一.研究背景
世界汽车工业发展面临三大问题:节能、环保、安全
汽车轻量化是节能与环保的重要方法和途径
轻量化与汽车制动安全、操纵稳定性、舒适性相关
整车轻量化:
1、降低排放的有效途径:
世界铝业协会数据:汽车自重每减少10%,排放降低5%-6% 欧盟将实现CO2排放控制目标的基础确定为汽车的小型化与轻量化 美国“新一代汽车共同开发计划”(PNGV)将汽车轻量化列为汽车节 能减排三大技术措施之一。
2、整车经济性提高的重要方法:
研究表明,约75%的油耗与整车的重量有关,降低汽车重量就可 有效降低油耗及排放;对商用车的研究表明,汽车重量每减少100Kg, 油耗可降低6%-7%.
3、提高运输效率,符合我国可持续发展要求:
汽车的轻量化符合国家节能减排战略和中长期科技发展规划的要求 我国原油对外依存度为60%.
二.轻量化设计方案
驱动桥简介
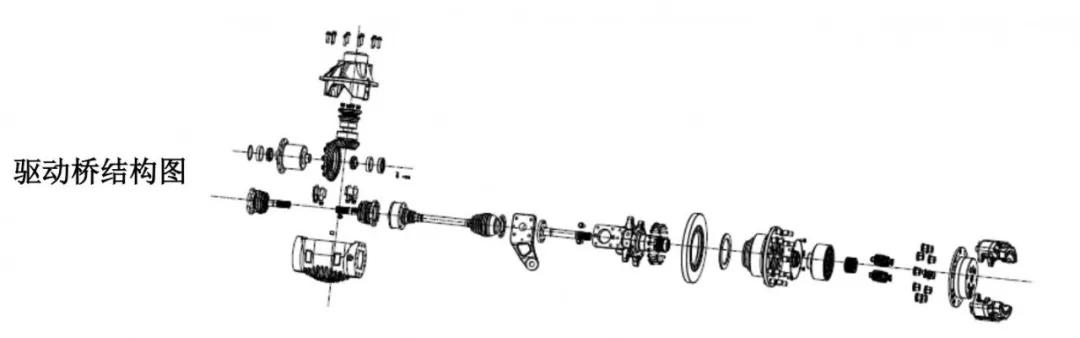
驱动桥功能
①将传动装置传来的发动机扭矩通过主减速器、差速器、 半轴等传到驱动车轮,实现降速増扭;
