在动力总成性能验证领域,当前行业普遍采用分散式单体台架测试与整车迭代验证相结合的作业模式。但独立模块的逐项验证不仅需要配置多套专用台架及整车资源,导致设备投入与场地成本居高不下;更关键的是割裂了动力总成各子系统间的动态耦合关系,难以实现NVH、热管理、传动效率等关键性能的协同优化。此外,台架工况与真实道路环境存在的显著偏差,往往导致实验室数据与实车表现产生系统性误差,迫使企业投入大量时间进行重复验证。
近日,中汽中心工程院智能声振开发团队开发出了基于台架的动力总成多性能联调解决方案。该方案将台架信号、测试信号与HIL系统相连,集成动力总成在整车域运动性能的模拟测试,并在台架上实现实时的扭矩响应,使台架运行环境更贴合整车实际运行工况;能够实现动力总成多性能联调实时标定;能够兼容企业现有NVH、热管理、传动效率等研发流程,将整车综合验证周期缩短2-3个月,为动力总成的多属性联合开发提供全新、高效的解决方案。
1、台架搭建
图 1 硬件在环HIL台架的搭建
在传统动力总成台架的基础上,获取台架控制权限,并与HIL机柜实时通道进行信号匹配,搭建测试样件的硬件在环HIL系统,如图1。测试时,通过实时控制软件定义试验类型和工况,调用相应的实时仿真模型输出信号给台架执行器,控制样件动作;动作完成后,通过传感器获取执行结果,反馈给仿真模型进行实时计算,动态调整。
