由于全轮驱动系统技术能够使车辆拥有更好的稳定性、通过性和操作性能,所以使其成为当前越野汽车的主要特征之一,而分动器则是汽车实现全轮驱动的核心部件。当前四驱系统的工作方式主要有分时四驱、全时四驱、适时四驱三种模式,操作形式则可分为手动和电动两种形式。手动分动器需要驾驶员在多变的越野路况下操作换挡杆,并兼顾其他操作,对驾驶技术要求高,而且分动器有特定的档位顺序和换挡条件,驾驶员易造成误操作。然而电控分动器以换挡按钮作为输入信号,从而由驱动电机进行换挡。虽然电控分动器具有换挡简单、安全性好等优点,但存在以下难点:换挡操纵装置的开发、分动器控制器TCU的开发、控制策略的开发、台架实验困难。针对上述问题,设计了具有“滑动齿套差速不传扭”特点的行星差速换挡机构。设计控制器和编写程序完成对整车状态信息采集,准确判断驾驶员操作意图,从而发送换挡指令顺利完成换挡以及信息提醒。最后,在实验台架上进行全时四驱电控分动器的台架疲劳耐久试验以及电控换挡操纵系统循环换挡10万次目标耐久试验。
1 背景介绍
为充分发挥四驱车辆的性能和提供对车辆的传动系统的保护,本款全时四驱电控分动器设置有四个行驶模式,分别为HL、H、N及L模式。四个模式对应着不同的适用行驶工况和车速范围,具体说明如下:
HL模式:当车辆行驶时出现轮胎打滑或车辆行驶在附着力低的路面(如结冰路面或雪地、潮湿光滑等路面)选择HL模式行驶。在HL模式下行驶,为了车辆安全,车速建议不要超过60km/h。
H模式:在城市路面等较平坦的路面、高速公路等大部分路况下,选择该H模式行驶,每次车辆下电后再次上电,分动器初始挡位默认为H挡,行驶模式旋钮默认H模式。
N模式: 当车辆出现故障,车辆无法正常行驶需要拖车时,为了对车辆传动系统的保护,拖车时,车辆分动器需要处于N档,行驶模式为N模式。
L模式:在极限工况下,如无路、越野、爬坡、越障等条件下,车辆设定为低档四轮驱动模式。在L模式下行驶,为了车辆安全,车速建议不要超过20km/h。
2 全时四驱电控分动器方案开发设计
2.1 全时四驱电控分动器本体结构设计