②通过主减速器圆锥齿轮副或双曲面齿轮副改变转矩的传递方向;
③通过差速器实现两侧车轮差速作用,保证内、外侧车轮以不同转速转向;
④通过桥壳体和车轮实现承载及传力作用。
本文将以某自主品牌越野车车型X 为蓝本 ,以车型X的驱动桥为例讲述 轻量化设计,并应用三维软件和有限元对驱动桥进行分析计算,最后通过台架以及实车试验验证本文所述车型X轻量化方案的可行性。
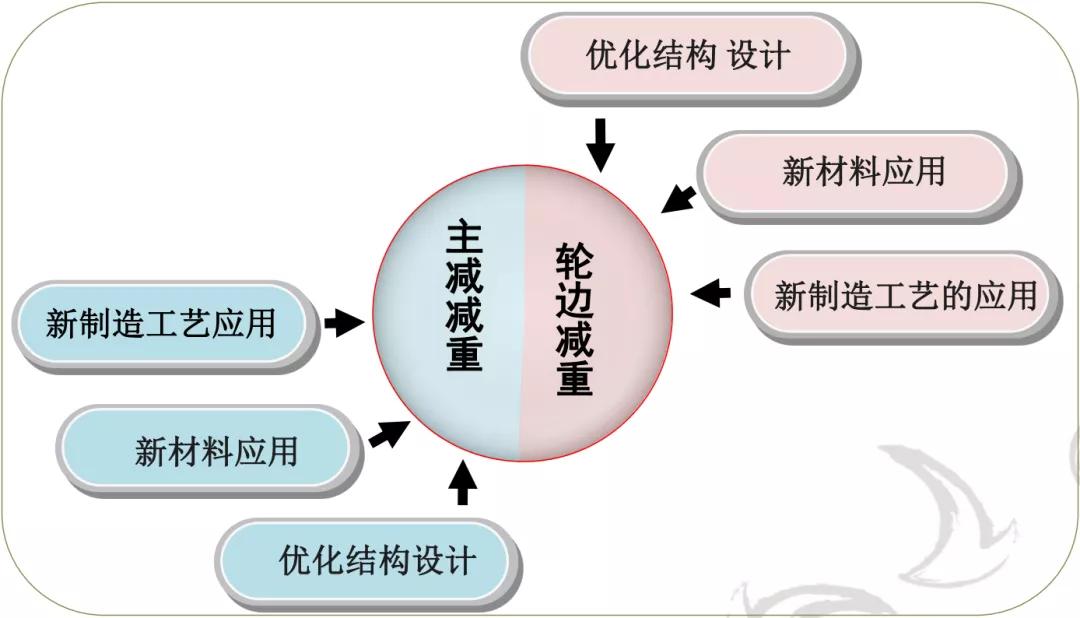
主减速器减重方案
用较小的尺寸和最轻的质量,设计制造出承载能力强,轻量化的主减速器,可 以降低整车噪声、提高整车舒适性和通过性,还减小了材料的使用和自身功耗。
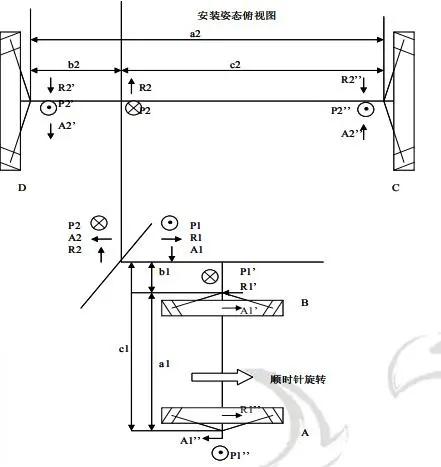
齿轮机构
齿轮尺寸优化
• 通过过优化主减速器、轮 边减速器速比,原则:适当 提高行星齿轮轮边速比,减 小主减速比;
• 优化齿轮模数,在保证强 度要求的前提下,缩小齿轮 模数,减小齿轮尺寸;
齿轮材料
• 采用性能更优的20CrMoH, 代替20CrMnTi,表面硬度更高, 心部韧性更佳,渗碳后表面性能提升;齿轮工艺
