引言
上述研究一般仅着重于单个子系统的能耗优化,未对整车能耗作深入的探索。另一方面,在部分整车能量流分析研究中,缺乏仿真手段的介入,无法预估各子系统优化后整车能耗的变化。本文在 AMESim 提供的多物理场系统仿真环境下,搭建机-电-热耦合的整车一体化功热耦合能耗分析模型,探究电动汽车在 高温工况下各子系统的能耗占比以及整车续驶里程的估计。
01、整车功热耦合模型
1.1 动力学模型
车辆动力学模型是整车能耗分析的基础,为了兼顾仿真精度及计算效率,采用一维纵向动力学模型模 拟真实车辆的动力学特性。仿真分析之前收集车辆质量,前后轴荷,车轮半径及转动惯量等基本参数。本 文在 AMESim 中搭建的车辆动力学模型如图 1 所示。该模块考虑了风速、空气密度、路面摩擦系数、坡度 等外部环境的影响,同时也考虑了电驱零扭矩这一内部因素的影响。
在底盘测功机上模拟道路滑行试验时,通过滑行时间的迭代可以消除电驱零扭矩这一内部阻力的影响。然而,仿真环境中不具备迭代滑行的条件,因此需要将滑行试验中电驱零扭矩产生的额外阻力,以外部动 力的方式补充回动力学模型中,用以消除道路滑行试验和转毂台架试验这一边界条件的差异。本文研究车 辆涉及的电驱零扭矩等效动力如图 2 所示。由图可见,该等效动力在车速 80km/h 以下时随车速线性增长, 在 80km/h 以后维持在约 60N 左右。
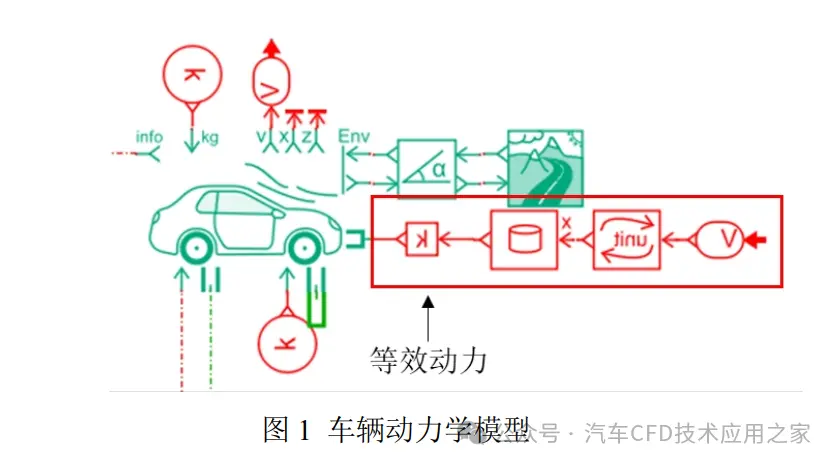
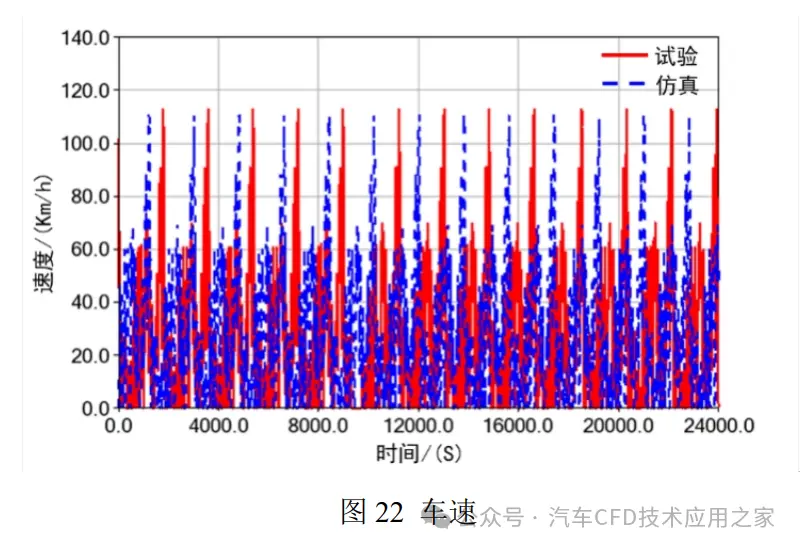
本文基于前向仿真的方式搭建整车能量流分析模型,因此需要建立驾驶员模型控制车辆模型按照外部 工况要求的速度曲线行驶。在 AMESim 中搭建的驾驶员模型如图 3 所示。驾驶员模型实时接收车辆的速度 信号以及电驱系统的转速、扭矩、最大正向扭矩、最大负向扭矩等信号,通过内置的 PID 控制器控制加速 踏板开度、制动踏板开度和挡位。加速踏板信号连同车速信号输入至油门踏板图,以查找表的方式计算出 驾驶员需求的轮端扭矩,如图 4 所示。将需求轮端扭矩传递至 VCU 整车控制器后,由 VCU 请求电驱执行 相应的驱动扭矩或制动扭矩命令。当电驱的再生制动扭矩不满足车辆制动加速度要求时,会进一步对车辆 的机械制动系统下达制动扭矩命令,由两者共同达成驾驶员请求的制动需求。