根据不同的测试目的,台架配备了振动噪声传感器、油耗仪、扭矩遥感、功率分析仪等设备,进行动力总成NVH、油耗、效率等多性能联调标定验证。
2、软件开发
包含更精确的发动机模型,可模拟其真实扭矩信号,包含从性能MAP中提取的基础扭矩、整车道路工况变化时的瞬态扭矩和发动机燃烧产生的扭矩正弦波动。经过测试验证,发动机扭矩的模拟值和整车环境的测试值具有高度一致性。
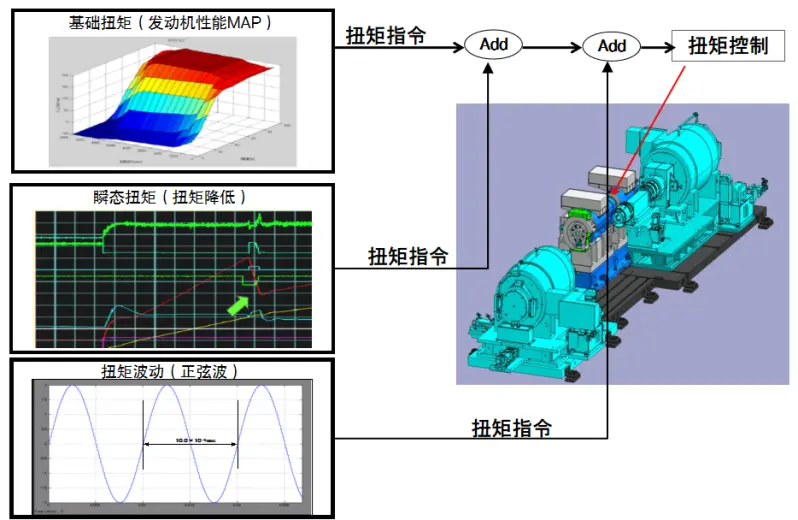
图 2 发动机扭矩模拟构成图
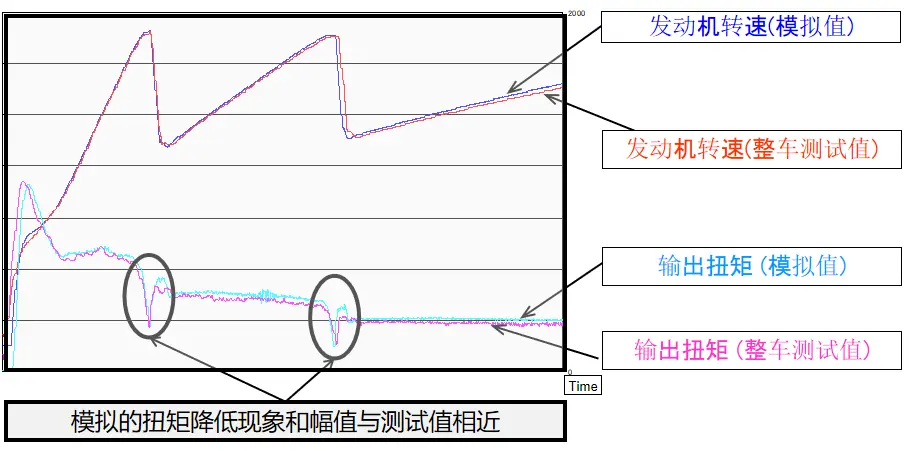
图 3 发动机扭矩模拟值与测试值对比
包含更精确的道路模型,可设置5~20Hz的正弦波轮速指令,模拟路面颠簸产生的转速波动,也可根据实际采集的数据设置不同路面参数,同时,也可根据一维计算中的转速波动值实时控制车轮转速。
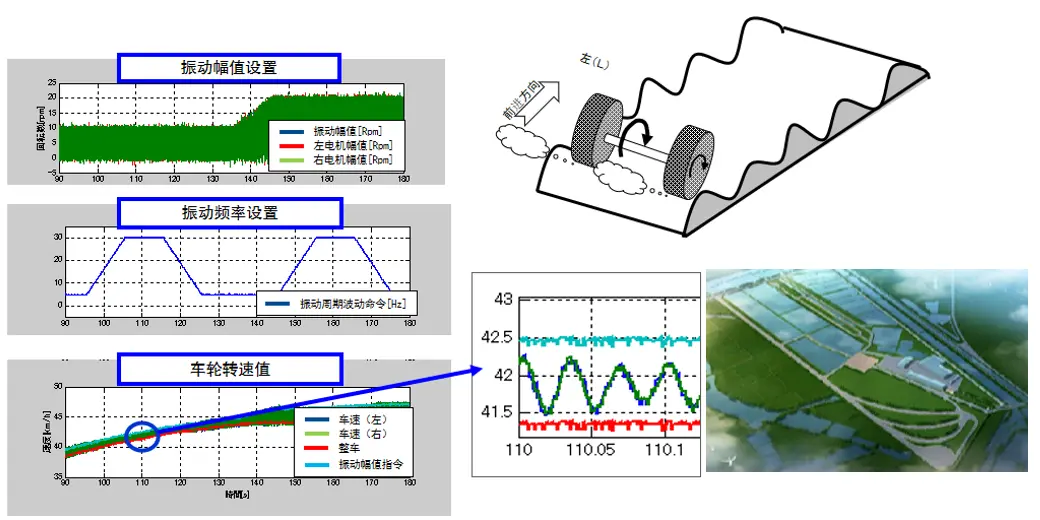
图 4 道路模拟结果图
根据客户需求不同,定制不同车型的动力学模型,实现实时驾驶模拟。
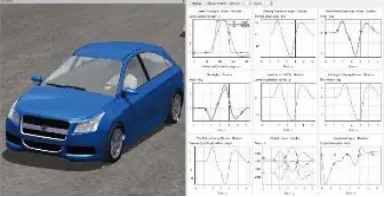
图 5 不同车型运动学模型
包含传动系统动力学模型,包含发动机、电驱、传统变速箱、混动变速箱、整车传动链等关键系统模型。
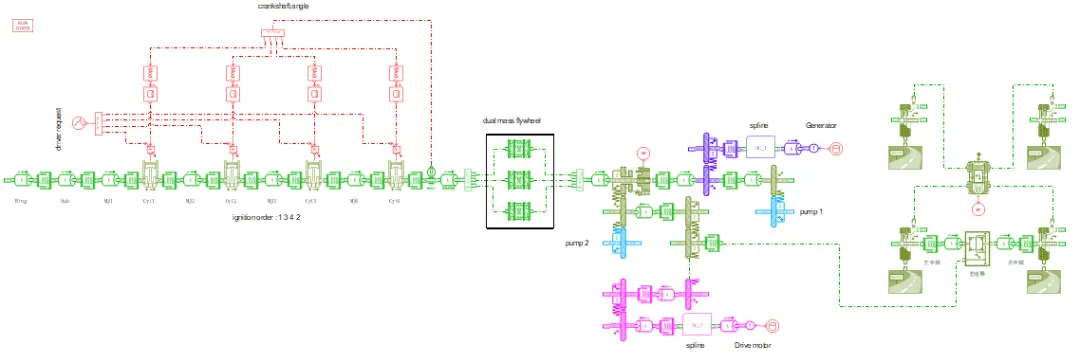
图 6 传动系统模型
3、功能应用
来源:中汽中心工程院