• 采用强力喷丸表面强化技 术,可进一步提高其扭矩传 递能力,喷丸表面强化后的 齿轮疲劳强度寿命最高可提升30%;
壳体
主减总成壳体重量一般占总成的30%左右,重量占比较大,通过优 化结构、材料以铝代钢,提高材料利用率;
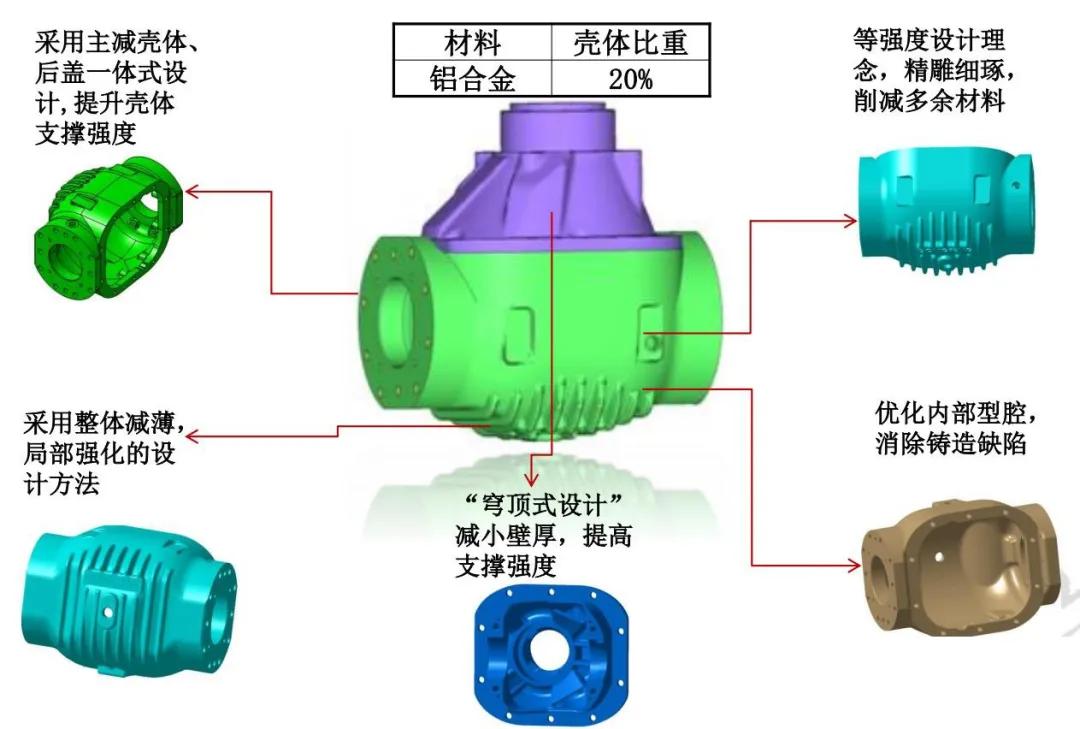
半轴
半轴为主减速器重要零件,对强度要求很高。
优化半轴与突缘连接方式
半轴与输出法兰一体式设计,采 用一次锻造成型,提升了半轴与法 兰的连接强度,同时优化了连接环 节,减少了连接螺母、O 型圈,缩 短了半轴长度,重量减轻;
优化设计后半轴 普通半轴
优化外廓尺寸
减小法兰直径和厚度; 切除多余的法兰边;
等强度设计,切除多余的材料;
优化半轴材料
采用高强度的采用代替传统材料
轮边减速器轻量化方案
轮毂 轮毂是轮胎内廓支撑轮胎的圆桶型的、中心装在轴上的金属部件,又叫做轮圈、钢圈、轱辘、胎 铃。轮毂根据直径、宽度、成型方式、材料不同种类繁多。
新技术、工艺
采用低压铸造技术,材料利用率 提升30%
采用齿轮仿真技术、减小行星齿 轮机构,减小整体尺寸