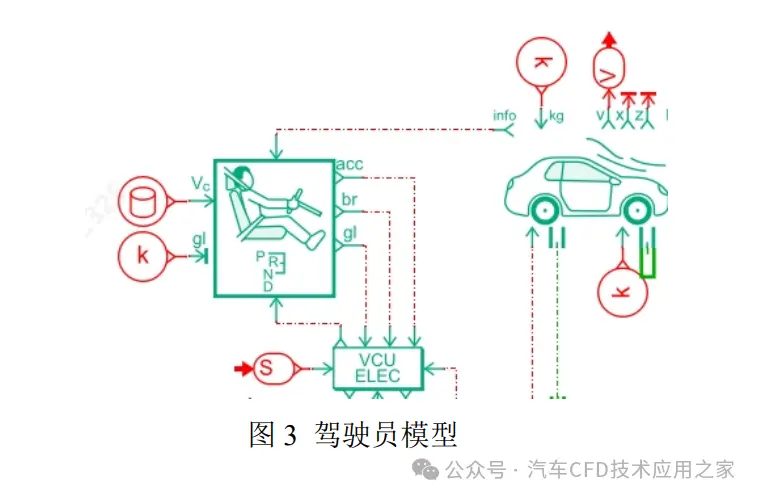
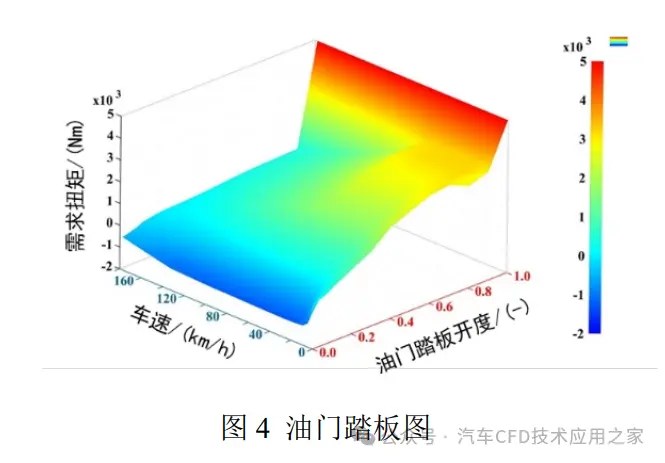
1.2 电力学模型
本文重点关注影响续驶里程的整车能量流转情况,对电驱子系统内部不作深入探究,因此以功能性电 机元件为基础对电驱系统进行建模。在 AMESim 中搭建的电驱模型如图 5 所示。以电驱台架试验效率 Map 作为电机模型的输入参数,按照接收的 VCU 扭矩请求执行扭矩输出或者扭矩输入的命令。其中,电机效 率 Map 如图 6 所示。本文涉及的传动构型为单级减速器,减速器输入端连接电机输出端,输出端连接车辆 模型的车轮端口,为其提供驱动扭矩或者接收其再生制动时传递过来的制动扭矩。
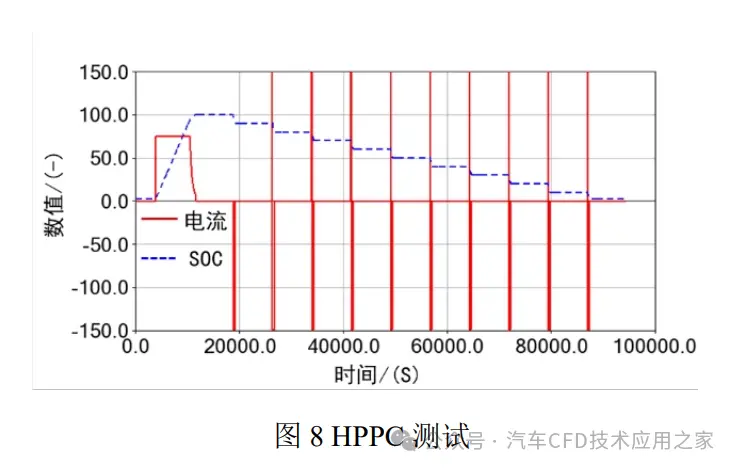
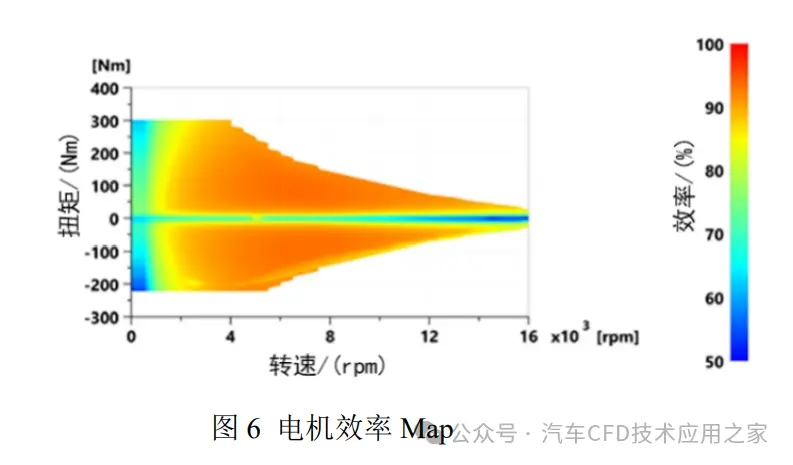
电池是纯电动汽车行驶过程中的主要能量来源,其建模精度直接影响到最终整车能耗及续驶里程分析 的精度。在 AMESim 中搭建的电池包模型如图 7 所示,每个电池包元件由 54 个电芯串联而成,两个电池 包元件共同构成 1P108S 的电池包整体架构。在与外界环境能量交换方面,主要考虑电池包水冷系统工作 带来的液体换热以及车底空气对流引发的气体换热。电池包整体的热力学参数,如等效比热容,固-液换热 系数、固-气换热系数等,由恒温仓中的电池包热平衡试验测试得到。首先由恒温箱试验确定单个电芯的电 力学特性,主要包括不同环境温度(-20、-10、0、10、25 和 45)、不同充放电倍率(1/3C、1C)下的容 量测试,开路电压测试和混合脉冲功率特性 HPPC 测试;然后用 1 阶 RC 等效电路模型进行参数拟合,用 以计算单个电芯的发热量;最后结合标定出的固-气换热系数,校核预测的电芯温度是否与测试数据吻合。