该款电控分动器总体结构如图1所示,主要由主要由壳体、行星减速机构、行星差速机构、换挡操纵机构、链轮链条传动机构六个部分组成。核心电控换挡操纵装置结构如图2所示,换挡电机依据换挡信号驱动换挡凸轮轴从而进行HL、H、N、L四个模式的切换。
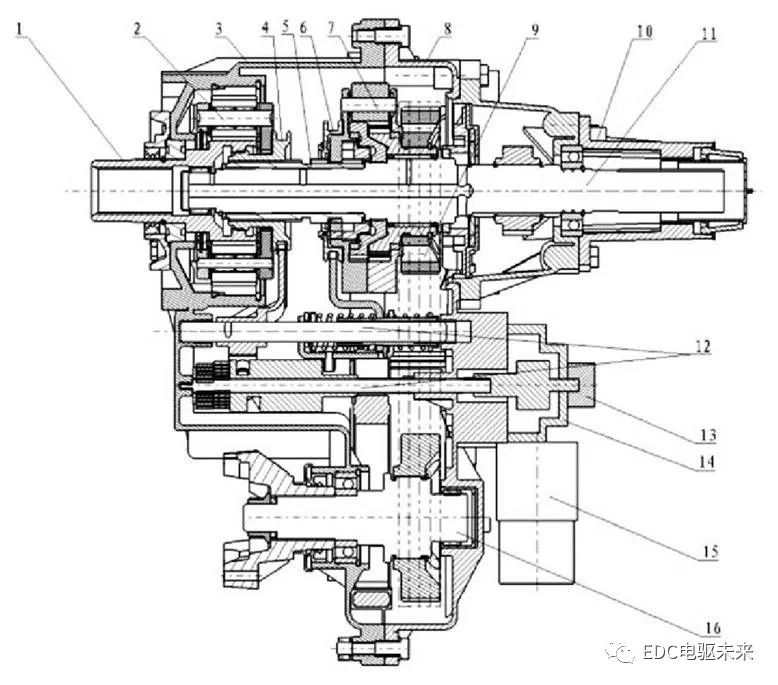
图1 全时四驱电控分动器总成机械本体结构
1-分动器输入轴 2-行星减速机构3-前壳体 4-高低档滑动齿套 5-后桥驱动轴轴套 6-差速锁止拨叉套 7-行星差速机构 8-中壳体 9-链轮传动装置 10-后壳体 11-后桥驱动轴 12-电控换挡操纵装置 13-电机位置编码器 14-电机减速器 15-换挡电机 16-前桥驱动轴
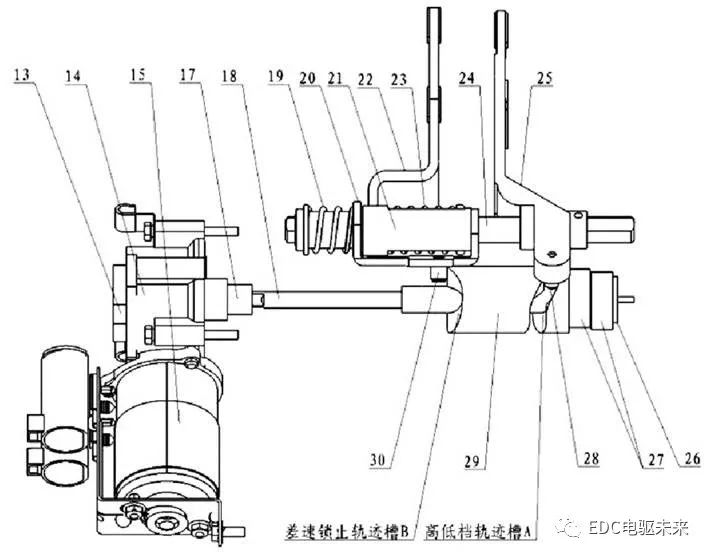
图2 电控换挡操纵装置结构示意图
13-电机位置编码器 14-电机减速器 15-换挡电机 17-电机减速器输出轴 18-换挡凸轮轴 19-差速退档弹簧 20-差速锁止导块 21-差速进档弹簧固定架 22-差速锁止拨叉 23-差速进档弹簧 24-拨叉轴 25-高低档拨叉 26-弹性件支撑片27-弹性件 28-高低档滚轮 29-凸轮 30-差速锁止滚轮
如图2所示,换挡电机15输出端和电机减速器14相连。电机减速器14端部装有电机位置编码器13,用于反馈电机位置信号。电机减速器输出轴17通过三角形凹槽和换挡凸轮轴18轴端的三角形凸起连接,凸轮29和弹性件27空套在换挡凸轮轴18上。弹性件支撑片26和换挡凸轮轴18采用焊接或铆接,可同步旋转。差速退档弹簧19、差速锁止导块20、差速进档弹簧固定架21、差速锁止拨叉22、差速进档弹簧23和高低档拨叉25均空套在拨叉轴24上。凸轮29上设有高低档轨迹槽A和差速锁止轨迹槽B,高低档滚轮28一端在高低档轨迹槽A内,另一端固定在高低档拨叉25上。差速锁止滚轮30一端在差速锁止轨迹槽B内,另一端固定在差速锁止导块20上。