新材料应用
采用压铸铝合金
结构优化
等强度设计,对轴承支撑、车轮连接部位强化;
优化内部型腔,减小铸造缺陷,提升轮毂强度;
转向节
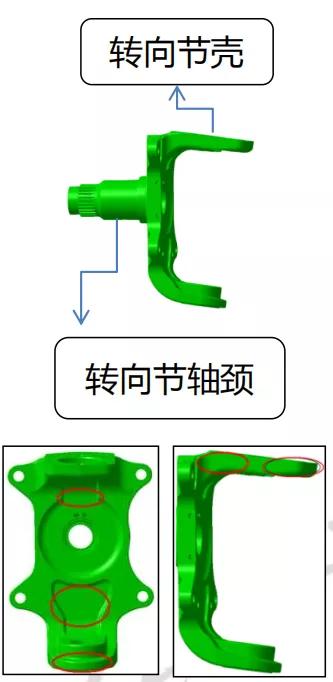
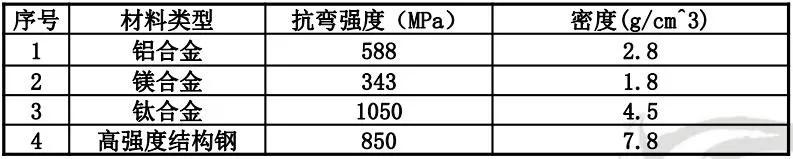
转向节的功用是传递并承受汽车前部载荷,支撑并带动前轮绕主销转动而使汽车转向。在汽 车行驶转状态下,它承受着多变的冲击载荷,因此,要求其具有很高的强度。
针对转向节受力情况进行划分:
- 把车轮与上下三角臂连接,并承受载荷冲击——转向节壳;固定齿圈并承受来自齿圈的扭矩—— 转向节轴颈 ;转向节壳采用轻质材料钛合金,而承受扭矩的轴颈采用合金结构钢。
- 对多余材料进行优化去除;
- 对高应力处进行加强,对受力较小的部位优化去除,造保证整体强度条件下,保证零件最轻;
- 高强度、轻量化材料的利用,钛合金比传统材料轻40%, 强度提升20%;
节臂
转向节臂又叫梯形臂,是转向传动装置的最后一级传力部件,转向节臂安装在左右转向节上, 另一端用球销和横拉杆连接。通过转向纵拉杆将其与转向摇臂连接起来,并实现转向。