容量测试和开路电压测试为电芯的等效电路建模提供基本的参数,而 HPPC 测试则主要考察电芯的欧姆内 阻、极化内阻情况。环温 25℃下的 HPPC 测试结果如图 8 所示。
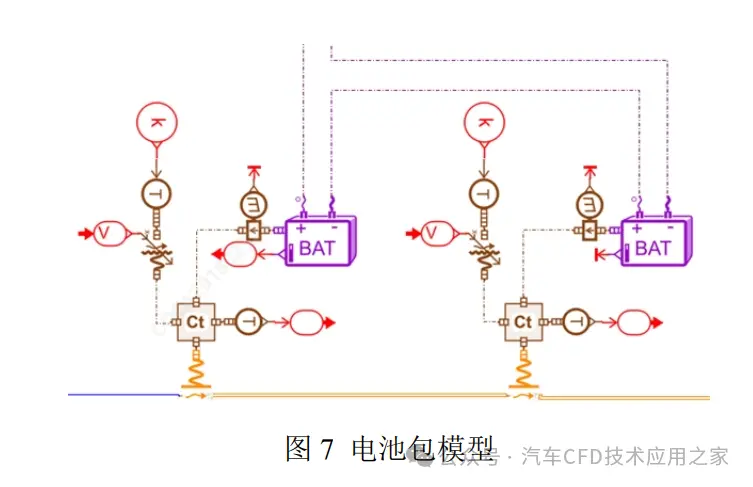
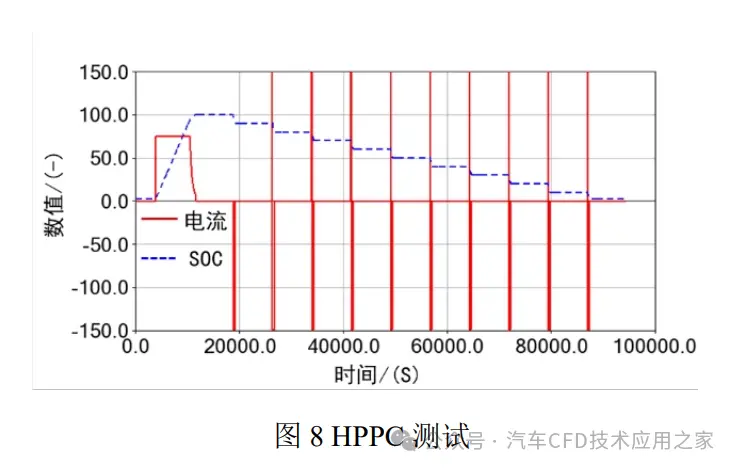
1.3 热力学模型
整车热管理系统负责高温工况下乘员舱的热舒适性,以及电驱、电池等各子系统的正常工作,其原理 如图 9 所示。本文研究车型在空调冷媒回路方面,为一典型的非热泵式并联架构。低压低温制冷剂经压缩 机压缩做功后变为高温高压气态制冷剂,进入冷凝器后经冷凝作用形成高温高压液态制冷剂,然后并联两路,一路进入暖通空调系统中的热力膨胀阀及蒸发器为乘员舱制冷,另一路经电子膨胀阀进入 Chiller 中与 冷却液换热为电池包制冷,两路冷媒在压缩机吸气口前管路汇聚,形成一个完整的循环回路。
图 9 中 PDU 模块代表配电盒、电控、电机串联而成的管路,该段管路与电子三通阀、散热器等零部 件一起构成完整的电驱冷却液回路。在该回路中,冷却液的流动由电驱水泵提供动力,电子三通阀左侧开 度比例 100%,前端模块进风量不足时,可以通过增大风扇转速为散热器提供更大的进风量。
高温工况下,电池冷却液回路与电驱冷却液回路保持独立,整个回路冷却液的流动由电池水泵提供动 力。冷却液流过电池包底部冷却板之后,进入电子三通阀,此时右侧开度比例 100%,冷却液全部进入 Chiller 与电子膨胀阀后的低温冷媒进行换热。换热过后的低温冷却液经三通阀流回电池水泵,形成一个完整的冷 却回路。
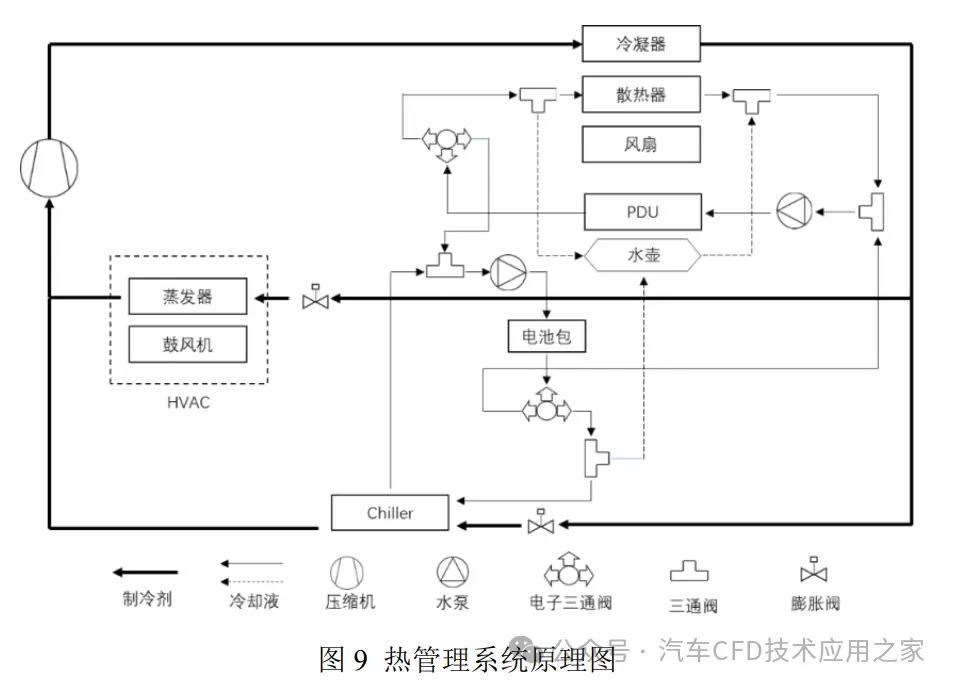
冷媒回路中的压缩机为整个冷媒回路流动提供动力,其热力学特性主要由容积效率、等熵效率、机 械效率确定。本文在压缩比 3~8 的范围之中,等间距地选取了 4 个包含上下限边界的转速进行测量。测 量得到的效率表如图 10 至 12 所示,以查找表的形式输入到压缩机元件中供建模使用。
