针对奔驰E300 V6发动机与C200 L4发动机在冷测试中不同的正时测试项目进行了分析,逐一描述其检测点所代表的内容,并结合实际生产案例对测试项目进行了描述,同时对奔驰E300发动机的可变正时系统进行了简要介绍。
发动机正时系统
发动机正时系统主要由ECU(电子控制单元)和传感器等组成。发动机曲轴位置传感器用于采集曲轴转动角度和发动机转速信号,并输入ECU以确定点火时刻和喷油时刻。凸轮轴位置传感器用于采集进排气凸轮轴的位置信号,并与曲轴位置传感器一同确认发动机一缸上止点,用于燃油喷射控制、点火时刻控制等。奔驰C200及E300发动机采用的是磁感应式曲轴与凸轮轴位置传感器。
如图1所示,发动机发信轮的飞轮齿圈周围有一圈齿盘作为信号转子,齿圈圆周均匀分布有58个窄齿和1个宽齿。宽齿输出基准信号,对应发动机一缸或四缸压缩上止点前一定角度。宽齿所占的弧度相当于两个窄齿所占的弧度。因为信号转子随曲轴一同旋转,所有信号转子圆周上的宽齿和窄齿所占的曲轴转角为360°,每个窄齿所占的曲轴转角均为6°,58个窄齿对应348°,宽齿所占的曲轴转角为12°。
当曲轴转动时,磁感应式曲轴位置传感器会周期性的产生交变电压,输出交变电压信号。ECU通过接收脉冲信号来判断上止点的到达时刻。由于信号转子上有58个凸齿,因此信号转子每转一圈(发动机曲轴转一圈),传感线圈就会产生58个交变电压信号输入ECU, 因此,ECU每接收到曲轴位置传感器58个信号,就可知道发动机曲轴旋转了一圈。
通过检测曲轴位置传感器的信号,ECU可以精确计算出发动机的转速。同样,ECU可以通过凸轮轴位置传感器信号获取凸轮轴电压信号。
通过判断曲轴位置及凸轮轴位置,ECU便可以确定发动机喷油时刻及点火时刻等基本控制参数。
发动机可变气门正时
目前我公司所生产的各种型号的发动机都采用了可变气门正时技术,即所谓的VVT (Variable Valve Timing),以提高进气充量,使充量系数增加,进而提高发动机转矩和功率等性能。
发动机不同转速下也要求可变配气正时机构进行相应的调节,这是因为,当发动机转速改变时,由于进气流速和强制排气时的废气流速也随之改变,因此在气门晚关期间利用气流惯性增加进气和促进排气的效果将会不同。例如,当发动机低速运转时,气流惯性小,若此时配气定时保持不变,则部分进气将被活塞推出气缸,使进气量减少,气缸内残余废气将会增多。当发动机高速运转时,气流惯性大,若此时增大进气迟后角和气门重叠角,则会增加进气量并减少残余废气量,使发动机的换气过程更完善。
合理选择配气正时,保证最好的充气效率ηv,是改善发动机性能的重要技术途径。图3所示为可变气门正时的角度。在进、排气门开闭的四个冲程中,进气门迟闭角的改变对充气效率ηv影响最大。进气门迟闭角改变对充气效率ηv和发动机功率的影响可以通过图4进一步了解。