1、措施
通过创新设计,通过提 高转向节臂与转下节壳 的配合间隙,提高连接 强度,缩小节臂结构
2、措施
调整转向节臂的安装位置, 改变转向节臂与转下拉杆的 空间角度,优化转向节臂的 受力,可缩小结构
3、措施
切除多余材料
4、措施
采用模锻工艺,提高材料 机械能力,提升零件强度
轻量化设计成果
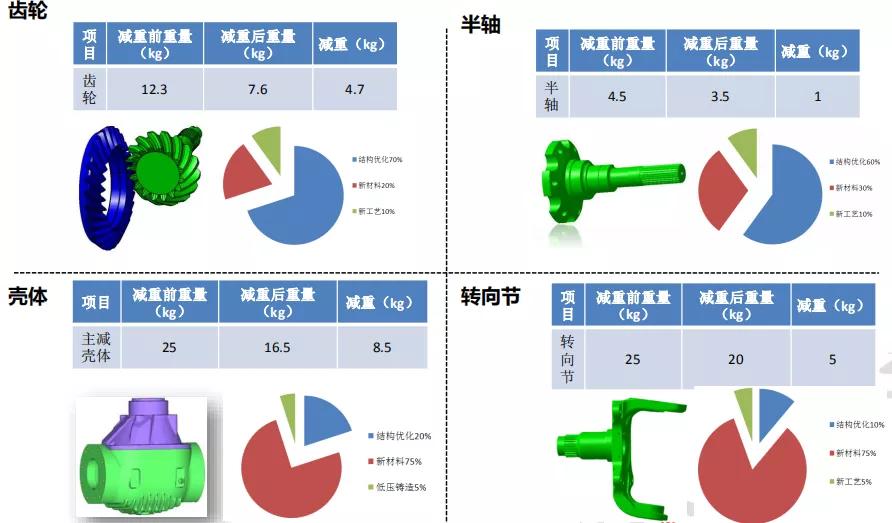
轻量化设计
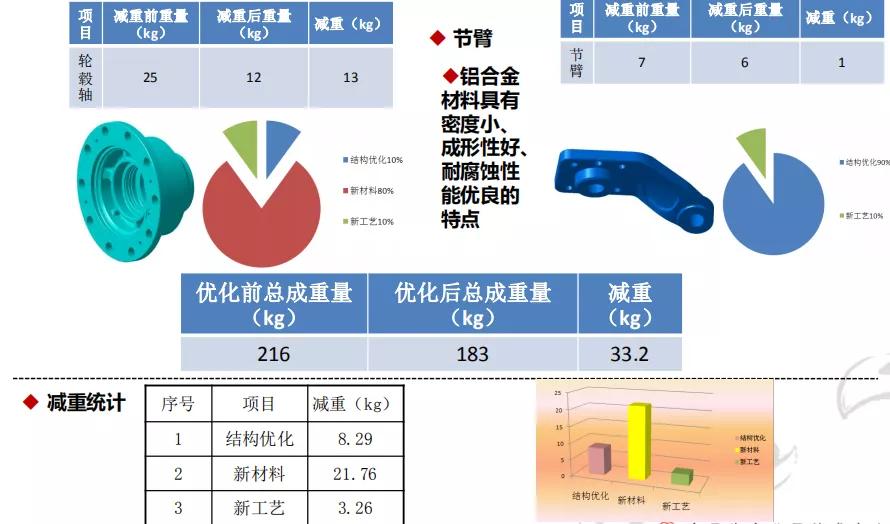
3、CAE分析
主减速器壳体CAE分析
受力分析
根据相关公式可得出主减速器壳体各轴承处的载荷;
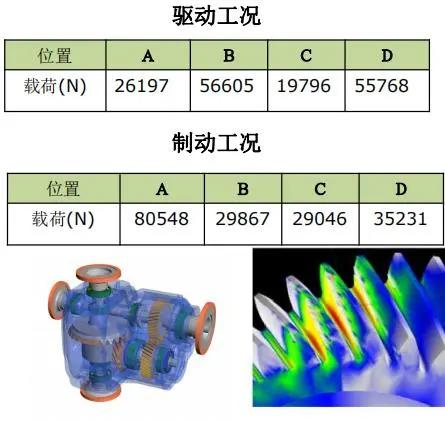
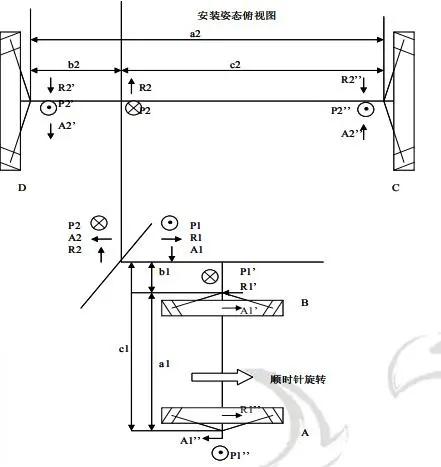
壳体建模
- 主减速器壳体有限元模型由1406672个单元组成;
- 在有限元分析过程中,对输出轴两侧螺栓孔进行全约束,采用二阶单元计算;