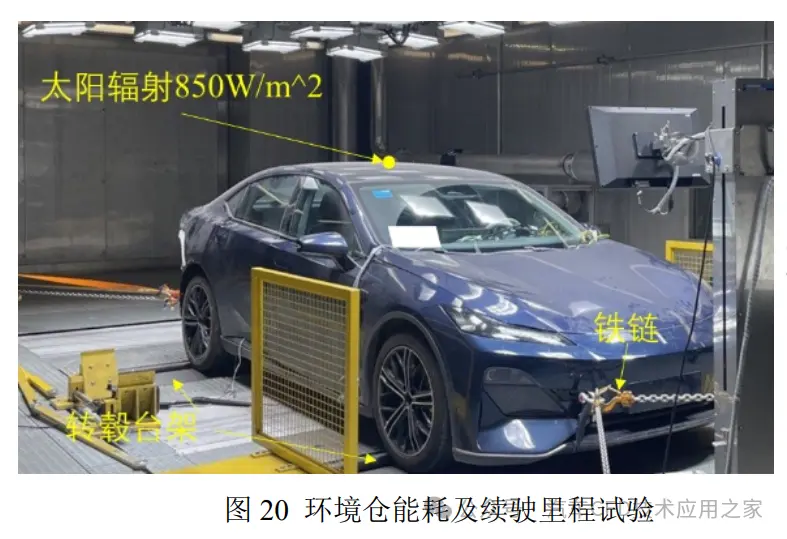
冷凝器和蒸发器是冷媒回路中两个重要的换热器,其换热量和流阻方面的建模精度对乘员舱温度、 压缩机功耗等方面有重要影响。冷凝器换热量及流阻的标定结果如图 13、14 所示,蒸发器换热量及流阻 的标定结果如图 15、16 所示。
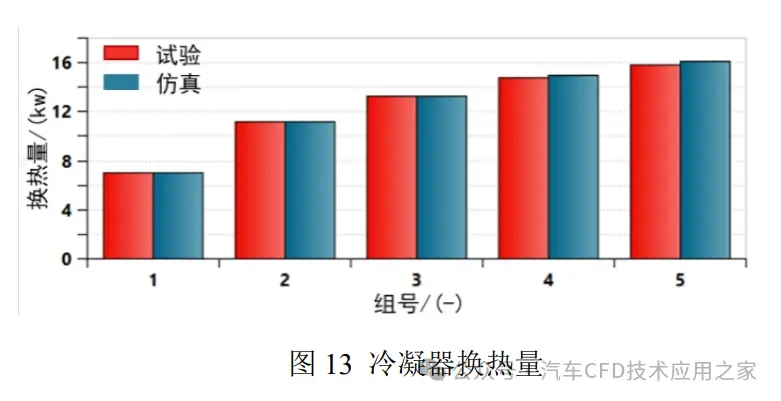
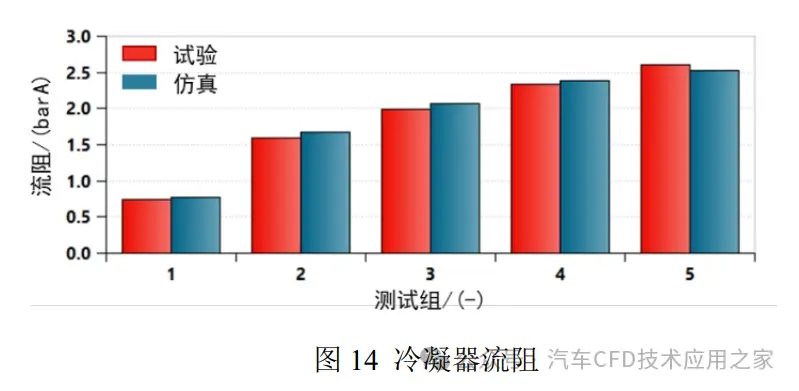
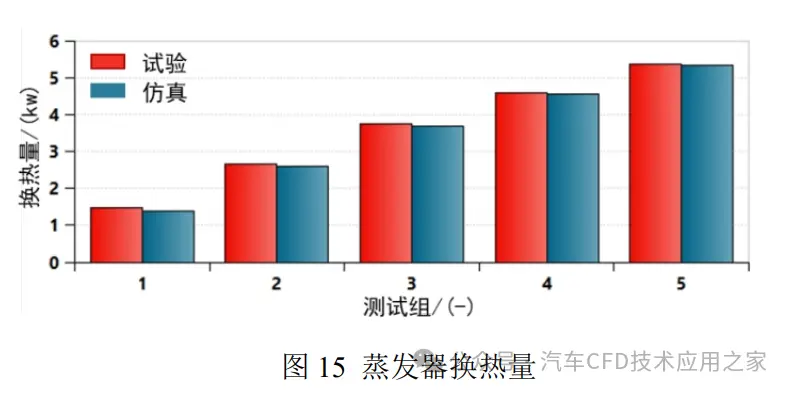
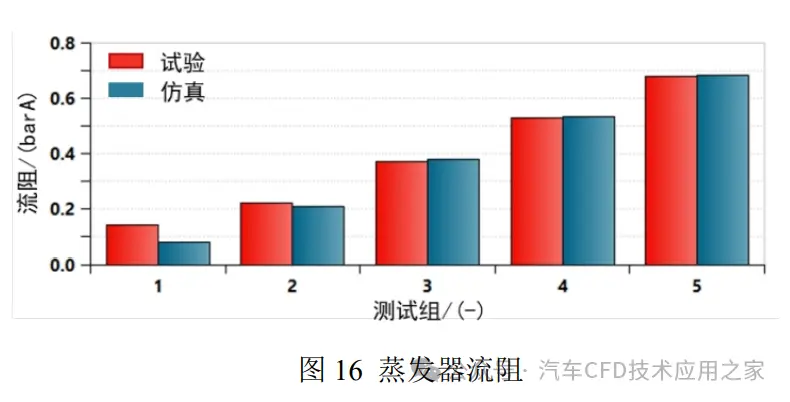
当电池包开启冷却时,冷媒回路与冷却液回路在 Chiller 中进行换热,其换热量与流阻的建模精度会 直接影响到电池温度变化的准确性,同时也会影响到制冷过程中压缩机、水泵等功率部件的能耗情况, 详细标定结果如图 17、18 所示。
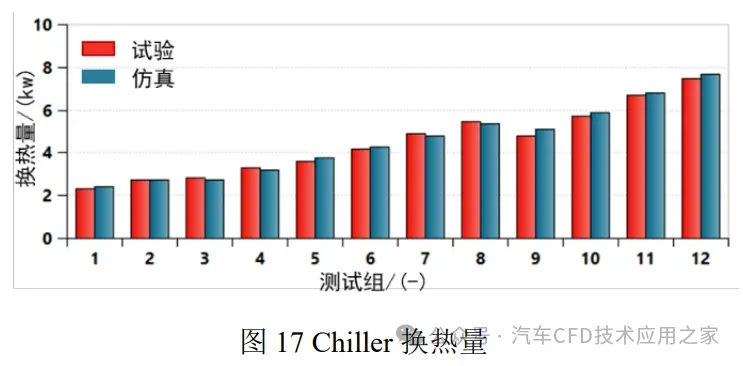
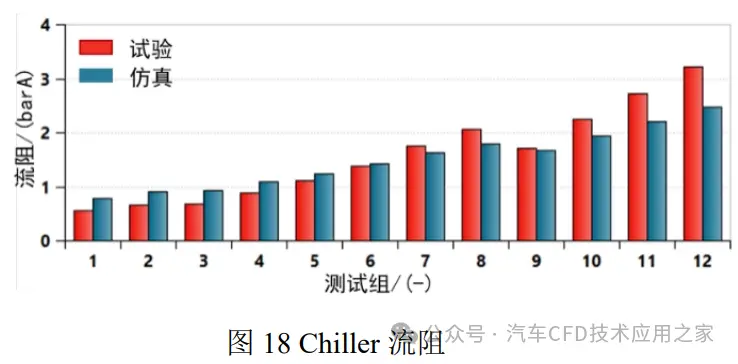
1.4 控制策略
在 MATLAB/Simulink 中建立基于规则的整车 TMS 控制器模型,对整车热管理系统中的压缩机、水泵、 风扇等零部件进行控制,用以维持乘员舱、电驱、电池等子系统正常运行的需要。整车 TMS 控制器模型 如图 19 所示,图中绿色端口为输入信号,红色端口为输出信号,圆形端口代表整个控制器的输入输出, 方形端口则仅为内部的输入输出。由图可见,控制器模型主要分为两大部分,左半部分为输入信号模块, 可以导入试验数据进行开环控制验证或者切换为闭环控制;右半部分为子系统控制器模块,涉及各个子系 统的控制逻辑,主要包含压缩机,PTC,鼓风机,风扇等 8 个子模块。部分子模块的输出信号不仅是整个 控制器的输出信号,也将作为另外某些子模块的输入信号,为其控制逻辑提供输入。
