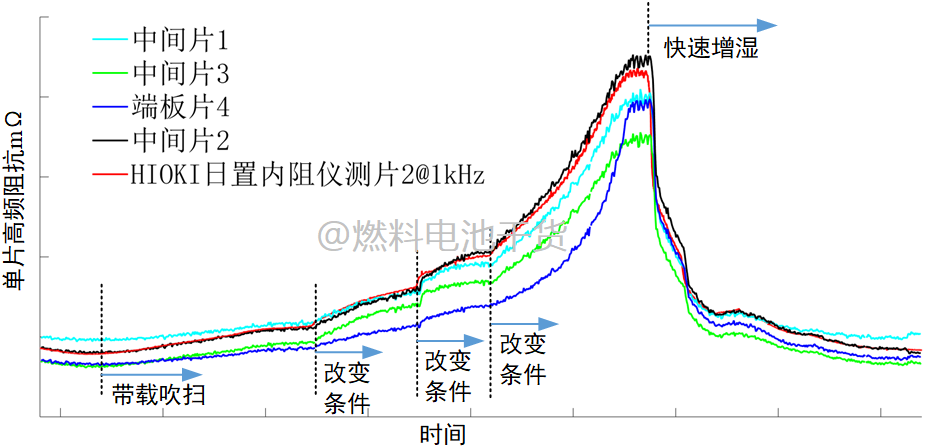
往期公众号内分享过《丰田燃料电池堆含水量实时测量技术分析》,细致介绍了丰田汽车公司在2010年前开发的燃料电池堆交流阻抗测量实施方法与应用场景,其中高频阻抗对应频率300 Hz、耗时约170 ms。通过查阅丰田专利和技术报道可以发现丰田Mirai在2014年已实现燃料电池单体层面的交流阻抗测量,并同时测量高频阻抗和低频阻抗(频率未知)。
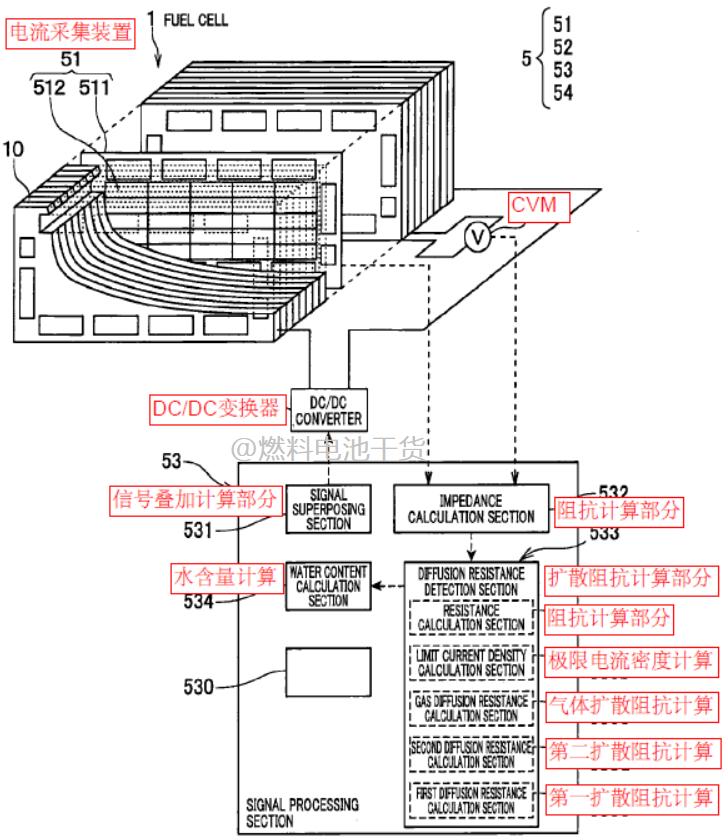
目前,国内在燃料电池发动机级别的交流阻抗测量与应用仍较为少见。从实施步骤看,『燃料电池干货』对国内交流阻抗测量技术的开发与应用情况进行了深入调查与分析。
施加交流电流扰动
据悉,在燃料电池发动机交流阻抗测量方面,目前尚无企业尝试施加交流电压扰动信号。据广泛和深入调研,国内外专利中关于施加交流电流扰动的实施方法主要有三大类。据悉,三类方法在国内燃料电池发动机企业中均有应用。
第一大类是在DC/DC变换器内部内嵌一套交流电流扰动施加硬件模块和电堆阻抗计算软件。其硬件模块与DC/DC变换器主拓扑无任何关联性,仅仅是将硬件模块与DC/DC变换器输入端并联,考虑零部件集成度、接插件、电安全、散热、成本等,将硬件模块内置于DC/DC变换器壳体内。其优点是:相较于DC/DC变换器控制,硬件模块控制较为简单、可操作性强(交流电流扰动频率和扰动幅值)。其缺点是:额外产品成本,只能测量电堆阻抗,硬件模块有功率消耗而使得系统效率有损失(实际上交流阻抗并没有实时且全时测量的必要性,仅仅取决于水含量动态变化的时间尺度)。
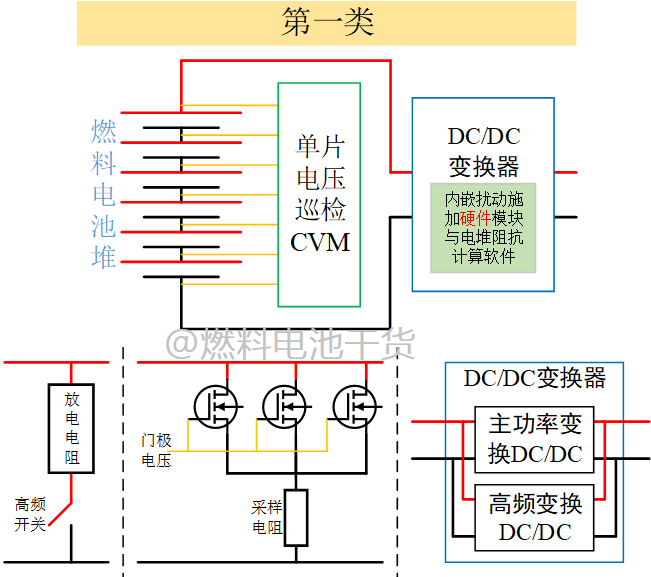
硬件模块有三种实现方式:第一种方式是高频开关+放电电阻,第二种方式是多个MOSFET并联+调控门极电压(类似于电子负载功能),第三种方式是主功率DC/DC变换器与高频DC/DC变换器并联(类似于多相并联式DC/DC变换器结构)。