- 主减速器壳体的材料为ZL101 ,材料的屈服强度为190MPa。
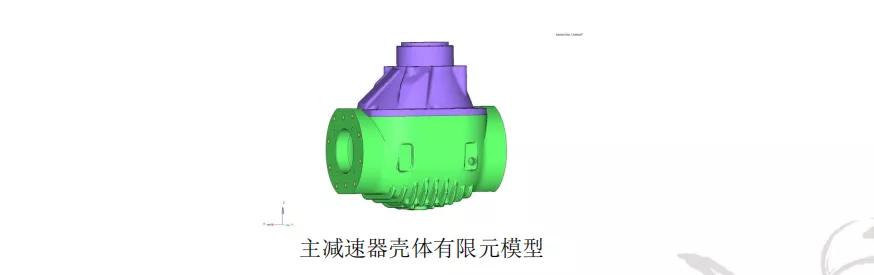
约束条件
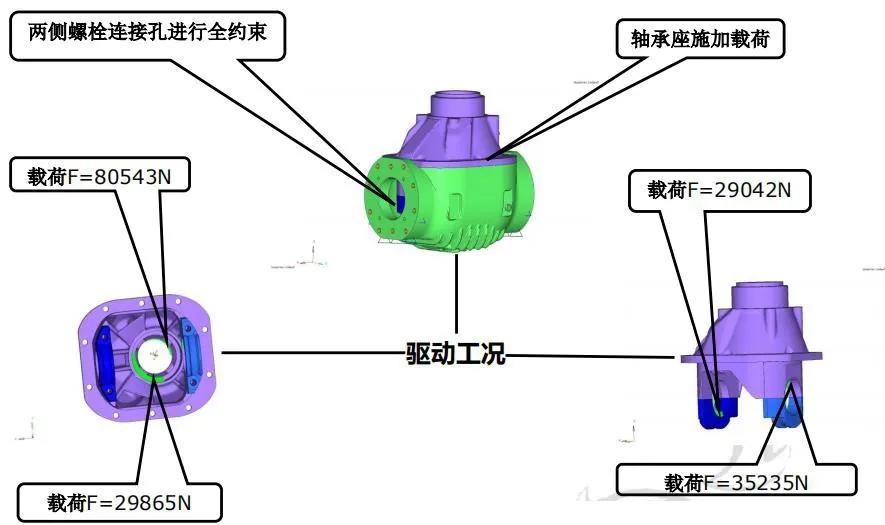
分析结果
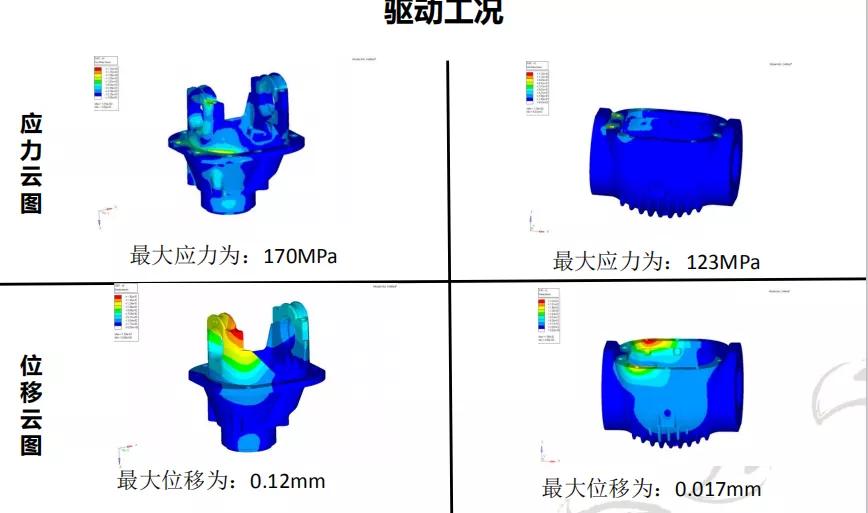
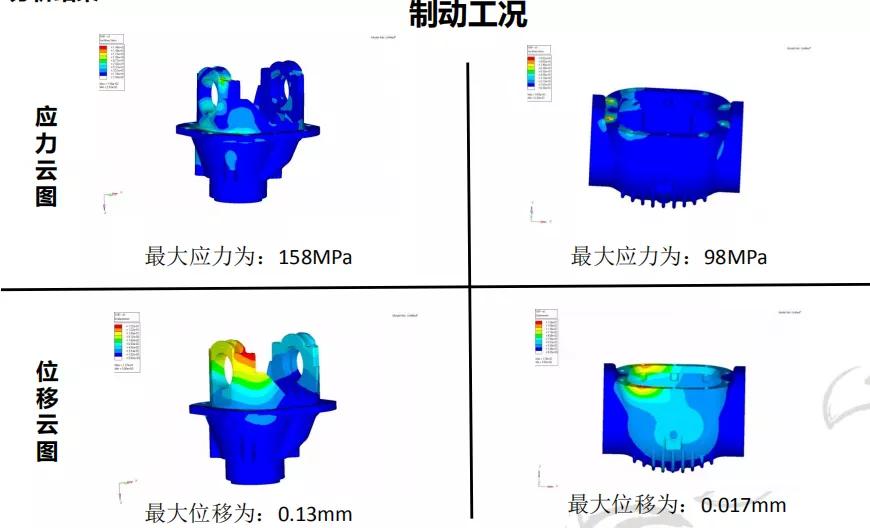
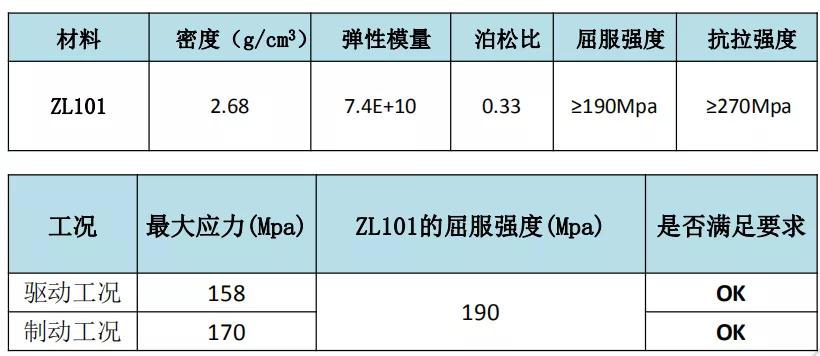
结论:车型X主减速器壳体的最大应力为170MPa,不超过材料屈服极限190MPa, 满足强度要求,轻量化的方案可行。
转向节与节臂CAE分析
转向节与转向节臂分析工况说明:
- 根据整车质心高度、轴荷等条件计算车轮所受载荷
- 前六个工况采用惯性释放方法,进行转向节强度计算;极限转向工况约 束轮心点,在上控制臂外点、下控制臂外点、横向推力杆外点加载;
- 前后轴转向节模型一致,且后轴荷大,此分析采用后轴计算;