高低档轨迹槽A为封闭式,换挡时,由轨迹槽推动高低档滚轮28和高低档拨叉25沿拨叉轴24左右运动,执行换挡操作。差速锁止轨迹槽B左半边为开放式,当由N(非锁止)档进入L(锁止)档时,轨迹槽B推动差速锁止滚轮30、差速锁止导块20、进档弹簧固定架21向左运动,压缩进档弹簧23,由进档弹簧23推动差速锁止拨叉22向左运动,进入L档,同时压缩退档弹簧19;而从L(锁止)档退入N(非锁止)档时,轨迹槽B仅给滚轮30留出向右运动的空间,由退档弹簧19提供退档力。
下面以从HL(高速锁止)档换入N档(空档)为例,介绍电控换挡操纵装置的实施方式。如图2所示,当驾驶员将档位选择开关由HL置为N,分动器控制单元判断车辆状态是否满足换挡条件,若满足,则驱动换挡电机15通过弹性件27推动换挡凸轮29按照图2中箭头所示方向旋转α°,旋转过程中,凸轮29上的高低档轨迹槽A不断向左延伸,推动轨迹槽内的高低档滚轮28和高低档拨叉25沿拨叉轴24向左运动,从H(高速)档进入N档(空档)。与此同时,旋转过程中,由于凸轮29上的差速锁止轨迹槽B向右延伸,而轨迹槽B左边为开放式,这样就给差速锁止滚轮30留出了向右运动的空间,退档弹簧19推动差速锁止滚轮30和差速锁止拨叉22沿拨叉轴24向右运动,从L(锁止)档退入N(非锁止)档。以此类推,当换挡电机15带动凸轮29旋转时,轨迹槽推动两组滚轮和拨叉沿拨叉轴运动,使得分动器进入相应档位。
2.2 全时四驱电控分动器控制器设计
全时四驱电控分动器控制器作为全时四驱电控分动器总成的核心部件,对分动器的正常工作关系重大,而硬件则又是控制器能够稳定、安全工作的基础和保障。
经过分析,分动器控制器的主要功能有以下三点:换挡电机控制、换挡电机位置检测以及系统故障诊断。针对以上三项功能,系统分动器控制器电控单元原理图如图3所示,控制器主要包含电源、信号采集、CAN通信、驱动和电流检测及驱动保护等部分。其中开关信号包含档位选择、离合器位置、制动等信号。转速信号和换挡信号经过处理后进入控制器,分动器控制器采通过马达位置编码器检测档位位置。比较换挡信号和换挡后实际位置形成位置闭环控制,从而准确完成档位调换。

图3 电控分动器控制器原理图