第二大类在DC/DC变换器内部内嵌一套交流电流扰动施加软件和电堆阻抗计算软件。其优点是:DC/DC变换器硬件集成度高、成本低、系统效率高(无额外能量损耗)。缺点是:只能测量电堆阻抗,交流电流扰动频率控制难度高、扰动幅值控制难度高(取决于DC/DC变换器电路结构参数、被DC/DC变换器后端总线电压干扰、受限于电流传感器采样精度)。
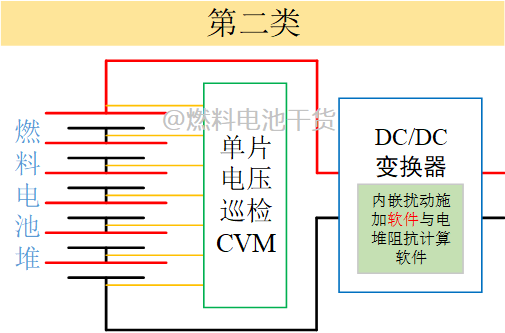
第三大类是在单片电压巡检CVM内部内嵌扰动施加硬件模块与单片阻抗计算软件。其优点是:降低了对DC/DC变换器软硬件控制要求,硬件模块控制较为简单、可操作性强(交流电流扰动频率和扰动幅值),可测量单片交流阻抗。其缺点是:硬件模块成本高,单片电压巡检兼具有执行器功能而对系统可靠性设计要求增加,交流电流扰动频率和幅值易于受到DC/DC变换器干扰(干扰程度不清楚)。其硬件模块种类较多,可参考日产汽车相关燃料电池专利。
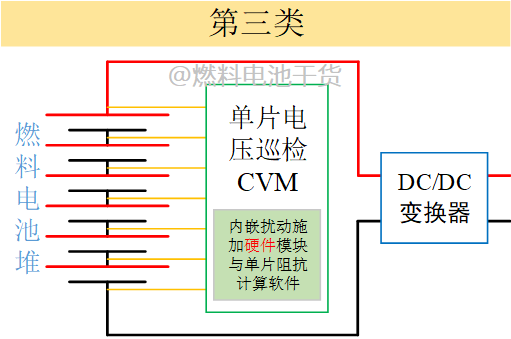
采集电流扰动和电压响应信号
以单片为例,单片稳态电压从0~1 V变化,而单片高频阻抗考虑水含量和温度影响以及实际应用场景,从开机输出电流到吹扫结束前变化范围应该在0.1mΩ~10mΩ之间,加之交流电流扰动幅值3A~5A,也就是单片交流电压响应幅值范围应该在0.3mV~50mV且是有目标频率要求的。从频带角度来讲,信号处理电路一般采用如下模式:光耦选通电路将单片正负极电压传递给高共模差分电路,高共模差分电路将单片正负极电压中的共模信号消除而仅剩差分电压(即为单片实际输出电压)并传递给带通滤波电路,带通滤波电路滤掉单片实际输出电压中的稳态电压、且提取出目标频率处的交流电压传递给增益调整电路,增益调整电路将不高于几毫伏的交流电压调整为几百毫伏甚至几伏的交流电压信号传递给中位电压调整电路,中位电压调整电路将正弦交流扰动信号的偏置电压调整为单片机A/D转换模块参考电压的1/2,再由单片机A/D模块实现单片交流电压采集。