- 前六个分析工况参考越野车结构零部件强度分析标准:EQCD-26。第七个极限转向工况为考虑自重及转向电机输出最大转向扭矩。
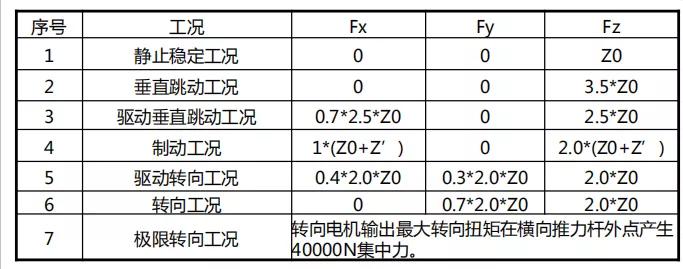
说明:Z0为静载状态下的轮荷,Z’为轴荷转移时产生的附加轮荷
节臂CAE分析
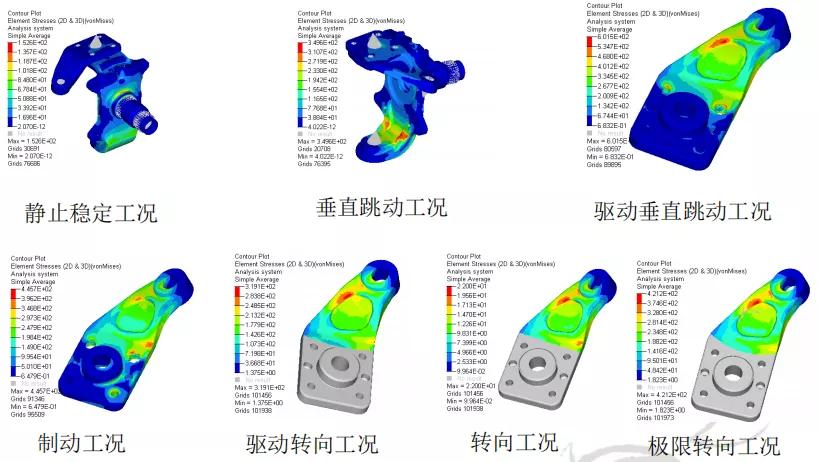
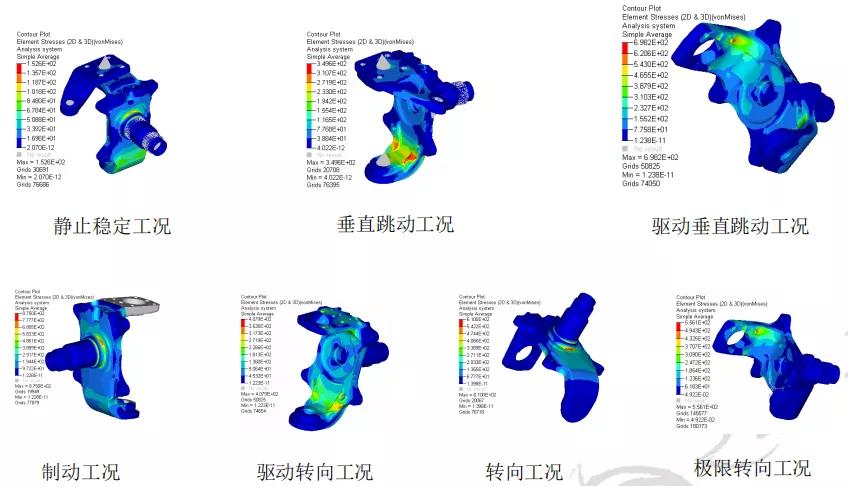
分析结果
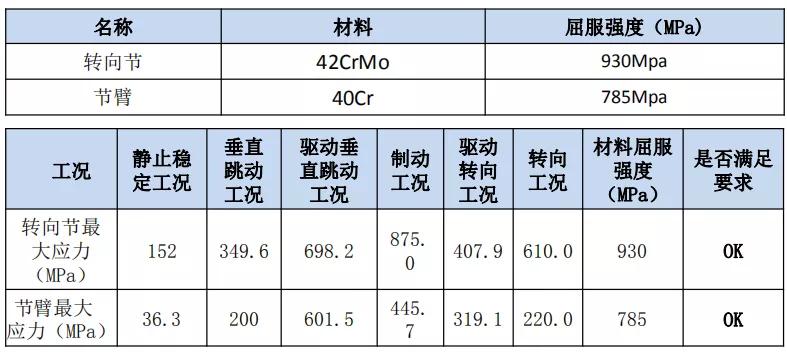
结论:车型X转向节的最大应力为875MPa,不超过材料屈服极限930MPa,满足强度要求;车型X转向节臂的最大应力为601.5MPa,不超过材料屈服极限785MPa,满足强度要求, 轻量化方案可行。
轮毂CAE分析
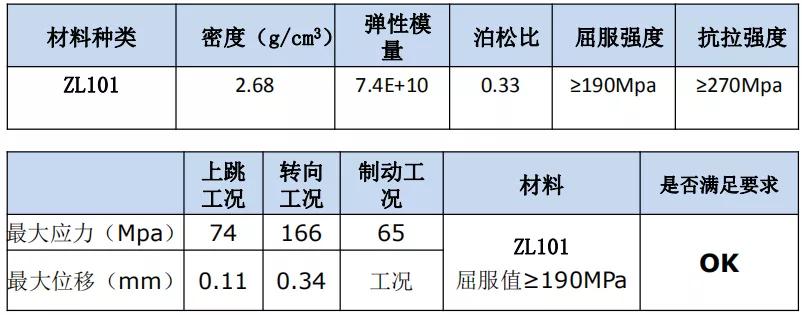
约束:约束连接制动盘螺栓孔位置全部自由度;释放轴承外圈节点沿轴向转动自由度;
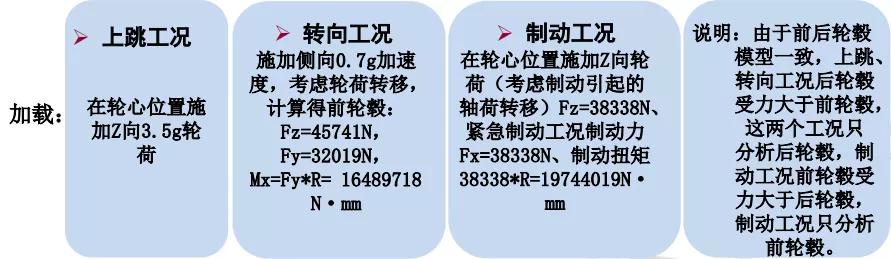
