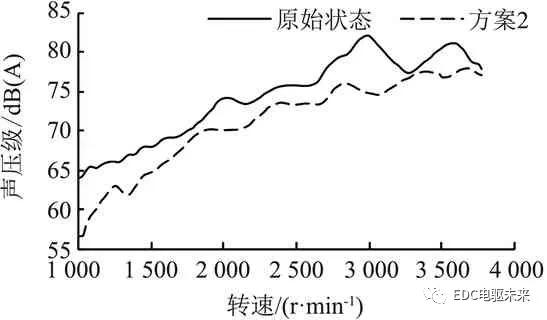
图15 优化前后车内噪声总级曲线
4 结论
针对某后驱柴油车型车内噪声240.0 Hz共振引起的多个轰鸣声问题,首先对传动系统弯曲模态试验方法和影响因素进行研究,然后分析模态灵敏度,最后提出优化方案并验证其效果,得出如下结论:
(1) 在传动系统弯曲模态试验中,传动系统间隙和变速器档位对弯曲模态试验结果有明显影响,应尽可能减少其造成的试验误差;
(2) 在解决此类频率相对较高的高阶弯曲模态问题时,除了考虑模态分布外,还应重视模态响应幅值的降低;
(3) 优化传动轴支撑点的位置可有效提升传动系统弯曲模态频率,并降低其响应,有效解决由其引起的车内噪声问题。
来源:EDC电驱未来
作者:王媛文