2.3 控制策略设计
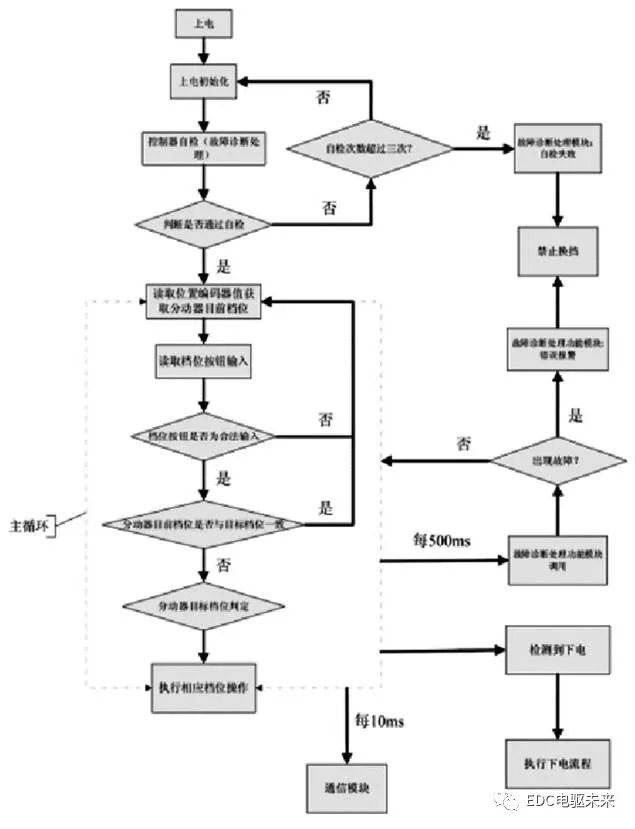
图4 换挡控制策略流程图
为满足全时四驱电控分动器功能要求和安全需求,软件整体策略由上电初始化自检模块、换挡模块、通信模块、故障诊断模块和下电处理模块等组成。在程序主循环中,控制器通过马达位置编码器和档位选择按钮不断读取分动器当前档位和目标档位,设置换挡条件进行此次换挡行为的合法判断从而决定是否执行换挡操作。当目标档位和当前档位一致时则等待条件满足和新的档位选择开关信号。当目标档位和当前档位不一致时进行换挡条件判定,如果满足则执行换挡操作。为增强分动器的可靠性和可维护性,主程序中同时设置周期为500ms的故障诊断程序为驾驶员提供可能出现的故障参考。全时四驱电控分动器控制策略原理图如图4所示。
2.4 故障诊断系统设计
由于复杂电路的使用,全时四驱电控分动器在为驾驶员提供操作方便的同时也降低了其可维护性。针对出现故障时检查度大、专业能力要求高的问题,控制器中设计了完善的故障诊断系统,故障诊断主要内容见表5。整车CAN依据故障代码将故障类型显示在显示屏上或由专业汽车维修人员通过整车CAN读取故障码判断故障类型。
表5 故障码对应的故障信息以及处理措施
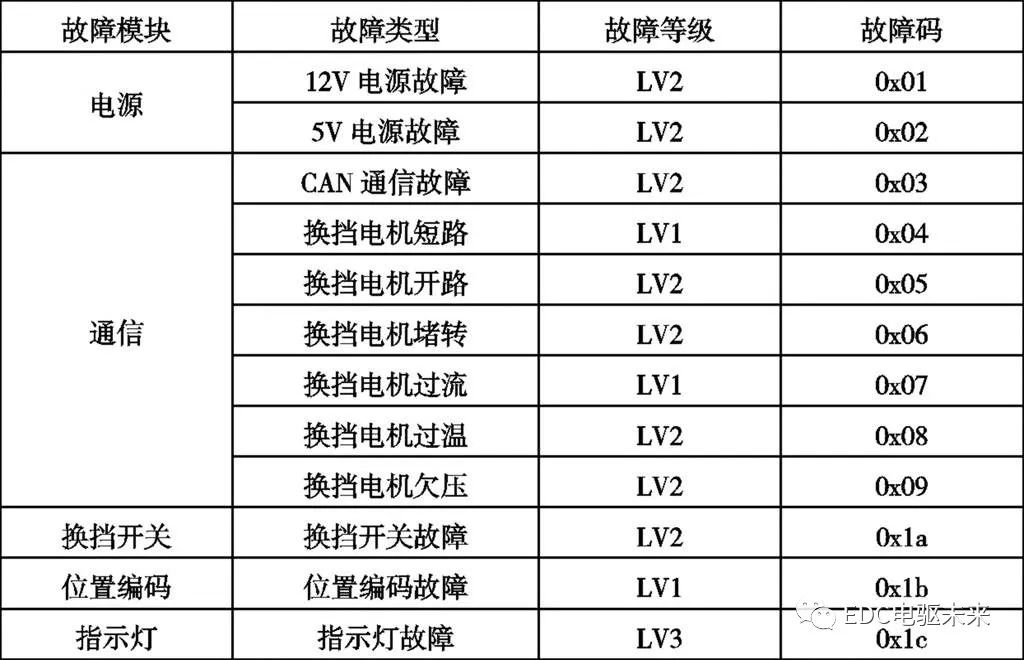
3 换挡可靠性台架试验设计
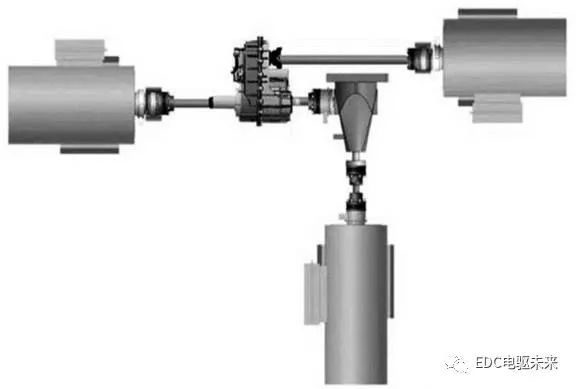
图6 分动器模拟换挡测试台架布置
全时四驱电控分动器开发定型过程中以及产品量产后需要定期在带前后负载的专业检测台架上进行电控分动器换挡功能可靠性的检测认可试验。试验样品进行台架试验时,全时四驱电控分动器装于试验台上应与其在汽车上的实际工况相似。试验测试台架所需的一台驱动电机、两台测功机布置安装根据电控分动器的偏置进行适应调整。根据分动器中心距离以及在整车上的偏置角来设计台架试验工装,将被测试的样品安装固定。输入电机、输出测功机,试验样品在台架布置如图6所示。
