作为底盘系统的关键部件,减振器性能直接影响车辆的驾乘性能。由于减振器结构参数繁多且耦合性高,在传统开发流程中,减振器调校对工程师的系统建模能力和对复杂耦合机理理解的要求很高,往往依赖“经验+反复试验”的试错模式,这不仅耗时数月,更将产生高昂成本。如何高效、精准地建立减振器的模型,并实现整车仿真应用的系统化优化,一直是行业关注的问题。
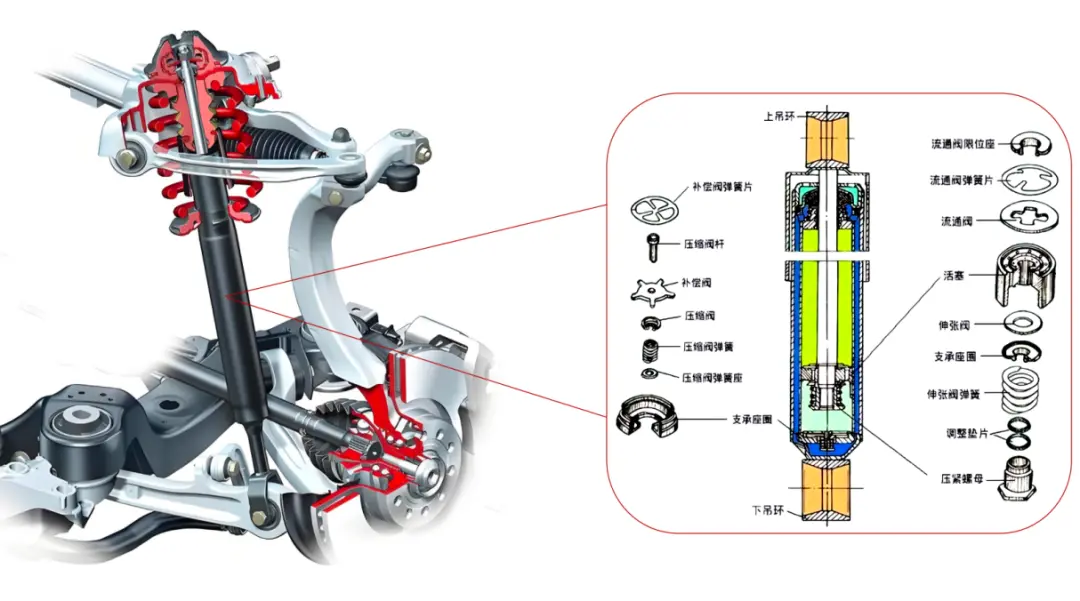
图 汽车减振器结构示意
相较于依赖工程师经验积累的传统开发模式,AI技术在减振器建模与整车仿真领域展现出突破性优势。AI技术擅长挖掘复杂数据间的高维非线性关系,发现传统建模方法难以识别的隐含关系,为减振器建模和整车仿真提供全新的智能化解决方案!
工程院人工智能减振器建模系统
中汽中心工程院融合AI技术与减振器建模开发,依托大量试验数据与物理理论约束,开发了基于深度学习算法的人工智能减振器建模软件。该软件面向汽车底盘不同开发阶段,集成了两大减振器建模工具,用于整车开发过程中减振器快速调校和减振器外特性高精度仿真,覆盖汽车开发过程中减振器的参数优化、性能评估、仿真验证等关键环节。
核心功能模块
(1)减振器人工智能建模工具
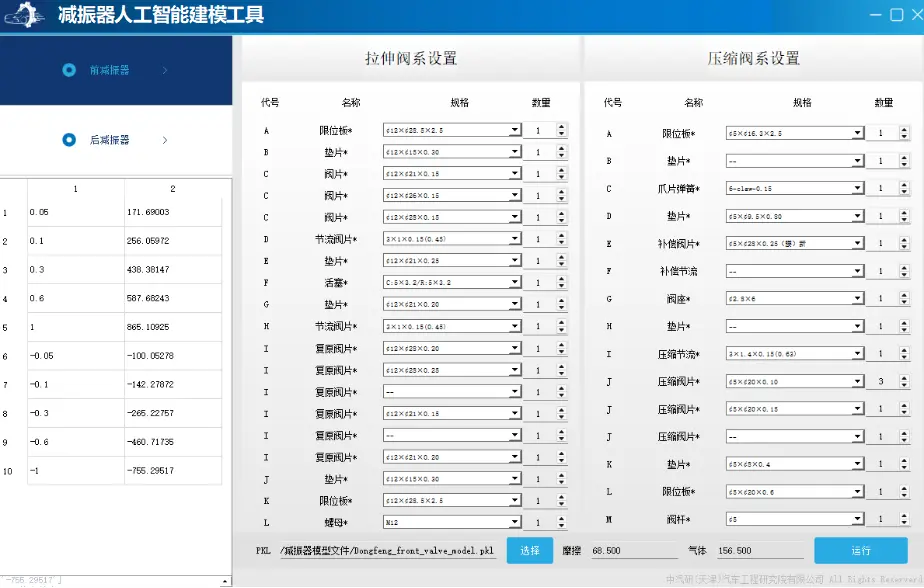