图4 中每条充气效率ηv曲线体现了在一定的配气正时下,充气效率ηv随转速变化的关系。如迟闭角为40°时,充气效率ηv是在约1800r/min的转速下达到最高值,说明在这个转速下工作能最好地利用气流的惯性充气。当转速高于此转速时,气流惯性增加,就使一部分本来可以利用气流惯性进入气缸的气体被关在气缸之外,加之转速上升,流动阻力增加,所以充气效率ηv下降。当转速低于此转速时,气流惯性减小,压缩行程初始时就可能使一部分新鲜气体被推回进气管,充气效率ηv也下降。
图中不同充气效率ηv曲线之间,体现了在不同的配气正时下,充气效率ηv随转速变化的关系。不同的进气迟闭角与充气效率ηv曲线最大值相当的转速不同,一般迟闭角增大,与充气效率ηv曲线最大值相当的转速也增加。迟闭角为40°与迟闭角为60°的充气效率ηv曲线相比,曲线最大值相当的转速分别为1 800 r/min和2 200 r/min 。由于转速增加,气流速度加大,大的迟闭角可充分利用高速的气流惯性来增加充气。
总之,四冲程发动机的配气定时应该是进气迟后角和气门重叠角随发动机转速的升高而加大。如果气门升程也能随发动机转速的升高而加大,则将更有利于获得良好的发动机高速性能。
奔驰所采用的可变气门正时技术为双VVT连续可变气门正时技术。如图5所示,可变正时系统由ECU协调控制,各部位的传感器随时向ECU报告运转工况, ECU根据需要动态调节气门正时。由于在ECU中储存有气门最佳正时参数,所以ECU会随时控制凸轮轴可变正时电磁阀从而间接控制液压阀,根据发动机转速调整气门的开启时间,或提前,或滞后,或保持不变。叶片式的凸轮轴调节器由控制柱塞调节,控制柱塞装配在凸轮轴前端,位于调节器中心固定螺纹孔内。凸轮轴调节器的机油供应来自凸轮轴的油道。若电磁阀被触发,机油在压力的作用下经过控制柱塞到达凸轮轴调节器。根据触发的程度不同,控制柱塞便会被不同程度地操控,相应地,不同数量的油便会到达凸轮轴调节器叶片,叶片被密封在调节器壳体内,在机械限制的范围内带动凸轮轴来回转动,从而实现对凸轮轴的调节。若电磁阀不再被激发,则由弹簧控制回位。为了避免发动机起动时产生的噪声,凸轮轴调节器由一个锁止螺栓轴向锁死(奔驰M271发动机为垂直方向锁死),再次激发时由油压解锁。被锁定的曲轴转角起始位置是: 进气凸轮轴 +36° (ATDC) ,排气凸轮轴 -20° (BTDC)。
E300发动机左右两排气缸对应的可变气门正时机构均设置了一个可变气门正时电磁阀,由其控制对应的电磁中心柱塞(如图6所示)。发动机获得转速传感器的信息后,对左右两排气缸对应的可变气门正时电磁阀的控制方式做出正确选择并控制中心柱塞的动作。当获得不同阀体位置时,通往可变气门正时调节器内的液压缸油路变换,使得可变气门正时调节器上升或下降,使左右两排气缸对应的进气门获得不同的迟闭角。其凸轮轴调节范围为,进气凸轮轴:上止点前4°至上止点后36°;排气凸轮轴:上止点20°至上止点后20°。 进排气门最大重叠角4°+20°=24°。