测试内容需要根据实际电控分动器各档位排列设计顺序来确定。测试台架监控各档位是否按照设计的台架既定换挡策略进行换挡,反馈换挡成功与失败次数。由于目前开发电控分动器四个挡位是按照HL、H、N、L进行依次排列设计,为了验证设计换挡机构可靠性,将按照上述四个挡位测试内容进行可靠性台架试验。电控分动器换挡可靠性台架试验测试结果包括以下内容如表7所示。
表7 全时四驱电控分动器换挡可靠性台架试验测试结果
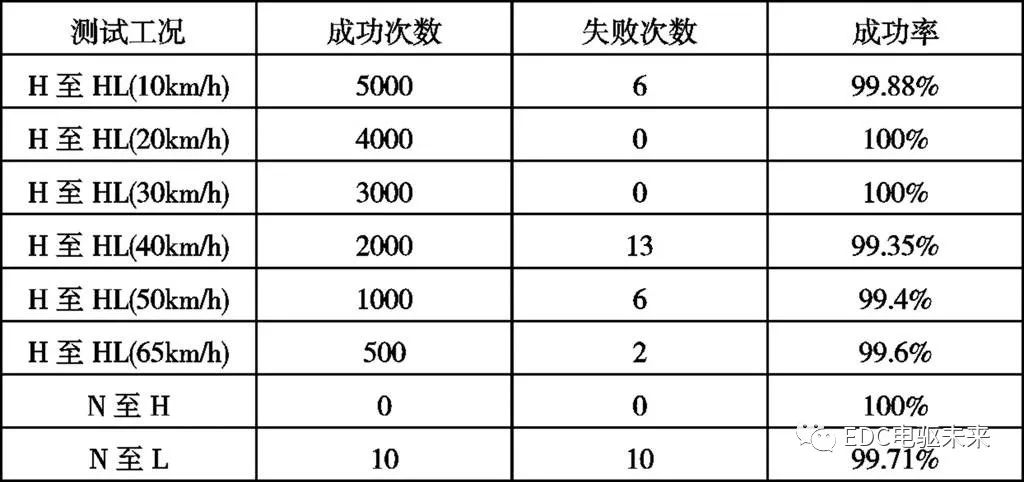
对于测试过程中出现的较小频次换挡失败现象,经过分析原因如下。电控分动器换挡操纵机构的换挡拨叉齿套与结合齿在换挡过程中会较小概率的出现需要换挡力较大情况。当换挡电机提供的换挡力小于需要的换挡力时,换挡机构中具有换挡缓冲作用的扭簧给换挡机构蓄能,保证换挡电机不会堵转。当换挡马达的位置编码器识别到目标挡位时,电机停止转动,具有自锁功能的换挡机构锁止电机不会反转。但是,实际分动器换挡拨叉没有到位,当外界需要的换挡力变小时,扭簧提供的换挡力满足换挡力需求时,换挡拨叉到位,即在实际工作中表现为换挡到位需要延迟一定时间。由于台架换挡测试的连续性以及台架控制标定时间参数与实际试验测试的全过程不可能完全匹配,所以台架测试时会出现换挡失败现象。这种出现频次在测试过程中出现的概率较小,一般要求在2%以内是可以接受的。
4 结束语
本文在手动分动器的基础上开发全时四驱电控分动器,在档位操纵机构上面使用步进电机、凸轮、位置编码器等来完成换挡动作和位置检测。同时使用弹性件,避免机构因刚性连接而损坏,同时可以实现在车速小于60km/h时换H挡与HL挡,在车速小于2km/h时实现换L挡和N挡。自主开发的电控分动器控制器TMM和换挡控制策略,可准确判断驾驶员意图,根据采集的车辆状态信息,发送换挡指令,并可与仪表进行通讯,在仪表上显示相关信息等。通过分动器试验台架对全时四驱电控分动器总成进行最后的台架试验,试验表明,该总成稳定可靠,达到设计要求。文章介绍了电控分动器开发的主要内容,为其它汽车上控制器的开发提供了参考。
来源:EDC电驱未来
作者:刘志柱