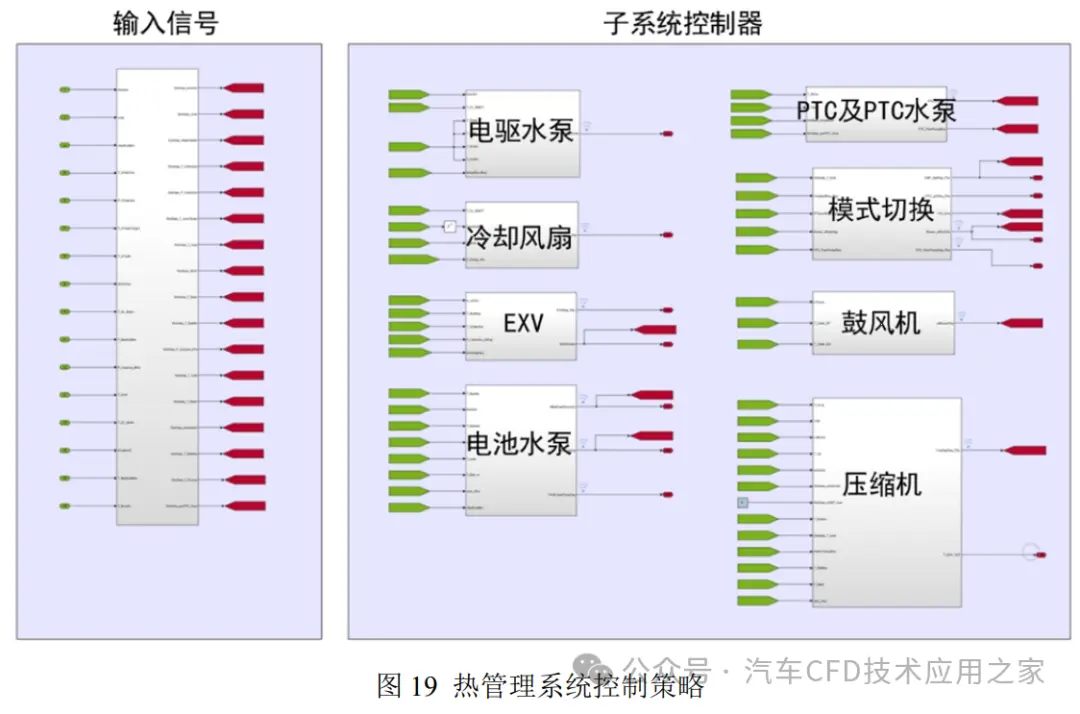
02、环境舱能耗及续驶里程试验
为了验证仿真分析结果的精度和准确性,根据国家标准《GB/T 18386.1-2021 电动汽车能量消耗量和 续驶里程试验方法第 1 部分:轻型汽车》在环境模拟仓内进行了高温工况下的能耗试验,试验过程如图 20 所示。
试验车辆前后拖钩处分别系上铁链和绑带,限制车辆的前后左右平面位移,使其固定在转毂台架上, 只具有轮端处的转动自由度。为了更好地探究该车型在高温地区下的能耗情况,环境仓气温设定为 38℃, 车顶最高点平面处的太阳辐射强度为 850W/m^2。从车辆 CAN 总线系统中提取车速、电池包电压、电池包 电流、SOC 等信号供仿真结果与试验数据对比使用。除此之外,对车俩结构进行改制,在主要的能耗元件 如压缩机、风扇、鼓风机、水泵等导线位置处布置了电压、电流传感器;在冷媒回路主要元件如压缩机、 冷凝器、蒸发器等管路进出口位置处管壁上布置了温度传感器;在冷却液回路主要元件如电驱、散热器、 电池包等管路进出口位置处也布置了温度传感器,同时还布置了流量传感器测量电驱和电池冷却回路的体 积流量。
采用常规工况法进行测试,试验循环为 CLTC-P 循环,如图 21 所示。该试验循环主要分为低速段、 中速段及高速段三个部分,分别表征市区、城郊及高速下的运行场景。试验车辆的最高车速高于试验循环 的最高车速 114Km/h,因此无需对速度曲线进行尺度缩减。试验时采用自动驾驶机器人控制车辆的加速及 制动踏板,使整车速度与试验循环保持跟随,误差控制在±2Km/h 以内。
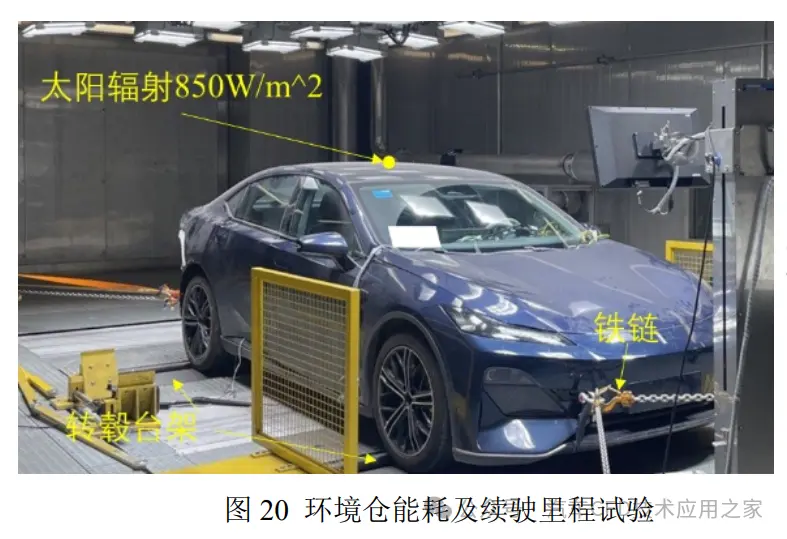
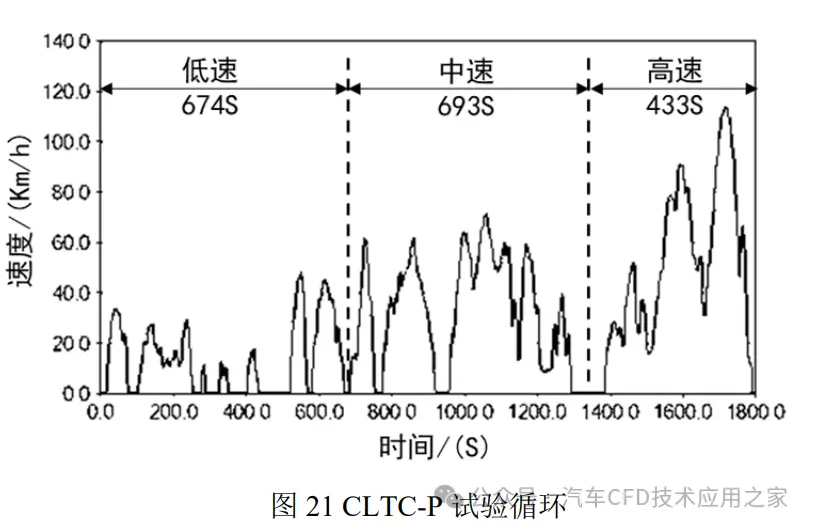
03、能耗及续驶里程分析