可变气门正时系统测试
可变气门正时系统非常重要,因此,必须通过严格的测试。我公司采用冷测试,且所有的测试都是基于一个触发点来进行,而凸轮轴位置传感器与曲轴位置传感器常被用作这一触发点。
1.检测方案一
可变气门正时发动机需要控制和检测移相器。 对凸轮轴响应时间的评估和显示将包括移相器变化的速度以及达到要求角度所需时间。表1详细描述了移相器命令位置和评估类型。
凸轮轴移相器的测试过程由每转1024个脉冲的外部时钟触发并运行。同时获得曲轴和凸轮轴传感器信号。曲轴角度变化引起的曲轴和凸轮轴角度的变化值将被记录并用图线画出。合成的图线将是斜线,它的起点表明凸轮轴移相器的初始位置,峰值点表明最大行程位置。测试曲线见图9。
2.检测方案二
由于可变正时调节是调整进排气门的开启关闭时刻,而根据前面我们对排气压力曲线的分析可知,相应的进排气门开启及关闭时刻,在对应的排气压力曲线上能够比较明显检测出来,因此,我们还可以间接通过检测排气压力的方式对可变正时调节进行检测。该方案如图2所示。
但是由于排气压力所受外界环境以及发动机整机状态的影响比较大,而且气门开启时刻角度的微小变化在排气压力中可能体现的并不是特别明显,因此该检测方案有一定的局限性,在测试时需要更多的样本作为参考,并且需要对进排气可变正时分别进行检测,而且其检测精度要比方案一的检测精度要低很多,同时,对操作人员的综合判断能力也有更高的要求。
案例分析
1.案例一
某M272发动机在冷测试中发现CCT测试项中左侧进排气凸轮轴脉冲盘边沿角度整体向前偏移15°以上,排气压力测试项左侧3个气缸的排气压力曲线前移15°左右,导致压力测试值偏低,且可变正时测试项目的左侧进排气项目不合格,如图10所示,其中CCT的详细测试数值见表3。
发动机正时链轮的齿数为42,每个齿的角度为8.6°,而检测角度比标准下限低约15°以上,根据测试曲线的差异以及相关及测试数值推测,怀疑发动机正时错误或者脉冲盘装配错误。由于左侧进排气脉冲盘全部错位,这样,基本上判断左侧正时链轮错齿;再根据正时链轮的角度以及测试值的角度偏移量计算,如果为发动机正时错误,应该是链轮链条向前错两个齿。
拆下发动机正时前盖检查,发现左侧正时链轮错两个齿,导致正时错误。由于偏移角度过多,有可能对活塞及气门正时造成损坏,因此继续拆检缸盖以进一步检查气门及活塞,发现活塞表面有轻微的撞击痕迹,至此,基本确定为正时错误导致气门关闭时刻错误,气门与活塞撞击导致。
2.案例二
某M272发动机在测试中发现VVT测试项不合格,查看测试曲线发现,其左侧进排气凸轮轴调节曲线的走向完全相反,实际测试到的可变正时响应角度与检测标准值也是完全相反。