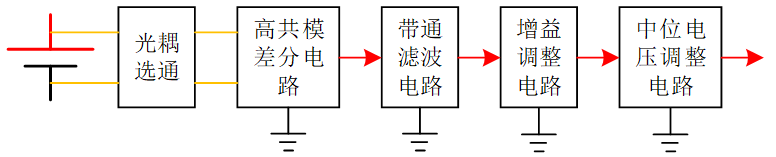
带通滤波电路带来的直接问题是,每次选通一个单片的时候,对带通滤波电路都是一个阶跃激励信号,带通滤波电路的动态响应延时则直接导致阻抗测量的时间延长。如果带通滤波电路是被高频阻抗测量、低频阻抗测量共用的,那么阻抗测量时间长度同步增加,对单片电压巡检的巡回电压采集时序安排产生影响。在系统设计时,必须综合考虑。
任何信号处理电路都面临幅值增益、相位延迟问题。对于阻抗计算而言,幅值增益和相位延迟尤为关键,对阻抗的幅值测量精度、相位精度要求较高。控制器的信号处理电路选用电阻可以做到1%甚至1‰的精度、选用电容可以做到10%甚至5%的精度,电子元器件误差累积和串联乘积是非常可怕的。在笔者看来,需要在每个交流阻抗目标频率处,对每一套信号处理电路进行幅值增益和相位延迟标定,每一套信号处理电路中包括电流采集电路(比如标定出某频率下幅值增益是100倍、相位延迟是10°)、多个单片电压采集电路(比如标定出某频率下幅值增益是31倍、相位延迟是57°)。
在批量产品中,电路标定方法是必不可少的,反过来影响单片电压巡检的生产效率和周期。对于多套单片阻抗测量电路来说,有三个基本要求:第一,燃料电池堆通道不变,任意单片电压巡检的阻抗采集通道互换时,两套电路的阻抗测量结果幅值误差在2%以内、相位误差在5°以内;第二,燃料电池堆通道不变,批量单片电压巡检中任意抽取两个进行测试,两套电路的阻抗测量结果幅值误差在2%以内、相位误差在5°以内;第三,在单片电压巡检的全生命周期内,任意一套单片阻抗测量电路的阻抗测量结果幅值误差控制在2%以内、相位误差控制在5°以内。关于第三点,可以考虑在单片电压巡检内配备自动校准功能模块,但影响单片电压巡检的电路集成效率、空间尺寸和成本。