该工具以被动型减振器为对象,支持底盘调教方案的快速评估。底盘调校工程师只需要输入减振器阀系的安装规格参数,即可智能预测该结构下的减振器速度特性曲线,实现减振器结构与阻尼力的数据化表达。该工具的外特性预测结果相较减振器台架测试结果准确率达90%以上。
(2)减振器外特性高精度建模工具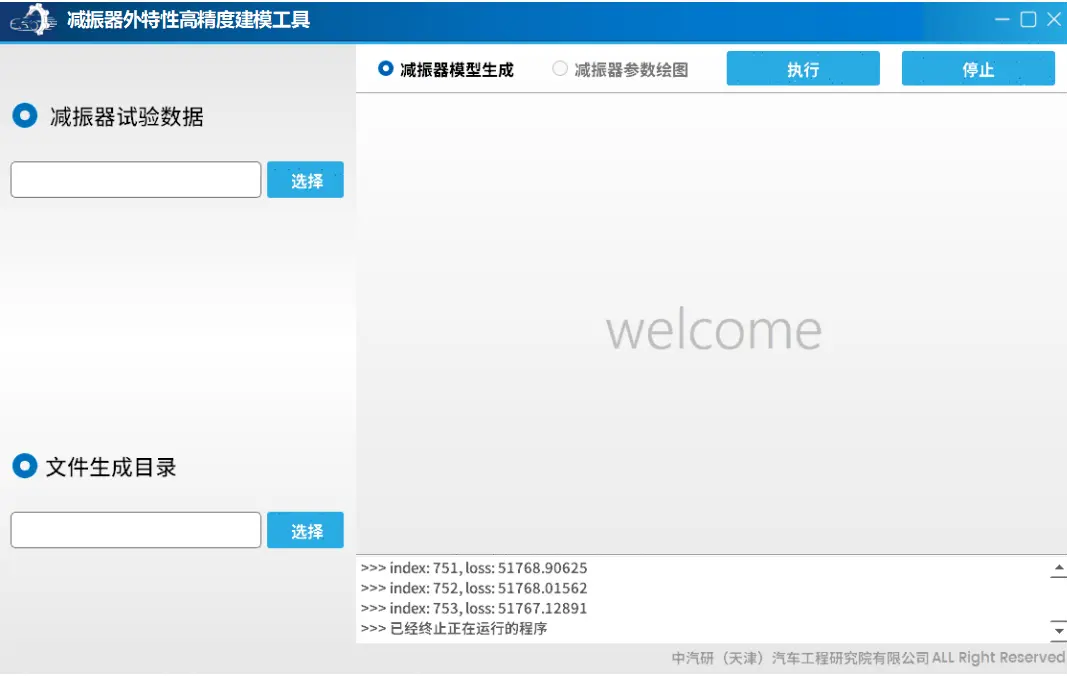
减振器外特性高精度建模工具将位移、速度双重参数共同作为阻尼力控制要素,使得模型仿真真实复现整车运动状态,提高整车动力学载荷仿真精度。与此同时,将参数化的减振器动力学模型集成到整车动力学仿真软件中,从而将整车的动力学性能和减振器的内部结构联系起来。突破传统阻尼力样条曲线仿真瓶颈,增加数据取值丰富度,相较传统仿真模式整车载荷精度提升大于5%。

图 减振器外特性3D图形
人工智能减振器建模系统对加快减振器设计开发速度,降低设计和试验费用,提高减振器设计水平和制造质量,提高车辆行驶平顺性、操作稳定性和乘坐舒适性都将产生积极推动作用。工程院研发团队将围绕减振器建仿真问题,打造全流程的数据驱动与物理约束融合的智能建模体系,实现从试验数据采集、参数辨识、模型训练到整车级仿真应用的闭环优化,提高减振器调校的效率与准确性,为整车开发提供更加高效、精准的系统化解决方案。
我们诚挚邀请行业同仁垂询与试用,期待与各位行业伙伴携手合作,共同探索前沿技术,攻克关键难题,推动减振器建模与整车仿真的智能化升级,共创行业智能仿真新时代!
来源:中汽中心工程院