经过一系列检查确认后,我们将目标定在了线束针脚走向上。通过查看ECU图纸并对VVT针脚进行测量,发现发动机线束进排气凸轮轴可变正时电磁阀的针脚反向,导致在测试过程中,所有的测试指令都发向了对侧的电磁阀,引起了故障。联系生产厂家对线束针脚进行调整后,再次进行测试验证,测试结果合格,确认是由于该缺陷引起的故障。
小结
发动机正时是一个非常关键的问题,如果正时调节不正确,轻则会影响发动机的正常运转,影响发动机的功率转矩以及相关的排放标准,造成产品质量的缺陷,重则会在气门开启的过程中造成气门与活塞的撞击,严重情况下会导致气门损坏、活塞、连杆、曲轴及缸体等发生严重变形或者划伤,以致引起发动机报废及整车故障等严重后果,所以在发动机的现实装配过程中一定要严格按照设计要求及作业指导进行相关零部件的装配操作,并在后续工序中进行必要的互检、测试台检测等。
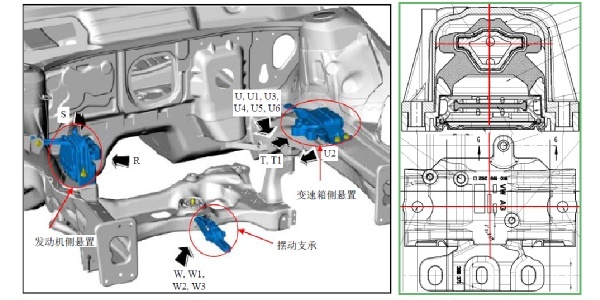
- 动力总成悬置系统疲劳强度试验标准的研究
2021-10-08
从极限竞速到未来出行新科技 Kistler车辆动力学测量技术至关重要
如今,技术的进步和移动出行的兴起,让人们的生活变得更快、更高效。近数十年来,能够精确采集车辆动力学被测变量的测量技术取得了巨大进步,并将在车辆优化中继
2020-12-2511823
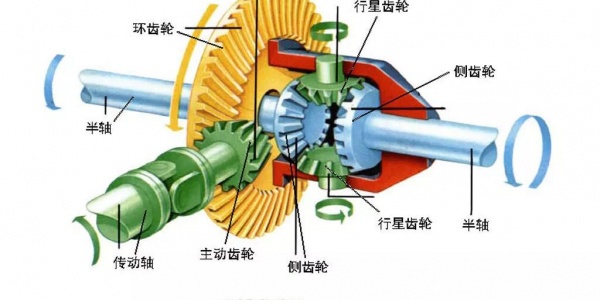
- 新能源动力总成差速器测试
2020-12-07
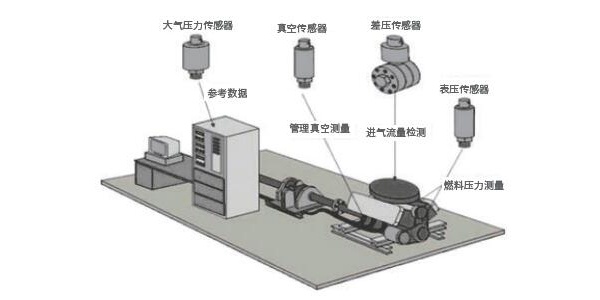
- 福禄克公司发动机及排放测试解决方案
2020-04-28
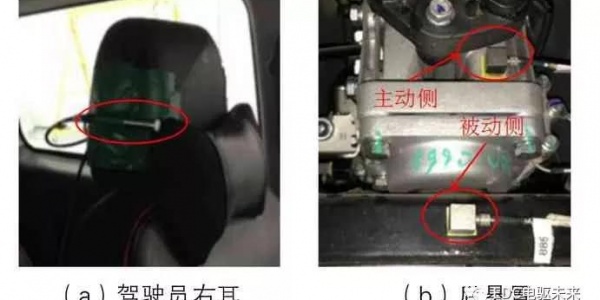
- 汽车手动变速器齿轮啸叫问题试验探究
2020-01-20
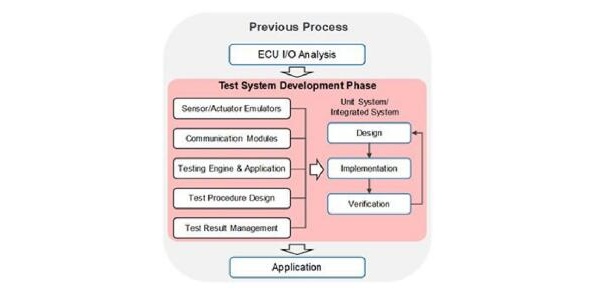
- Hyundai Kefico缩短了15%的测试时间-NI案例分析
2019-10-13
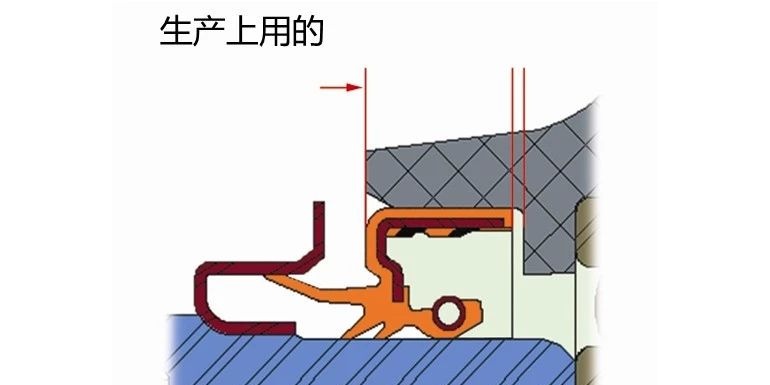
- 混合动力驱动系统油封选型与试验验证
2019-06-29
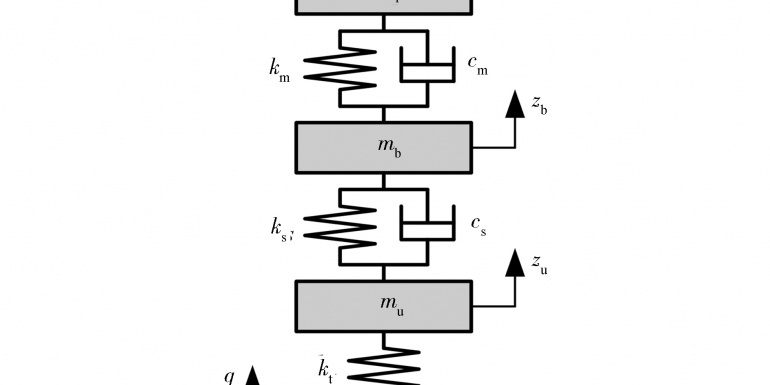
- 动力总成悬置系统对汽车动力学性能的影响
2019-06-11
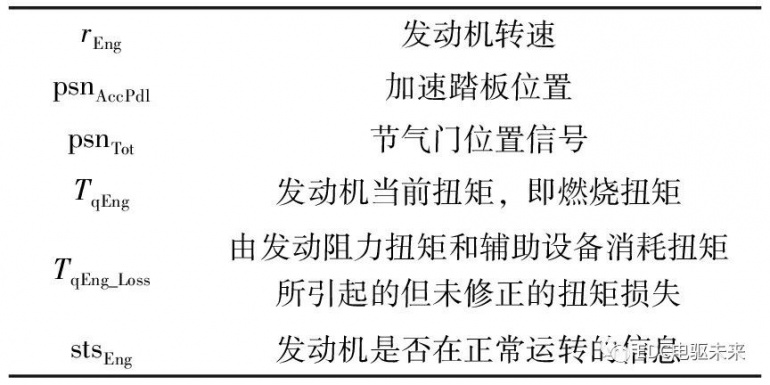
- 基于发动机转速和扭矩信号的离合状态识别研究
2019-06-09
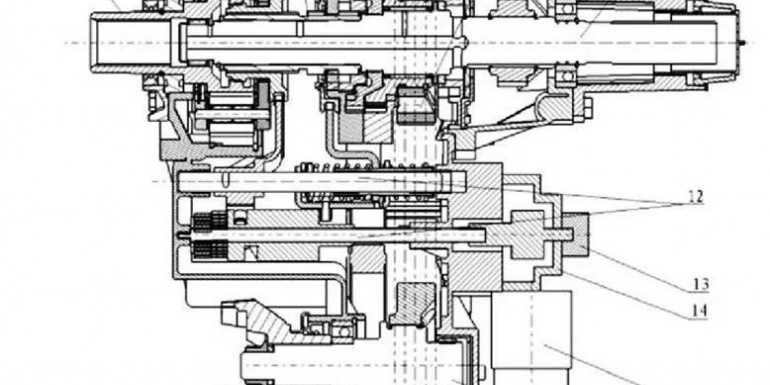
- 一款全时四驱电控分动器总成的开发介绍
2019-05-16