除了单片电压巡检信号处理电路对阻抗相位产生误差以外,交流电流扰动采集和单片交流电压响应采集之间,也存在时间差,笔者目前总结了两种系统集成方案,主要取决于交流电流扰动信号采集功能所处的零部件。第一种方案是:DC/DC变换器集成交流电流扰动功能、电流传感器、交流电流扰动信号采集电路与电流软件信号处理,单片电压巡检CVM只集成单片交流电压信号采集电路与软件信号处理,由燃料电池系统控制器负责协调DC/DC变换器与单片电压巡检CVM的协同工作,那么DC/DC变换器必须具备硬线触发信号采集起始时刻同步的功能,确保交流电流扰动采集与单片交流电压响应采集之间是完全同步的、或者是存在固定时间差的。该方案缺点是相位同步难度大,优点是电流传感器内置于DC/DC变换器而不增加系统成本。
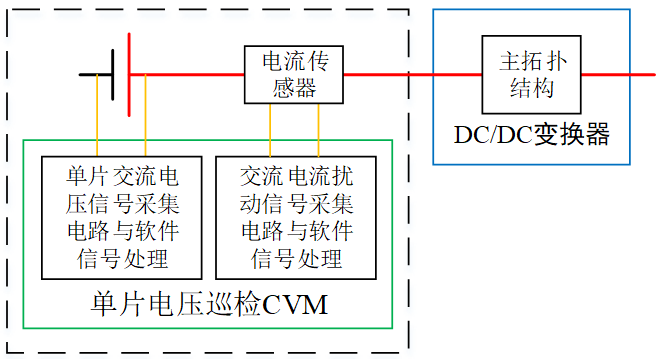
第二种方案是:单片电压巡检CVM同时集成了单片交流电压信号采集电路与软件信号处理、交流电流扰动信号采集电路与软件信号处理,DC/DC变换器仅负责交流电流扰动功能,由燃料电池系统控制器协同单片电压巡检CVM和DC/DC变换器协同工作,由单片电压巡检CVM实现单片交流电压信号与交流电流扰动信号采集同步。方案缺点是电流传感器必须内置于燃料电池堆PACK内部,电流传感器面临位置固定与接插件问题,同时对于DC/DC变换器来说,为实现输入电流闭环控制则必须要再次集成一个电流传感器,增加了系统成本,同时燃料电池堆内部高温易于导致电流传感器采集结果产生偏差(需要不断修正)。该方案优点是相位同步简单,单片电压巡检CVM可实现燃料电池堆输出电流采集。
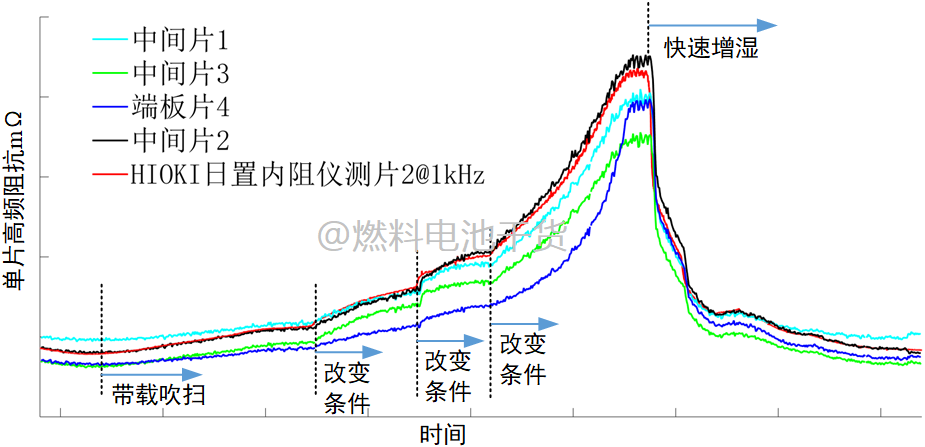
遵循前述思考过程、设计过程和分析过程,经过博士课题与博士后阶段7年时间,笔者目前已经分别在CVM级别和DC/DC级别实现了一部分在线交流阻抗测量和计算功能(高频与低频、单次用时170 ms),在燃料电池堆试验台架上进行了吹扫阶段四个单片阻抗测量,试验结果分享给大家。希望通过此次分享,促进国内燃料电池发动机级别交流阻抗测量的技术交流与发展。
来源:燃料电池干货
作者:洪坡