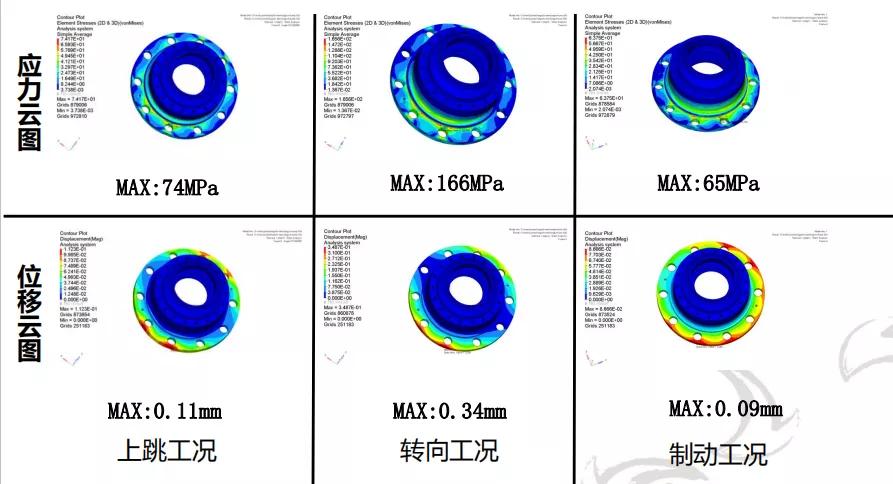
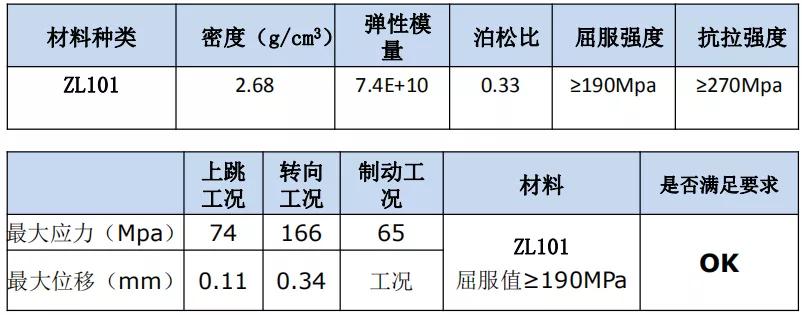
结论:车型X轮毂轻量化后的最大应力(166MPa)小于材料屈服值(190MPa),满 足强度要求。
4、台架与实车试验
总成台架试验
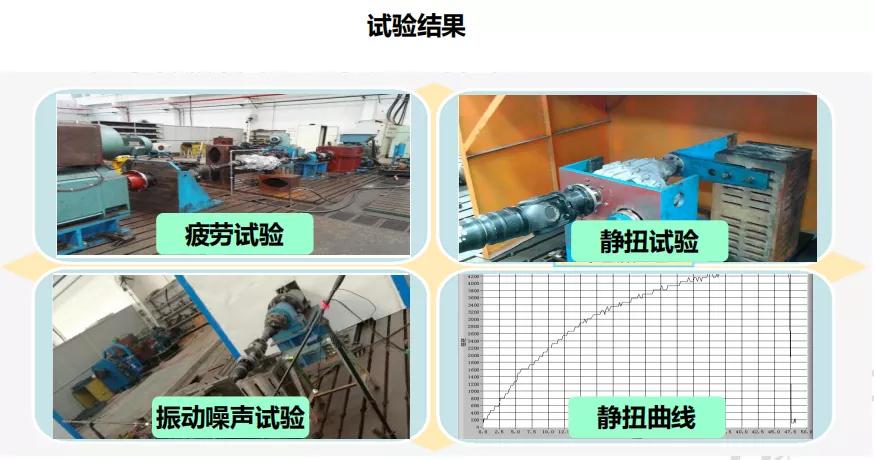
总成疲劳试验,标准与国外不一致,主减速器试验次数50万次以上,满足国标要求;
总成静扭试验,总成后备系数大于2.5,满足国标要求;
实车试验
按照前文设计的总成,进行了总成试制,并开展实车验证,满足使用要求;
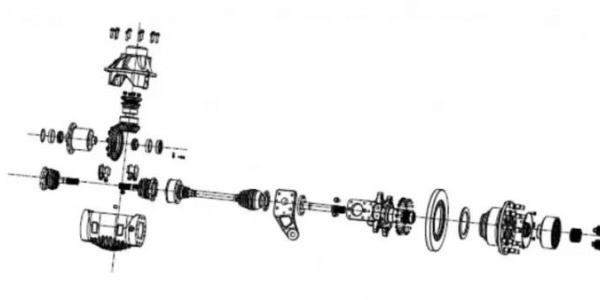
5、总结
1、轻量化是今后驱动桥结构设计的根本要求,利用CAE拓扑优化、运用新材 料、探索新工艺是有效的解决途径。
2、选取了驱动桥总成的4个典型部件进行了建模,进行了7个典型工况的力 学分析,计算设计结果并试验改进得出最佳方案,实现了各部件轻量化35kg, 并通过了台架与实车试验。
来源:汪振晓