需要首先说明的是,在对试验车辆热管理系统改制布置传感器时,HVAC 系统中风道的漏风量未得到 良好的控制,过大的漏风量影响了原本设定的乘员舱内循环条件,导致高温工况下乘员舱的热负荷偏大, 难以在短时间内达到热平衡以及要求的乘员舱温度。因此本文仅选取热平衡附近的一段稳态过程进行仿真 分析与试验测试的对比展示。选取的稳态过程时长 24000S,约 13 个 CLTC 循环,期间历经了 5 次电池制 冷过程。
动力学及电力学仿真与试验结果对比如图 22 至 25 所示。图 22 展示了试验与仿真在车速上的对比。为了进一步验证里程,提取CAN总线系统中的行驶里程数据,与仿真结果的对比分别为187.1km和187.9km, 吻合良好。图 23 展示了电池包电压随时间变化的情况,随着放电深度的增大,怠速时的电池包端电压从 450V 下降至 390V,降幅约 13%,整体下降趋势与单颗电芯的 OCV 开路电压曲线类似。如图 24 所示,仿 真电池包电流与试验测量得到的电池包电流曲线吻合良好,图中电流为正代表放电情况,电流为负代表制 动充电情况。在该稳态过程中,试验车辆的整体需求功率大致不变,因此随着电池包端电压的减小,试验 与仿真的电池包电流均有所增大,同时也可以看到在绝对值上正向电流峰值比负向电流峰值更大,在稳态 阶段的末尾处正向电流峰值约 130A,而此时负向电流峰值不到-100A。整个稳态过程,试验与仿真的电池 包 SOC 变化范围分别为 87.6%~25.3%和 87.7%~25.8%,一致性良好。试验与仿真的 DC/DC 输出端电压均 为 14.4V,图 25 展示了其电流的对比情况,两者的平均电流分别为 62.3A 和 63.3A,基本相当。
图 26 至图 31 展示了空调系统、电池及电驱系统的热力学对比结果。压缩机转速及功率的对比如图 26 所示,在乘员舱单独制冷时,由于前文所述漏风量偏大的问题,压缩机转速在 4500rpm~5000rpm 的范围内 来回波动,整体处于较高水平;当电池包开启冷却时,压缩机转速在更大的 4000rpm~6500rpm 范围内变化, 接近压缩机的性能极限。观察下方压缩机的功率曲线,可以看出压缩机的功率与转速紧密相关,在乘员舱单独制冷时,功率保持在 2000W 左右,而当电池包开启制冷时,瞬时峰值功率可达 3200W 以上,增幅明 显。压缩机的进口及出口压力对比如图 27 所示,乘员舱单独制冷时的进、出口压力均低于电池包同时制 冷时的进、出口压力,这与图 26 所示的压缩机转速变化趋势保持一致。乘员舱的温度如图 28 所示,达到 热平衡后,乘员舱的温度稳定在 29℃左右,电池开启冷却后,受制冷剂流量分配的影响,有约 3℃的增幅。蒸发器出口风温方面,如图 29 所示,单独给乘员舱制冷时,稳定在 4℃左右的较低水平,满足乘员舱的制 冷需求。电池包开启冷却之后,蒸发器出口风温增幅 11℃,来到 15℃左右的较高水平,因此也进一步造 成了前述乘员舱温度升高的现象。图 30 展示了电池包最高最低试验温度与仿真平均温度的对比情况。由 图可见,电池包最高温度达到 41℃之后,便会执行电池冷却动作,而当最高温度下降至 38℃时,则会结 束电池冷却动作。3℃的温控范围,避免了电池冷却的频繁开启与关闭。总体而言,电池降温的速度远高 于升温的速度,每大约 4000S 会触发一次电池冷却,而一次电池冷却则持续约 550S。电驱进水口及定子温 度的对比如图 31 所示。平衡状态下进水口的温度保持在 53℃左右,同时也受压缩机转速波动的影响,当 同时开启电池制冷时,压缩机转速升高,散热器进风温度也升高,导致其换热量下降,最终使得进水口温 度升高至 57℃左右。电驱定子的温度在 58℃至 72℃较大范围内波动,曲线变化趋势与车速明显相关,车 速越高电驱功率越大,发热量也越大,又由于定子本身热容较小,因此温度变化更加明显。
基于上述仿真分析结果,绘制整车能量流分布如图 32 所示。总体而言,由蓝色虚线方框所代表的电 池包与外界环境的能量交换形式有三种,分别为机械能,电能和热能,均以橘黄色框图表示。其中,机械 能损失项以实线框图表示,包括风阻、滚阻和内阻损失;电能损失项以虚线框图表示,包括电池包净放电、 压缩机和 DC/DC 所代表的低压负载;热能损失项以点划线框图表示,包括电驱驱动损失、回收损失以及 电池包的充电损失和放电损失。放电损失、净放电以及充电损失之和代表整个能量流动过程中电池与外界 环境交换的能量之和,而单独的净放电则代表蓝色虚线方框,即电池包本体之外所有的能量损失项总和。
各能量损失项的占比及排序如图 33 所示。压缩机所代表的高压负载以超过 30%的比例排序第一,同 时 DC/DC 代表的低压负载也因为鼓风机、风扇、水泵等零部件的影响,以超过 18%的比例排序第二。由 图可见,本次试验过程中热管理系统整体呈现出较高的能耗占比。
04、结论
本文基于 AMESim 提供的多物理场仿真环境,搭建了某纯电动汽车在高温工况下的整车功热耦合能量 分析模型,对动力学系统、电力学系统和热力学系统等各子系统的能量消耗情况及占比进行了深入研究。同时,在环境仓内进行了同等工况下的整车能耗及续驶里程试验。仿真分析结果与测试数据吻合良好,证 明了本文所述电动汽车能耗分析方法的有效性,为后续进一步探究各项能耗优化措施提供了基础。概括而 言,总结出以下结论:
1,本文所述基于 AMESim 搭建的功热耦合能量分析模型具备一定的仿真精度,电动汽车能耗分析方 法具备一定的有效性,对于各种能耗优化措施给续驶里程带来的提升效果可以进行仿真验证;
2,整车能量流动过程以机械能、电能、热能三种形式为主,机械能的损失主要体现在风阻、滚阻和 内阻上,电能的损失主要体现在高压负载和低压负载上,而热能的损失主要以电驱的驱动及回收损失为主, 电池充放电损失占比较小;
3,高温工况下,热管理系统整体能耗占比较高,并且以电能形式为主。压缩机、风扇、鼓风机、水 泵等众多热管理系统元件的运行造成了这一现象,后续针对高温工况的能耗优化,可重点从基于效率的零 部件选型或者最优控制策略入手。
免责声明:文章来源周帅 1,2,刘怀举 1,朱才朝 1,禹慧丽 2,严旭 2,严俊杰 2. 电动汽车高温工况功热耦合能量分析与研究. 中国汽车工程学会汽车空气动力学分会学术年会,2024
来源:汽车CFD热管理